ಲೋಹಗಳಿಗೆ ಲೇಸರ್ ಕಟಿಂಗ್ ಮಾಡುವ ತಂತ್ರಜ್ಞಾನದ ಬಳಕೆಯು ಸುಮಾರು 60 ನೇ ದಶಕದಲ್ಲಿ ಪ್ರಾರಂಭವಾಗಿದೆ. ಆ ಕಾಲಾವಧಿಯಲ್ಲಿ ಯುರೋಪ್ ನಲ್ಲಿ ಇದರ ಬಳಕೆಯು ನಿಧಾನವಾಗಿ ವೃದ್ಧಿಸಿತು. ಭಾರತದ ಇಂದೋರ್ ಗೆ 1983-84 ರಲ್ಲಿ ಮೊತ್ತಮೊದಲಾಗಿ ಒಂದು ಮಶಿನ್ ತರಲಾಯಿತು. ಟೆಲ್ಕೊ ಕಂಪನಿಯು 1984-85 ರಲ್ಲಿ ಪ್ರೊಟೋಟೈಪಿಂಗ್ ಉತ್ಪಾದನೆಗೆ ಒಂದು ಮಶಿನ್ ಖರೀದಿಸಿತು. ನಿಜವಾಗಿ ನೋಡಿದರೆ ಭಾರತೀಯ ಉದ್ಯಮದಲ್ಲಿ ಲೇಸರ್ ತಂತ್ರಜ್ಞಾನದ ಬಳಕೆಯು ಆಗಲೇ ಪ್ರಾರಂಭಗೊಂಡಿತ್ತು.
ಆ ಕಾಲಾವಧಿಯಲ್ಲಿ ವಾಹನಗಳ ಉತ್ಪಾದನೆಯಲ್ಲಿ ಶೀಟ್ ಮೆಟಲ್ ಕತ್ತರಿಸಿ ಅದರಿಂದ ತಮಗೆ ಬೇಕಾಗಿರುವ ಕಚ್ಚಾ ಆಕಾರವನ್ನು (ಬ್ಲ್ಯಾಂಕ್) ತಯಾರಿಸಲಾಗುತ್ತಿತ್ತು. ಅದರ ನಂತರ ಅದಕ್ಕೆ ಯೋಗ್ಯವಾದ ಆಕಾರ ನೀಡಿ (ಫಾರ್ಮಿಂಗ್) ಹೆಚ್ಚುವರಿ ಇರುವ ಮಟೀರಿಯಲ್ ಕತ್ತರಿಸಬೇಕಾಗುತ್ತಿತ್ತು (ಟ್ರಿಮಿಂಗ್). ಇದರ ಡೈ ತಯಾರಿಸಲು ತುಂಬಾ ಸಮಯವು ಬೇಕಾಗುತ್ತಿತ್ತು. ಪ್ರೊಟೊಟೈಪ್ ಉತ್ಪಾದನೆಗಳಿಗೆ ಅದು ಪೂರೈಸುತ್ತಿರಲಿಲ್ಲ. ಅದಕ್ಕೋಸ್ಕರ ಆ ತಗಡುಗಳನ್ನು ಕೈಯಿಂದ ಕತ್ತರಿಸಲಾಗುತ್ತಿತ್ತು. ಅಲ್ಪ-ಸ್ವಲ್ಪ ಪ್ರಮಾಣದಲ್ಲಿ ಸಾಫ್ಟ್ ಟೂಲ್ ಗಳನ್ನು ಅಭಿವೃದ್ಧಿ ಪಡಿಸಿ ಫಾರ್ಮಿಂಗ್ ಮಾಡಲಾಗುತ್ತಿತ್ತು. ಆದರೆ ಅದರ ನಂತರ ಹೆಚ್ಚುವರಿಯಾಗಿ ಉಳಿದಿರುವ ಮಟೀರಿಯಲ್ ಕತ್ತರಿಸುವ ಸಮಸ್ಯೆಯು ಇತ್ತು. ಆದ್ದರಿಂದಲೇ ಟೆಲ್ಕೋ ಈ ಕಂಪನಿಯು ಇಂಗ್ಲೆಂಡ್ ನಲ್ಲಿರುವ ಒಂದು ಕಂಪನಿಯಿಂದ 3D ಲೇಸರ್ ಕಟಿಂಗ್ ಮಶಿನ್ ಖರೀದಿಸಿದರು. ಈ ಮಶಿನ್ ನಲ್ಲಿ ಬ್ಲ್ಯಾಂಕಿಂಗ್, ಟ್ರಿಮ್ಮಿಂಗ್ ಇಂತಹ ಪ್ರಕ್ರಿಯೆಗಳನ್ನು ಮಾಡಲಾಗುತ್ತಿತ್ತು.
ನಾನು ಟೆಲ್ಕೋ ಕಂಪನಿಯ ಉದ್ಯೋಗವನ್ನು ಬಿಟ್ಟು ಸ್ವತಃ ಒಂದು ಕಾರ್ಖಾನೆಯನ್ನು ಪ್ರಾರಂಭಿಸಿದೆ. ಕಾರ್ಖಾನೆಯನ್ನು ಪ್ರಾರಂಭಿಸುವಾಗ ಕಾಲಕ್ಕೆ ತಕ್ಕಂತೆ ಎಲ್ಲ ರೀತಿಯ ವ್ಯವಸ್ಥೆಗಳು ಇರುವುದು ಅತ್ಯಗತ್ಯ, ಎಂಬ ವಿಚಾರವನ್ನು ಮಾಡಿದೆ. ಅದರಲ್ಲಿ ಪ್ರಮುಖವಾಗಿ ಅತ್ಯಾಧುನಿಕವಾದ ತಂತ್ರಜ್ಞಾನವು ಇರಲೇ ಬೇಕು. 3D ಲೇಸರ್ ಮಶಿನ್ ತುಂಬಾ ದುಬಾರಿಯಾಗಿತ್ತು. ಎಲ್ಲ ರೀತಿಯಲ್ಲಿ ಈ ಕುರಿತು ಆಳವಾದ ಅಭ್ಯಾಸ ಮಾಡಿದ ನಂತರ ಫ್ಲೇಟ್ ಬೆಡ್ 2D ಮಶಿನ್ ಖರೀದಿಸುವ ಕುರಿತು ವಿಚಾರ ಮಾಡಲಾಯಿತು. ನಂತರ ಆ ಮಶಿನ್ (ಚಿತ್ರ ಕ್ರ. 1) ನಾವು ಆಮದು ಮಾಡಿದೆವು.
ಅದೇ ಸಮಯದಲ್ಲಿ ನಮಗೆ ಒಂದು ದೊಡ್ಡ ಕಂಪನಿಗೆ ಹೊಸ ವಾಹನಗಳಿಗೆ ಬೇಕಾಗಿರುವ ಭಾಗಗಳ ಬ್ಲ್ಯಾಂಕಿಂಗ್ ಮಾಡುವ ಕೆಲಸವು ಲಭಿಸಿತು. ಆಗ ಆರು ತಿಂಗಳ ಕಾಲಾವಧಿಯಲ್ಲಿ ತುಂಬಾ ಶ್ರಮ ವಹಿಸಿ ಅತ್ಯಾಧುನಿಕ ತಂತ್ರಜ್ಞಾನವನ್ನು ತಿಳಿದುಕೊಂಡು ಕೆಲಸವನ್ನು ಆರಂಭಿಸಲಾಯಿತು. ಪ್ರೊಟೋಟೈಪ್ ಗೋಸ್ಕರ ಬಳಸಲಾಗುವ ಈ ಮಶಿನ್ ನಲ್ಲಿ ನಾವು ಮಾಸ್ ಪ್ರೊಡಕ್ಷನ್ (ಬೃಹತ್ ಪ್ರಮಾಣದ ಉತ್ಪಾದನೆ) ಮಾಡಲಾರಂಭಿಸಿದೆವು. ಆಗ ಪರಿಸ್ಥಿತಿ ತುಂಬಾ ಸಮಾಧಾನಕಾರಕವಾಗಿತ್ತು. ಕಂಪನಿಯು ಮುಂಬಾಗಿಲಲ್ಲಿ ಟ್ರಕ್ ಸಾಲಾಗಿ ನಿಂತಿದ್ದವು. ಪಕ್ಕದಲ್ಲಿ ಮಟೀರಿಯಲ್ ನ ರಾಶಿ ಇರುತ್ತಿತ್ತು. ಅಲ್ಲದೇ ಮಶಿನ್ 24 ಗಂಟೆಗಳೂ ನಡೆಯುತ್ತಿತ್ತು.
ಒಂದೇ ಮಶಿನ್ ನಲ್ಲಿ ನಾವು ಒಂದೇ ವಾಹನದ 75 ವಿಧದ ಅನೇಕ ಭಾಗಗಳನ್ನು ತಯಾರಿಸುತ್ತಿದ್ದೆವು. ಉದಾಹರಣೆ, ಔಟರ್ ಡೋರ್ ಪ್ಯಾನೆಲ್, ಇನರ್ ಡೋರ್ ಪ್ಯಾನೆಲ್, B ಪಿಲರ್, C ಪಿಲರ್, ಟೇಲ್ ಗೇಟ್ ಇನರ್, ಟೇಲ್ ಗೇಟ್ ಔಟರ್, ಲೋವರ್ ಪ್ಯಾನೆಲ್, ಹೂಡ್ ನ ಇನರ್ ಮತ್ತು ಔಟರ್ ಪಾರ್ಟ್ ಮುಂತಾದವುಗಳು. ಸಾಮಾನ್ಯವಾಗಿ ಪ್ರತಿ ತಿಂಗಳಿಗೆ ನಾವು ಪ್ರತಿಯೊಂದು ಭಾಗದ 100 ಸೆಟ್ ತಯಾರಿಸಿದೆವು. ಸುಮಾರು ಐದು ತಿಂಗಳ ಕಾಲಾವಧಿಯಲ್ಲಿ ಕೆಲಸವನ್ನು ಮಾಡಲಾಯಿತು.
ನಿಧಾನವಾಗಿ ಪುಣೆ, ಮುಂಬಯಿ ಮತ್ತು ನಂತರ ಸಂಪೂರ್ಣ ದೇಶದಲ್ಲಿ ಈ ತಂತ್ರಜ್ಞಾನವನ್ನು ಎಲ್ಲೆಲ್ಲಿ ಬಳಸುತ್ತಾರೆ, ಹೇಗೆ ಬಳಸುತ್ತಾರೆ, ಇದರ ಉಪಯುಕ್ತತೆ ಏನಿದೆ, ಎಂಬುದರ ಕುರಿತು ಆಳವಾಗಿ ಆಭ್ಯಾಸ ಮಾಡಿದೆವು. ಅನೇಕ ಆಂತಾರಾಷ್ಟ್ರೀಯ ಕಂಪನಿಗಳಲ್ಲಿ ಈ ತಂತ್ರಜ್ಞಾನದ ಬಳಕೆಯು ರೂಢಿಯಾಗಿತ್ತು. ಇದರಿಂದಾಗಿ ನಮ್ಮ ಗ್ರಾಹಕರಿಗೋಸ್ಕರ ಹೊಸ ತಂತ್ರಜ್ಞಾನವನ್ನು ಬಳಸುವ ಸುವರ್ಣಾವಕಾಶವು ಬೇಗ ನಮಗೆ ಸಿಕ್ಕಿತು. ಇನ್ನಿತರ ತಂತ್ರಜ್ಞಾನವನ್ನು ಹೋಲಿಸಿದಲ್ಲಿ ಲೇಸರ್ ತಂತ್ರಜ್ಞಾನವು ತುಂಬಾ ವೇಗವಾಗಿ ಸ್ಥಿರವಾಯಿತು. ಕಡಿಮೆ ವೇಳೆಯಲ್ಲಿ ಅದು ತುಂಬಾ ಪ್ರಸಿದ್ಧವಾಯಿತು. ಚಿಕ್ಕ ಆಕಾರ ಯಂತ್ರಭಾಗಗಳು, ಪ್ರೊಟೊಟೈಪ್ ಇವುಗಳಿಗೋಸ್ಕರ ಲೇಸರ್ ತಂತ್ರಜ್ಞಾನದ ಬಳಕೆಯು ಪ್ರಾರಂಭಗೊಂಡಿತು.
ಲೇಸರ್ ಪ್ರಕ್ರಿಯೆ
ಲೇಸರ್ ಇದೊಂದು ಉಷ್ಣತೆಗೆ (ಥರ್ಮಲ್) ಸಂಬಂಧಪಟ್ಟ ಪ್ರಕ್ರಿಯೆಯಾಗಿದೆ. ಗ್ಯಾಸ್ ಕಟಿಂಗ್ ಇರಲಿ ಅಥವಾ ಪ್ಲಾಜ್ಮಾ ಕಟಿಂಗ್ ಇರಲಿ, ಯಾವುದೇ ಭಾಗವನ್ನು ಕತ್ತರಿಸಿದ ನಂತರ ಆ ಜಾಗದಲ್ಲಿ ಒಂದು ‘ಹೀಟ್ ಎಫೆಕ್ಟೆಡ್ ಝೋನ್’ ತಯಾರಾಗುತ್ತದೆ. ಇದರಿಂದ ನಂತರ ಮಾಡಲಾಗುವ ಫಾರ್ಮಿಂಗ್ ನಲ್ಲಿ ಯಾವುದೇ ಕ್ಷಣದಲ್ಲಿ ಸಮಸ್ಯೆಗಳು ಉಂಟಾಗುವ ಸಾಧ್ಯತೆ ಇರುತ್ತದೆ. ಇದೇ ಕಾರಣದಿಂದಾಗಿ ಲೋಹಗಳು ಸ್ವಲ್ಪ ಪ್ರಮಾಣದಲ್ಲಿ ಕಠಿಣವಾಗುವ ಸಾಧ್ಯತೆ ಇರುತ್ತದೆ. ಆದರೆ ಲೇಸರ್ ಪ್ರಕ್ರಿಯೆಯಿಂದಾಗಿ ಅದರಲ್ಲಿ ಉಂಟಾದ ‘ಹೀಟ್ ಎಫೆಕ್ಟೆಡ್ ಝೋನ್’ ತುಂಬಾ ಕಡಿಮೆಯಾಗಿ (ಮಿನಿಮಲ್) ಮಟೀರಿಯಲ್ ನ ಗುಣಧರ್ಮದಲ್ಲಿ (ಪ್ರಾಪರ್ಟಿ) ಯಾವುದೇ ರೀತಿಯ ಬದಲಾವಣೆಯಾಗುವುದಿಲ್ಲ. ಸಾಮಾನ್ಯವಾಗಿ 4-5 ಮಿ.ಮೀ. ದಪ್ಪದ ಶೀಟ್ ಇದ್ದಲ್ಲಿ, ಲೇಸರ್ ನಿಂದ ಕತ್ತರಿಸಿದ ನಂತರ ಲಭಿಸುವ ಹೀಟ್ ಎಫೆಕ್ಟೆಡ್ ಝೋನ್ 0.25 ಮಿ.ಮೀ. ಇರುತ್ತದೆ. ಪ್ಲಾಸ್ಮಾ ಕಟಿಂಗ್ ನಿಂದ ಈ ಕೆಲಸವನ್ನು ಮಾಡಿದಲ್ಲಿ ಇದೇ ಝೋನ್ 5 ರಿಂದ 7 ಮಿ.ಮೀ., ಗ್ಯಾಸ್ ಕಟಿಂಗ್ ನಿಂದ ಮಾಡಿದಲ್ಲಿ ಅದು 10 ರಿಂದ 15 ಮಿ.ಮೀ. ಅಗಲ ಇರುತ್ತದೆ. ಲೇಸರ್ ಪ್ರಕ್ರಿಯೆಯು ತಂಪಾಗಿರುವ ತುಂಡಿನಷ್ಟೇ ಉಚ್ಚಮಟ್ಟದ್ದಾಗಿರುತ್ತದೆ. ಲೇಸರ್ ಪ್ರಕ್ರಿಯೆಯಲ್ಲಿ ಬರ್ ತಯಾರಾಗುವುದಿಲ್ಲ. ಬ್ಲ್ಯಾಂಕಿಂಗ್ ಡೈ ಬಳಸಿ ತಯಾರಾಗಿರುವ ಭಾಗಗಳ ನಿಖರತೆ ಮತ್ತು ಲೇಸರ್ ನಿಂದ ಸಿಗುವ ನಿಖರತೆ ಸಮಾನವಾಗಿಯೇ ಇರುತ್ತದೆ. ಲೇಸರ್ ಮೂಲಕ 1 ಮೀಟರ್ ನಲ್ಲಿ ±0.25 ಮಿ.ಮೀ. ನಷ್ಟು ನಿಖರತೆಯು ಲಭಿಸುತ್ತದೆ. ಗ್ಯಾಸ್ ಕಟಿಂಗ್ ಅಥವಾ ಪ್ಲಾಜ್ಮಾ ಕಟಿಂಗ್ ಮಾಡಿದಲ್ಲಿ 1 ಮೀಟರ್ ನಲ್ಲಿ ± 2 ಮಿ.ಮೀ. ನಷ್ಟು ನಿಖರತೆಯು ಸಿಗುತ್ತದೆ. ಲೇಸರ್ ಬೀಮ್ ಅದರ ನಿಗದಿತ ದಾರಿಯನ್ನು ಬಿಟ್ಟು ಬೇರೆ ಕಡೆಗೆ ಹೋಗುವುದಿಲ್ಲ. ಇದರಿಂದಾಗಿ ಯಂತ್ರಭಾಗಗಳ ಅಳತೆಯಲ್ಲಿ ನಿರಂತರತೆಯನ್ನು ಕಾಪಾಡಲಾಗುತ್ತದೆ. ಪ್ಲಾಜ್ಮಾ ಕಟಿಂಗ್ ನಲ್ಲಿ ಮಟೀರಿಯಲ್ ಹೆಚ್ಚು ಪ್ರಮಾಣದಲ್ಲಿ ಸುಡುತ್ತದೆ. ಇದರಿಂದಾಗಿ ಲೇಸರ್ ಹೋಲಿಸಿದಲ್ಲಿ ಅದರ ನಿಖರತೆಯು ತುಂಬಾ ಕಡಿಮೆ ಇರುತ್ತದೆ. ಪ್ಲಾಜ್ಮಾ ಕಟಿಂಗ್ ನಲ್ಲಿ ಮಟೀರಿಯಲ್ ಕತ್ತರಿಸುವಾಗ ಅದರ ಎಡ್ಜ್ ನಲ್ಲಿ ಟೇಪರ್ ಉಂಟಾಗುತ್ತದೆ. ಟೇಪರ್ ನ ಪ್ರಮಾಣವು ಲೇಸರ್ ಗಿಂತ ಕಡಿಮೆ ಇರುತ್ತದೆ. 15 ಮಿ.ಮೀ. ದಪ್ಪದ ಮಟೀರಿಯಲ್ ಲೇಸರ್ ನಿಂದ ಕತ್ತರಿಸಿದಲ್ಲಿ ಟೇಪರ್ 1 ಮಿ.ಮೀ.ನಷ್ಟು ಇರುತ್ತದೆ. ಅದನ್ನೇ ಪ್ಲಾಜ್ಮಾ ಮೂಲಕ ಕತ್ತರಿಸಿದಲ್ಲಿ ಸಾಮಾನ್ಯವಾಗಿ 4 ಮಿ.ಮೀ. ತನಕ ಟೇಪರ್ ಲಭಿಸಬಲ್ಲದು. ಹಲವಾರು ಯಂತ್ರಭಾಗಗಳ ಟಾಲರನ್ಸ್, ಗ್ಯಾಸ್ ಮತ್ತು ಪ್ಲಾಜ್ಮಾ ಕಟಿಂಗ್ ಮಾಡುವುದರಿಂದ ಪಡೆಯುವುದು ಅಸಾಧ್ಯ, ಅದ್ದರಿಂದ ಅದನ್ನು ಲೇಸರ್ ನಿಂದಲೇ ಮಾಡಬೇಕಾಗುತ್ತದೆ.
ಲೇಸರ್ ಎರಡು ವಿಧದಲ್ಲಿರುತ್ತದೆ. ಮೊದಲಾಗಿ CO2 ಲೇಸರ್. ಇದು ಗ್ಯಾಸ್ ನಿಂದ ತಯಾರಿಸಲಾಗಿರುತ್ತದೆ. ಎರಡನೆಯದಾಗಿ ಫೈಬರ್ ಲೇಸರ್. ಇದು ಸಾಲಿಡ್ ಮಟೀರಿಯಲ್ ನಿಂದ ತಯಾರಿಸಲಾಗುತ್ತದೆ. CO2 ಲೇಸರ್ ಹೋಲಿಸಿದಲ್ಲಿ ಫೈಬರ್ ಲೇಸರ್ ಮಶಿನ್ ತುಂಬಾ ಅಚ್ಟುಕಟ್ಟಾಗಿರುತ್ತದೆ. (ಚಿತ್ರ ಕ್ರ. 2).
ಮಟೀರಿಯಲ್
ಲೇಸರ್ ಕಟಿಂಗ್ ಗೋಸ್ಕರ ಬಳಸಲಾಗುವ ಮಟೀರಿಯಲ್ ವಿಶಿಷ್ಟ ಗುಣಮಟ್ಟದ್ದಾಗಿರಬೇಕು. ಪ್ರಮುಖ ಆವಶ್ಯಕತೆ ಅಂದರೆ ಅದರಲ್ಲಿ ಸೂಕ್ತ ರೀತಿಯ ಹೀಟ್ ಟ್ರೀಟ್ ಮೆಂಟ್ ಮಾಡಿ ಅದರಲ್ಲಿರುವ ಸ್ಟ್ರೆಸ್ ಸಂಪೂರ್ಣವಾಗಿ ತೆಗೆದಿರಬೇಕು. ಇಲ್ಲದಿದ್ದಲ್ಲಿ ಮಟೀರಿಯಲ್ ಕತ್ತರಿಸಿದ ನಂತರ ಅದರಲ್ಲಿರುವ ಸ್ಟ್ರೆಸ್ ಇಲ್ಲದಂತಾಗಿ ಅಲ್ಲಿ ಡಿಸ್ಟಾರ್ಶನ್ ಉಂಟಾಗುವ ಸಾಧ್ಯತೆ ಇರುತ್ತದೆ. ಕಡಿಮೆ ದಪ್ಪದ ಅಥವಾ ತೆಳ್ಳಗಿನ (ಥಿನ್) ಮಟೀರಿಯಲ್ ನಲ್ಲಿ ಈ ರೀತಿಯ ಡಿಸ್ಟಾರ್ಶನ್ ಆಗುವ ಸಾಧ್ಯತೆ ಹೆಚ್ಚಿರುತ್ತದೆ. ಎಲ್ಲ ರೀತಿಯ ಮಟೀರಿಯಲ್ ಗಳಲ್ಲಿ ಇದೇ ರೀತಿಯ ಸಮಸ್ಯೆಯು ಉಂಟಾಗುತ್ತಿತ್ತು. ಸಾಮಾನ್ಯವಾಗಿ ಕೋಲ್ಡ್ ರೋಲ್ಡ್ (CR) ಮಟೀರಿಯಲ್ ನ ಟ್ರೀಟ್ ಮೆಂಟ್ ಉಚ್ಚಮಟ್ಟದ್ದಾಗಿದ್ದರಿಂದ ಸಮಸ್ಯೆಗಳು ಉದ್ಭವಿಸುವುದಿಲ್ಲ. ಹಾಟ್ ರೋಲ್ಡ್ (HR) ಮಟೀರಿಯಲ್ ನಲ್ಲಿ ಇಂತಹ ಸಮಸ್ಯೆಗಳು ಕಂಡುಬರುತ್ತವೆ. 5-12 ಮಿ.ಮೀ. ದಪ್ಪದ ಮಟೀರಿಯಲ್ ನಲ್ಲಿ ಹೆಚ್ಚು ಸಮಸ್ಯೆಗಳು ಉಂಟಾಗುತ್ತವೆ. ಸ್ಟೇನ್ ಲೆಸ್ ಸ್ಟೀಲ್ ನಲ್ಲಿ ಕಡಿಮೆ ಪ್ರಮಾಣದ ಸಮಸ್ಯೆಗಳು ಉದ್ಭವಿಸುತ್ತವೆ. ಕಾರಣ ಸ್ಟೇನ್ ಲೆಸ್ ಸ್ಟೀಲ್ ತಯಾರಿಸುವ ಪ್ರಕ್ರಿಯೆಯು ಉಚ್ಚಮಟ್ಟದ್ದಾಗಿರುತ್ತದೆ. ವಾಹನಗಳ ಉತ್ಪಾದನೆಯಲ್ಲಿ ಹೆಚ್ಚಿನ ಯಂತ್ರಭಾಗಗಳು ಅಥವಾ ಬಾಡಿ 0.8, 1, 1.2 ಮಿ.ಮೀ. ದಪ್ಪದ್ದಾಗಿರುತ್ತವೆ. ಇದರಲ್ಲಿ ಇಂತಹ ಸಮಸ್ಯೆಗಳು ಕಂಡುಬರುವುದಿಲ್ಲ. ಇದಕ್ಕಿಂತ ಹೆಚ್ಚು ದಪ್ಪದ ಮಟೀರಿಯಲ್ ಇದ್ದಲ್ಲಿ ಅನೇಕ ಸಮಸ್ಯೆಗಳು ಉಂಟಾಗುತ್ತವೆ.
ಪ್ರಾರಂಭದಲ್ಲಿ ಈ ರೀತಿಯ ಸಮಸ್ಯೆಗಳು ಉದ್ಭವಿಸಿದ ನಂತರ ನಾವು ಜರ್ಮನಿಯಲ್ಲಿರುವ ಒಂದು ಕಂಪನಿಯೊಂದಿಗೆ ವಿಚಾರಿಸಿದೆವು. ಆದರೆ ಅವರು ಇಂತಹ ಡಿಸ್ಟಾರ್ಶನ್ ನ ಸಮಸ್ಯೆಯು ಇಲ್ಲ ಎಂಬುದಾಗಿ ತಿಳಿಸಿದರು. ಅವರಲ್ಲಿರುವ ಮಟೀರಿಯಲ್ ಉಚ್ಚ ಗುಣಮಟ್ಟದ ಹೀಟ್ ಟ್ರೀಟ್ ಮೆಂಟ್ ಮಾಡಿ ಸ್ಟ್ರೆಸ್ ರಹಿತವಾಗಿ ತಯಾರಿಸಲಾಗಿದೆ, ಎಂಬ ಅಂಶವು ನಮ್ಮ ಗಮನಕ್ಕೆ ಬಂತು. ಈ ಕುರಿತು ಜಿಂದಾಲ್ ಅಥವಾ ಇನ್ನಿತರ ಸ್ಟೀಲ್ ಉತ್ಪಾದನೆಯನ್ನು ಮಾಡುವ ಆಂತಾರಾಷ್ಟ್ರೀಯ ಕಂಪನಿಗಳೊಂದಿಗೆ ನಾವು ಚರ್ಚಿಸಿದೆವು. ತಾವು ನಮಗೆ ಲೇಸರೇಬಲ್ ಮಟೀರಿಯಲ್ ಪೂರೈಸ ಬಲ್ಲಿರೇ, ಎಂಬುದಾಗಿ ಅವರಲ್ಲಿ ವಿಚಾರಿಸಿದೆವು. ಕಾರಣ ಯುರೋಪ್ ದೇಶಗಳಲ್ಲಿ ಈ ರೀತಿಯ ಮಟೀರಿಯಲ್ ಬಳಸಲಾಗುತ್ತದೆ. ಸ್ವಲ್ಪ ಸಮಯದ ಪ್ರಯತ್ನದ ನಂತರ ಭಾರತದಲ್ಲಿರುವ ಸ್ಟೀಲ್ ಉತ್ಪಾದಕರು ಆವಶ್ಯಕವಿರುವ ಎಲ್ಲ ಪ್ರಕ್ರಿಯೆಗಳನ್ನು ಅಭಿವೃದ್ಧಿ ಪಡಿಸಿ ಲೇಸರೇಬಲ್ ಮಟೀರಿಯಲ್ ನ ಸರಬರಾಜನ್ನು ಪ್ರಾರಂಭಿಸಿದರು.
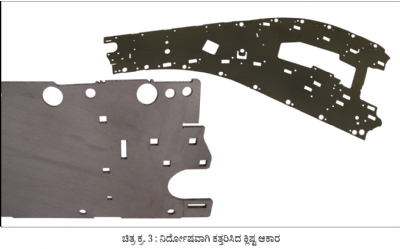
ನಾವು ಸ್ಟೀಲ್ ಕಟಿಂಗ್ ಗರಿಷ್ಠ ಪ್ರಮಾಣದಲ್ಲಿ ಮಾಡುತ್ತೇವೆ. ಬ್ರಾಸ್, ಸ್ಟೇನ್ ಲೆಸ್ ಸ್ಟೀಲ್ ಇವುಗಳಿಗೋಸ್ಕರ ಲೇಸರ್ ಬಳಸುತ್ತೇವೆ. ಕಾಪರ್ ಮತ್ತು ಅಲ್ಯುಮಿನಿಯಮ್ ಕೂಡಾ ಲೇಸರ್ ನಿಂದ ಕತ್ತರಿಸಬಹುದಾಗಿದೆ. ಆದರೆ ಅಲ್ಯುಮಿನಿಯಮ್ ಲೇಸರ್ ನಿಂದ ಕತ್ತರಿಸುವುದು ತುಂಬಾ ಕಷ್ಟಕರವಾಗಿದೆ. ಇದಕ್ಕೆ ಎರಡು ಕಾರಣಗಳಿವೆ. ಮೊದಲನೆಯದಾಗಿ ಮಟೀರಿಯಲ್ ನ ರಿಫ್ಲೆಕ್ಟಿವಿಟಿ. ಲೇಸರ್, ಬೆಳಕಿನ ಕಿರಣಗಳ ಬೀಮ್ ಇರುವುದರಿಂದ ಅದು ರಿಫ್ಲೆಕ್ಟ್ ಆಗುತ್ತದೆ. ಎರಡನೆಯದಾಗಿ ಕಾಪರ್ ಮತ್ತು ಅಲ್ಯುಮಿನಿಯಮ್ ನಲ್ಲಿ ಉಷ್ಣತೆಯ ಪ್ರವಾಹವು ತುಂಬಾ ವೇಗವಾಗಿ ಆಗುತ್ತದೆ. ಇದರಿಂದಾಗಿ ಇಂತಹ ಲೋಹಗಳನ್ನು ಕತ್ತರಿಸುವಾಗ ಹೆಚ್ಚು ಉಷ್ಣತೆಯು ಬೇಕಾಗುತ್ತದೆ. ಯಾವ ಲೇಸರ್ ಪವರ್ ನಿಂದ 20 ಮಿ.ಮೀ. ಸ್ಟೆನ್ ಲೆಸ್ ಸ್ಟೀಲ್ ಕತ್ತರಿಸಬಹುದೋ, ಅದರಿಂದ ಕೇವಲ 5 ಮಿ.ಮೀ. ಅಲ್ಯುಮಿನಿಯಮ್ ಕತ್ತರಿಸುವುದು ಸಾಧ್ಯ. ನಾನ್ ಮೆಟಲ್ ಲೇಸರ್ ನಿಂದ ಕತ್ತರಿಸುವುದೂ ಸಾಧ್ಯ. ಆದರೆ ನಾನ್ ಮೆಟಲ್ ತುಂಡು ಮಾಡುವಾಗ ಟಾಕ್ಸಿಕ್ ಫ್ಯೂಮ್ ತಯಾರಾಗುವ ಸಮಸ್ಯೆಯು ಇದರಲ್ಲಿದೆ. ಈ ಪರಿಸ್ಥಿಯನ್ನು ಎದುರಿಸಲು ಉಚ್ಚಮಟ್ಟದ ಎಕ್ಸಾಸ್ಟ್ ಯಂತ್ರಣೆಯು ಇರುವುದು ಅತ್ಯಾವಶ್ಯಕವಾಗಿದ್ದು ಅದನ್ನು ಬೃಹತ್ ಪ್ರಮಾಣದಲ್ಲಿ ಬಳಸಬೇಕಾಗುತ್ತದೆ.
ಮಶಿನ್ ನ ಸಾಮರ್ಥ್ಯ
ನಾವು 1994 ರಲ್ಲಿ ಮೊದಲ ಮಶಿನ್ ತಂದಾಗ ಆ ಮಶಿನ್ ನಿಂದ ನಾವು 10 ಮಿ.ಮೀ. ತನಕದ ಲೋಹಗಳನ್ನು ಕತ್ತರಿಸುತ್ತಿದ್ದೆವು. ಇಂದು ನಮ್ಮಲ್ಲಿರುವ ಮಶಿನ್ ಗಳಲ್ಲಿ 25 ಮಿ.ಮೀ.ನಷ್ಟು ದಪ್ಪದ ಲೋಹಗಳನ್ನೂ ಕತ್ತರಿಸಬಲ್ಲೆವು.
ಮಶಿನ್ ಗಳ ಸಾಮರ್ಥ್ಯಕ್ಕೆ ಅನುಸಾರವಾಗಿ ಅದರಲ್ಲಿ 8 ಮಿ.ಮೀ. ನಿಂದ 20 ಮಿ.ಮೀ. ದಪ್ಪದ ಮಟೀರಿಯಲ್ ಕತ್ತರಿಸುವುದು ಸಾಧ್ಯ. ಆದರೆ ಅದರ ನಿಖರತೆಯು ಮಶಿನ್ ಉತ್ಪಾದಕರು ನೀಡಿರುವ ಮಿತಿಗಳಿಗೆ ಅನುಸಾರವಾಗಿ ಲಭಿಸುತ್ತದೆ. ಇತ್ತೀಚೆಗೆ ಲಭ್ಯವಿರುವ ಮಶಿನ್ 1 ಮೀ. X 1 ಮೀ. ನಿಂದ 2.5 ಮೀ. X 16 ಮೀ. ತನಕ ಯಾವುದೇ ಆಕಾರದ ಬೆಡ್ ಇರುತ್ತದೆ. ಹಾಗೆಯೇ ಲೇಸರ್ ನ ಪವರ್ ಈ ಪ್ಯಾರಾಮೀಟರ್ ಮಹತ್ವದ್ದಾಗಿದೆ. ಇಂಡಸ್ಟ್ರಿಗಳಲ್ಲಿ ಸಾಮಾನ್ಯವಾಗಿ 1 kW ನಿಂದ 12 kW ನಷ್ಟು ಶಕ್ತಿ ಇರುವ ಮಶಿನ್ ಗಳನ್ನು ಬಳಸಲಾಗುತ್ತದೆ. 1 kW ನ ಮಶಿನ್, 5 ಮಿ.ಮೀ. ತನಕದ ಮಟೀರಿಯಲ್ ಕತ್ತರಿಸಬಲ್ಲದು, ಹಾಗೆಯೇ 12 kW ನ ಮಶಿನ್ 35 ರಿಂದ 40 ಮಿ.ಮೀ. ತನಕದ ಮಟೀರಿಯಲ್ ಕತ್ತರಿಸಬಲ್ಲದು. ಸಾಮಾನ್ಯವಾಗಿ 1 ಮೀ. X 1 ಮೀ. ಮಶಿನ್ ಹೆಚ್ಚು ನಿಖರವಾಗಿರುತ್ತದೆ. ಮಶಿನ್ ದೊಡ್ಡದಾದಷ್ಟು ಅದರ ನಿಖರತೆ ಕಡಿಮೆಯಾಗುತ್ತದೆ.
ಲೇಸರ್ ಪ್ರಕ್ರಿಯೆಯಲ್ಲಿ ನಾಲ್ಕು ಅಂಶಗಳಿರುತ್ತವೆ. ಮೊದಲನೆಯದಾಗಿ ಅಳತೆಯ ನಿಖರತೆ, ಎರಡನೆಯದಾಗಿ ತುಂಡುಗಳ ಫಿನಿಶ್, ಮೂರನೆಯದು ಟೇಪರ್ ಮತ್ತು ನಾಲ್ಕನೆಯದು ಡಿಸ್ಟಾರ್ಶನ್. ಲೇಸರ್ ಪ್ರಕ್ರಿಯೆಯಲ್ಲಿ ಹೀಟ್ ಅಫೆಕ್ಟೆಡ್ ಝೋನ್ ಕಡಿಮೆ ಇರುವುದರಿಂದ ಮಟೀರಿಯಲ್ ಡಿಸ್ಟಾರ್ಶನ್ ತುಂಬಾ ಕಡಿಮೆಯಾಗುತ್ತದೆ. ಲೇಸರ್ ಪ್ರಕ್ರಿಯೆಯಲ್ಲಿ ಸಾಮಾನ್ಯವಾಗಿ ಟೇಪರ್ ಉಂಟಾಗುವುದಿಲ್ಲ. ಆದರೆ ಮಟೀರಿಯಲ್ ಹೆಚ್ಚು ದಪ್ಪದ್ದು ಇದ್ದಲ್ಲಿ ಅದಕ್ಕೆ ಸ್ವಲ್ಪ ಪ್ರಮಾಣದಲ್ಲಿ ಟೇಪರ್ ಉಂಟಾಗುತ್ತದೆ. ತುಂಬಾ ಸೂಕ್ಷ್ಮ ಬೀಮ್ ಬಳಸಿ ಮಟೀರಿಯಲ್ ಕತ್ತರಿಸಲಾಗುತ್ತದೆ, ಆದ್ದರಿಂದ ನಿಖರತೆ ಮತ್ತು ಫಿನಿಶ್ ಹೆಚ್ಚು ಉಚ್ಚಮಟ್ಟದಲ್ಲಿ ಲಭಿಸುತ್ತದೆ.
ಅನೇಕ ರೀತಿಯ ಉಪಯೋಗ
ಲೇಸರ್ ತಂತ್ರಜ್ಞಾನವನ್ನು ಪ್ರಮುಖವಾಗಿ ಪ್ರೊಟೊಟೈಪಿಂಗ್ ಗೋಸ್ಕರ ತಯಾರಿಸಲಾಗಿತ್ತು. ಅನೇಕ ಕ್ಷೇತ್ರಗಳಲ್ಲಿ ವಿವಿಧ ಅಪ್ಲಿಕೇಶನ್ ಗಳಿಗೆ ಅನುಸಾರವಾಗಿ (ಚಿತ್ರ ಕ್ರ. 3, 4 ಮತ್ತು 5) ಅದನ್ನು ಅವಲಂಬಿಸಲಾಯಿತು. ನಮ್ಮಲ್ಲಿರುವ ಉದ್ಯಮಗಳು ಹೆಚ್ಚಾಗಿ ಕಸ್ಟಮೈಜೆಶನ್ ಕಡೆಗೆ ಗಮನ ಹರಿಸಿದ್ದಾರೆ. ಕಡಿಮೆ ಬೆಂಚ್ ಸೈಜ್ ಕ್ವಾಂಟಿಟಿಯ ಉತ್ಪಾದನೆಯ ಕಡೆಗೆ ನಮ್ಮ ಉದ್ಯಮಗಳು ಸಾಗುತ್ತಿವೆ. ಪ್ರೆಸಿಂಗ್ ಕೆಲಸದಲ್ಲಿ ಕಸ್ಟಮೈಜೆಶನ್ ಆಗದಿರುವುದರಿಂದ ಲೇಸರ್ ಬಳಸುವ ಒಲವು ಹೆಚ್ಚುತ್ತಿದೆ. ಕಾರಣ ಪ್ರತಿಯೊಂದು ಲಾಟ್ ಬೇರೆಬೇರೆಯೇ ಇರಬೇಕು. ಅದಕ್ಕೋಸ್ಕರ ಮಶಿನ್ ಫ್ಲೆಕ್ಸಿಬಲ್ ಇರುವುದೂ ಅತ್ಯಾವಶ್ಯಕವಾಗಿದೆ. ಇದರಲ್ಲಿ ಕೈಗಾರಿಕೋದ್ಯಮಿಗಳಿಗೆ ಅನೇಕ ವಿಧದ ಪ್ರಯೋಗಗಳನ್ನು ಮಾಡುವುದು ಸಾಧ್ಯವಾಗಿದೆ. ಕೇವಲ ಯಂತ್ರಭಾಗಗಳ ಡಿಸೈನ್ ಸೂಕ್ತ ರೀತಿಯಲ್ಲಿ ನೀಡುವುದನ್ನು ಅಪೇಕ್ಷಿಸಲಾಗಿದೆ. ವಾಹನೋದ್ಯೋಗದ ಹೊರತಾಗಿ ಇನ್ನಿತರ ಯಾವುದೇ ರೀತಿಯ ಉದ್ಯಮಗಳಲ್ಲಿ ಶೀಟ್ ಮೆಟಲ್ ನ ಆವಶ್ಯಕತೆ ಇರುವಾಗ ಅದಕ್ಕೆ ಸಂಬಂಧಿಸಿರುವ ಕೆಲಸವನ್ನು ಲೇಸರ್ ಕಟಿಂಗ್ ನಿಂದಲೇ ಮಾಡಲಾಗುತ್ತದೆ.
ಅನೇಕ ಕೈಗಾರಿಕೋದ್ಯಮಿಗಳು ಪ್ಲಾಜ್ಮಾ ಕಟಿಂಗ್ ಅಥವಾ ಗ್ಯಾಸ್ ಕಟಿಂಗ್ ನಿಂದ ಅಪ್ ಗ್ರೇಡ್ ಆಗಿದ್ದು, ಈಗ ಅವರು ಲೇಸರ್ ಕಟಿಂಗ್ ತಂತ್ರಜ್ಞಾನದೆಡೆಗೆ ತಲುಪಿದ್ದಾರೆ. ಲೇಸರ್ ಪ್ರಕ್ರಿಯೆಯ ಖರ್ಚು ಕಾಲಕ್ಕೆ ತಕ್ಕಂತೆ ತುಂಬಾ ಕಡಿಮೆ ಇರುವುದೇ, ಇದರ ಕಾರಣವಾಗಿದೆ. ಗ್ಯಾಸ್ ಕಟಿಂಗ್ ಗಿಂತ ಇದು ತುಂಬಾ ಪಟ್ಟು ದುಬಾರಿಯಾಗಿದೆ. ತಂತ್ರಜ್ಞಾನದಲ್ಲಿ ಅಭಿವೃದ್ಧಿಯಾದಂತೆ ಎಲ್ಲದರ ಬೆಲೆಯೂ ಕಡಿಮೆಯಾಯಿತು.
ಪ್ರೊಟೊಟೈಪಿಂಗ್ ಮತ್ತು ಸ್ಮಾಲ್ ಬ್ಯಾಚ್ ಕ್ವಾಂಟಿಟಿಗೆ ಲೇಸರ್ ತಂತ್ರಜ್ಞಾನದ ಪ್ರಾರಂಭವಾಯಿತು. ಆದರೆ ಕಾಲಾನುಕ್ರಮವಾಗಿ ಲೇಸರ್ ತಂತ್ರಜ್ಞಾನದಲ್ಲಿ ಬದಲಾವಣೆಗಳಾದವು ಮತ್ತು ಇಂದು ಲೇಸರ್ ಇದು ಪ್ರೊಡಕ್ಷನ್ ಟೂಲ್ ಎಂಬುದಾಗಿ ಪ್ರಚಲಿತವಾಗಿದೆ.
ಗ್ಯಾಸ್ ಕಟ್ ಇದು ತುಂಬಾ ಸಮಯವನ್ನು ವ್ಯಯಿಸುವ ಪ್ರಕ್ರಿಯೆಯಾಗಿದೆ, ಎಂಬುದು ನಮ್ಮ ಗಮನಕ್ಕೆ ಬಂತು. ಕಾರಣ ಪ್ರತ್ಯಕ್ಷ ಕಟಿಂಗ್ ಮಾಡಿದ ನಂತರ ಫಿನಿಶಿಂಗ್ ಗೋಸ್ಕರ ಅದರಲ್ಲಿ ಅನೇಕ ವಿಧದ ಪ್ರಕ್ರಿಯೆಗಳನ್ನು ಮಾಡಬೇಕಾಗುತ್ತದೆ. ಆದರೆ ಲೇಸರ್ ಪ್ರಕ್ರಿಯೆಯ ನಂತರ ಅದರಲ್ಲಿ ಯಾವುದೇ ಪ್ರಕ್ರಿಯೆಯನ್ನು ಮಾಡಲಾಗುವುದಿಲ್ಲ. ಇದೇ ಲೇಸರ್ ಪ್ರಕ್ರಿಯೆಯಿಂದ ಆಗುವ ಲಾಭ. ಅದರಲ್ಲಿ ನಂತರ ಡಿಬರಿಂಗ್ ಮಾಡುವ ಆವಶ್ಯಕತೆ ಇರುವುದಿಲ್ಲ. ಚಿತ್ರ ಕ್ರ. 5 ರಲ್ಲಿ ತೋರಿಸಿರುವ ಭಾಗಗಳನ್ನು ಕತ್ತರಿಸಲು ಲೇಸರ್ ಬಳಸಿದ್ದರಿಂದ ಅದಕ್ಕೆ ಬೇಕಾಗುವ ಸಮಯ ಮತ್ತು ಖರ್ಚು ಕೂಡಾ ಕಡಿಮೆಯಾಗುತ್ತದೆ.
ಉದಾಹರಣೆ
ನಮ್ಮಲ್ಲಿ ಸ್ಲೈಡರ್ (ಚಿತ್ರ ಕ್ರ. 6) ಎಂಬ ಒಂದು ಯಂತ್ರಭಾಗವನ್ನು ತಯಾರಿಸುತ್ತೇವೆ. ಅದರ ಉತ್ಪಾದನೆಯ ಖರ್ಚು ಕಡಿಮೆಯಾಗಬೇಕು, ಎಂಬ ಬೇಡಿಕೆಯು ಗ್ರಾಹಕರಿಂದ ಬಂದಿತ್ತು. ಇದಕ್ಕೋಸ್ಕರ ಗ್ರಾಹಕರು ಪ್ರಾರಂಭದಿಂದಲೂ ಅಂದರೆ ಡಿಸೈನ್ ಮಾಡುವಾಗಿನಿಂದಲೂ ನಮ್ಮೊಂದಿಗೆ ಚರ್ಚೆಯನ್ನು ಮಾಡುತ್ತಿದ್ದರು. ಈ ಸ್ಲೈಡರ್ ನ ಅಸೆಂಬ್ಲಿ ತುಂಬಾ ಕ್ಲಿಷ್ಟವಾಗಿದ್ದು ಈ ಹಿಂದೆ ಅದರ ಕ್ಯಾಲಿಬ್ರೇಶನ್ ಆದರ ನಂತರ ಅನೇಕ ರೀತಿಯ ಯಂತ್ರಣೆಯನ್ನು ಮಾಡಲಾಗುತ್ತಿತ್ತು. ಇದೇ ಹೆಚ್ಚು ಖರ್ಚಾಗುವುದಕ್ಕೆ ಕಾರಣವಾಗಿತ್ತು. ಈ ಖರ್ಚನ್ನು ಕಡಿಮೆ ಮಾಡುವುದು ಸಾಧ್ಯ ಅಥವಾ ಫ್ಯಾಬ್ರಿಕೇಶನ್ ನ ನಂತರ ಯಂತ್ರಣೆಯನ್ನು ಮಾಡಲಾಗುತ್ತದೆ, ಇದನ್ನು ತಡೆಯಬಹುದೇ, ಎಂಬ ಅಂಶವು ದೀರ್ಘ ಚರ್ಚೆಯ ನಂತರ ನಮ್ಮ ಗಮನಕ್ಕೆ ಬಂತು. ಇದರಲ್ಲಿ ಡಿಸ್ಟಾರ್ಶನ್ ಈ ಸಮಸ್ಯೆಯು ಬಹು ದೊಡ್ಡದಾಗಿತ್ತು. ಮಟೀರಿಯಲ್ ಕತ್ತರಿಸುವುದು, ಮಟೀರಿಯಲ್ ಬಗ್ಗಿಸುವುದು ಮತ್ತು ನಂತರ ಅದೇ ಮಟೀರಿಯಲ್ ವೆಲ್ಡ್ ಮಾಡುವುದು ಈ ರೀತಿಯಲ್ಲಿ ಪ್ರತಿಯೊಂದು ಹಂತದಲ್ಲಿ ಡಿಸ್ಟಾರ್ಶನ್ ಉಂಟಾಗುತ್ತದೆ. ಈ ರೀತಿಯ ಡಿಸ್ಟಾರ್ಶನ್ ಕಡಿಮೆ ಮಾಡುವುದು ಒಂದು ಸವಾಲಾಗಿರುತ್ತದೆ. ಇದಕ್ಕೋಸ್ಕರ ಎಲ್ಲಕ್ಕಿಂತಲೂ ಮೊದಲಾಗಿ ಮಟೀರಿಯಲ್ ಉಚ್ಚಮಟ್ಟದ್ದಾಗಿರಬೇಕು. ಮಟೀರಿಯಲ್ ನ ಸಮತಟ್ಟುತನವು ಯೋಗ್ಯವಾಗಿರಬೇಕು. ಈ ಹಿಂದೆ ಗ್ಯಾಸ್ ಕಟಿಂಗ್ ಅಥವಾ ಪ್ಲಾಜ್ಮಾ ಕಟಿಂಗ್ ಮಾಡಿ ಮಟೀರಿಯಲ್ ಕತ್ತರಿಸಲಾಗುತ್ತಿತ್ತು. ಅದರ ಬದಲಾಗಿ ನಾವು ಲೇಸರ್ ಪ್ರಕ್ರಿಯೆಯನ್ನು ಮಾಡಲಾರಂಭಿಸಿದೆವು. ಇದರಿಂದಾಗಿ ಕನಿಷ್ಠ ಪ್ರಮಾಣದಲ್ಲಿ ಹೀಟ್ ಎಫೆಕ್ಟೆಡ್ ಝೋನ್ ಉಂಟಾಗುತ್ತದೆ ಮತ್ತು ಡಿಸ್ಟಾರ್ಶನ್ ಕೂಡಾ ತುಂಬಾ ಕಡಿಮೆಯಾಗುತ್ತದೆ.
ಈ ಯಂತ್ರಭಾಗಗಳ ಅಗಲ ಕಡಿಮೆ ಮತ್ತು ಉದ್ದ ಹೆಚ್ಚು ಇರುತ್ತದೆ. ಯಂತ್ರಭಾಗಗಳ ಉದ್ದ ಹೆಚ್ಚು ಮತ್ತು ಕಡಿಮೆ ಅಗಲ ಇದ್ದಲ್ಲಿ ಡಿಸ್ಟಾರ್ಶನ್ ಉಂಟಾಗುವ ಸಾಧ್ಯತೆ ಹೆಚ್ಚು ಇರುತ್ತದೆ. ಇದರಿಂದಾಗಿ ಲೇಸರ್ ನಿಂದ ಪ್ರಕ್ರಿಯೆ ಮಾಡಿ ಅದರ ಪ್ಯಾರಾಮೀಟರ್ ಕನಿಷ್ಠ ಡಿಸ್ಟಾರ್ಶನ್ ಆಗುವಂತೆ ಅಳವಡಿಸಬೇಕಾಗುತ್ತದೆ. ಅದರ ನಂತರ ಸಿ.ಎನ್.ಸಿ. ಬೆಂಡಿಂಗ್ ಮಶಿನ್ ನಲ್ಲಿ ಬೆಂಡಿಂಗ್ ಪ್ರಕ್ರಿಯೆಯನ್ನು ಮಾಡಲಾಯಿತು. ಇದರಿಂದಾಗಿ ಬೆಂಡಿಂಗ್ ಮಾಡಿದ ನಂತರದ ಅಪೇಕ್ಷಿತ ನಿಖರತೆಯು ಲಭಿಸುತ್ತದೆ. ± 30 ನಿಮಿಷಗಳ ಟಾಲರನ್ಸ್ ನಲ್ಲಿ ಅದರ ಬೆಂಡಿಂಗ್ ಆಗುತ್ತದೆ. ಈ ಯಂತ್ರಭಾಗಗಳಲ್ಲಿ ಅನೇಕ ರಂಧ್ರಗಳಿರುತ್ತವೆ ಮತ್ತು ಅವುಗಳಿಗೆ ಬೇರೆಬೇರೆ ಜಾಗದಲ್ಲಿ ಬುಶ್ ವೆಲ್ಡ್ ಮಾಡಲಾಗಿರುತ್ತದೆ. ಲೇಸರ್ ನಿಂದ ಪ್ರತಿಯೊಂದು ರಂಧ್ರದ ಸೆಂಟರ್ ಡಿಸ್ಟನ್ಸ್ ತುಂಬಾ ನಿರ್ದೋಷವಾಗಿ ನಿಯಂತ್ರಿಸಲಾಯಿತು. ಬುಶ್ ನಲ್ಲಿರುವ ದೂರವು ಫ್ಯಾಬ್ರಿಕೇಶನ್ ನಂತರ 0.5 ಮಿ.ಮೀ. ಮೈಕ್ರಾನ್ ನಲ್ಲಿ ನಿಯಂತ್ರಿಸಲ್ಪಟ್ಟಿತು. ಕನಿಷ್ಠ ಪ್ರಮಾಣದ ಡಿಸ್ಟಾರ್ಶನ್, ನಿಖರವಾದ ಸೆಂಟರ್ ಡಿಸ್ಟನ್ಸ್ ಮತ್ತು ರಂಧ್ರಗಳ ನಿಖರತೆ ಈ ಮೂರೂ ಅಂಶಗಳು ನಿಯಂತ್ರಿಸಲ್ಪಟ್ಟವು. ಈ ಯಂತ್ರಭಾಗಗಳಿಗೋಸ್ಕರ ನಾವು ಕೆಲವು ಫಿಕ್ಸ್ಚರ್ ಗಳನ್ನು (ಚಿತ್ರ ಕ್ರ. 7) ತಯಾರಿಸಿದೆವು. ಇದರಿಂದಾಗಿ ಅದರಲ್ಲಿ ವೆಲ್ಡಿಂಗ್ ಪೊಸಿಶನ್ ಸರಿಯಾಗಿ ಮಾಡುವುದು ಸಾಧ್ಯವಾಯಿತು. ವೆಲ್ಡಿಂಗ್ ಪ್ರಕ್ರಿಯೆಗೋಸ್ಕರ ಫಿಕ್ಸ್ಚರ್ ನಲ್ಲಿ ನಾವು ವೆಲ್ಡಿಂಗ್ ನ ಕ್ರಮವನ್ನು ನಿರ್ಧರಿಸಿದೆವು. ಒಂದು ಭಾಗವನ್ನು ವೆಲ್ಡ್ ಮಾಡಿದ ನಂತರ ಇನ್ನೊಂದು ಭಾಗವನ್ನು ವೆಲ್ಡ್ ಮಾಡುವ ಮುಂಚೆ ಅದು ತಂಪಾಗಲು ಅದಕ್ಕೆ ಆಗಾಗ ನಿರ್ಧಾರಿತ ಸಮಯದ ತನಕ ಕಾಯಬೇಕಾಗುತ್ತದೆ. ಈ ರೀತಿಯಲ್ಲಿ ಸಂಪೂರ್ಣ ಯಂತ್ರಭಾಗವನ್ನು ತಯಾರಿಸುವ ಪ್ರಕ್ರಿಯೆಯನ್ನು ನಿರ್ಧರಿಸಲಾಯಿತು. ನಂತರ ಯಂತ್ರಣೆಯ ಹೊರತಾಗಿಯೂ ಇಂತಹ ಯಂತ್ರಭಾಗಗಳನ್ನು ತಯಾರಿಸುವುದು ಸಾಧ್ಯ, ಎಂಬುದೂ ಸಾಬೀತಾಯಿತು. ಈ ಯಂತ್ರಭಾಗಗಳ ಒಳಗೆ ಎರಡು ಫ್ಲ್ಯಾಟ್ ವೆಲ್ಡ್ ಮಾಡಲಾಗಿರುತ್ತದೆ. ಅದರಲ್ಲಿ ಒಂದು ಮೂರನೇ ಯಂತ್ರಭಾಗವು ಸ್ಲೈಡ್ ಆಗುತ್ತದೆ. ಅದಕ್ಕೋಸ್ಕರ ಅದಕ್ಕೆ ಸ್ಲೈಡರ್ ಅಥವಾ ಕ್ಯಾರಿಯರ್ ಎಂಬ ಹೆಸರನ್ನು ನೀಡಲಾಗಿದೆ. ಪ್ರಕ್ರಿಯೆಯ ಸುಧಾರಣೆಯಿಂದ ಮತ್ತು ಡಿಸೈನ್ ನಲ್ಲಿ ಹಲವಾರು ಬದಲಾವಣೆಗಳನ್ನು ಮಾಡಿದ ನಂತರ ಈ ಎಲ್ಲ ಅಂಶಗಳನ್ನು ಮಾಡಲಾಯಿತು. ಉದಾಹರಣೆ, ಹಲವಾರು ಕಡೆಗಳಲ್ಲಿ ದಪ್ಪವನ್ನು ಹೆಚ್ಚಿಸಬೇಕಾಯಿತು, ಎಲ್ಲಿ ವೆಲ್ಡಿಂಗ್ ಮಾಡಬೇಕು ಮತ್ತು ಬೇಡಾ, ಎಂಬುದರ ಕುರಿತು ಮುಂಜಾಗ್ರತೆಯನ್ನು ವಹಿಸಲಾಯಿತು. ಈ ರೀತಿಯಲ್ಲಿ ಎಲ್ಲ ಸುಧಾರಣೆಗಳನ್ನು ಮಾಡಿ ಯಂತ್ರಭಾಗಗಳಲ್ಲಿ ಸುಮಾರು ಶೇಕಡಾ 20 ರಷ್ಟು ಆರ್ಥಿಕ ಉಳಿತಾಯವೂ ಆಯಿತು. ಈ ಪ್ರಕ್ರಿಯೆಯನ್ನು ನಾವು ಈ ಯಂತ್ರಭಾಗಗಳಲ್ಲಿ ಮುಂಚೆ ಸ್ಥಾಪಿಸಿ ನಂತರ ಇನ್ನಿತರ ಅನೇಕ ರೀತಿಯ ಯಂತ್ರಭಾಗಗಳಿಗೆ ಅದನ್ನು ಬಳಸಲಾರಂಭಿಸಿದೆವು. ಈ ಸಂಪೂರ್ಣ ಪ್ರಕ್ರಿಯೆಯಲ್ಲಿ ಎಲ್ಲಿಯೂ ಹೀಟ್ ಟ್ರೀಟ್ ಮೆಂಟ್ ಅಥವಾ ಸ್ಟ್ರೆಸ್ ರಿಲೀವಿಂಗ್ ನಂತಹ ಪ್ರಕ್ರಿಯೆಗಳನ್ನು ಮಾಡಲಾಗಿಲ್ಲ. ಯಾವುದೇ ಯಂತ್ರಣೆಯನ್ನು ಮಾಡದೇ ಲೇಸರ್ ಪ್ರಕ್ರಿಯೆಯನ್ನು ಮಾಡಿ ಆ ಅಸೆಂಬ್ಲಿಯನ್ನು ನಾವು ತಯಾರಿಸಿದೆವು.
ಸುರಕ್ಷಿತವಾದ ಬಳಕೆ
ಲೇಸರ್ ನ ನಿರ್ವಹಣೆಯನ್ನು ಯೋಗ್ಯವಾದ ಪದ್ಧತಿಯಲ್ಲಿ ಮಾಡದೇ ಇದ್ದಲ್ಲಿ ಮಾತ್ರ ಅದು ತುಂಬಾ ಅಪಾಯಕಾರಿಯಾಗಬಲ್ಲದು. ಕಾರಣ ಲೇಸರ್ ಕಣ್ಣುಗಳಿಗೆ ಕಾಣುವುದಿಲ್ಲ, ಅದರಲ್ಲಿ ಪವರ್ ತುಂಬಾ ಹೆಚ್ಚು ಇರುತ್ತದೆ. ಕಣ್ಣಿನಿಂದ ನೋಡಬಹುದಾದ ಲೇಸರ್ ನ ಪವರ್ ಒಂದು ಅಥವಾ ಎರಡು ವ್ಯಾಟ್ ಇರುತ್ತದೆ. ಇಂದು ನಮ್ಮಲ್ಲಿ 12,000 ವ್ಯಾಟ್ ನ ಮಶಿನ್ ಇದೆ. ಲೇಸರ್ ಇದು ಯಾವಾಗಲೂ ಒಂದೇ ನೇರವಾದ ರೇಖೆಯಲ್ಲಿ ಎಷ್ಟು ದೂರಕ್ಕೂ ತಲುಪಬಲ್ಲದು. ಅದು ಎಷ್ಟು ದೂರಕ್ಕೆ ತಲುಪಿದರೂ ಕೂಡಾ ಅದರ ತೀವ್ರತೆಯು ಕಡಿಮೆಯಾಗುವುದಿಲ್ಲ. ಇದೊಂದು ಲೇಸರ್ ಕುರಿತಾದ ವಿಶೇಷವಾದ ಅಂಶವಾಗಿದೆ. ಇದರಲ್ಲಿ ಲೇಸರ್ ನ ಗುಣಧರ್ಮಗಳು ಬದಲಾಗುವುದಿಲ್ಲ. ಅವುಗಳು ಸ್ಥಿರವಾಗಿರುತ್ತವೆ. ಇದರಿಂದಾಗಿ ಈ ಪ್ರಕ್ರಿಯೆಯು ತುಂಬಾ ಹೆಚ್ಚು ಪ್ರಮಾಣದಲ್ಲಿ ನಿರಂತರವಾದ ಪ್ರಕ್ರಿಯೆ ಎಂದು ತಿಳಿಯಲಾಗುತ್ತದೆ. ಇದರಿಂದಾಗಿ ಲೇಸರ್ ಮಶಿನ್ ನಲ್ಲಿ ಸುರಕ್ಷಿತತೆಗೋಸ್ಕರ ಆವಶ್ಯಕವಿರುವ ಎಲ್ಲ ವೈಶಿಷ್ಟ್ಯಗಳನ್ನು ಅಳವಡಿಸಲಾಗಿದೆ. ಲೇಸರ್ ಮಶಿನ್ ನ ಹೊರ ಭಾಗದಲ್ಲಿ ಫ್ಲೆಕ್ಸಿ ಗ್ಲಾಸ್ ಎಂಬ ವಿಶೇಷವಾದ ಗಾಜುಗಳಿರುವ ತಡೆಗಳಿರುತ್ತವೆ (ಚಿತ್ರ ಕ್ರ. 8). ಈ ಗಾಜಿನಿಂದಾಗಿ ಲೇಸರ್ ಬೀಮ್ ನಲ್ಲಿ ತೀವ್ರತೆಯು (ಇಂಟೆನ್ಸಿಟಿ) ಉಳಿಯದಂತೆ ಡಿಸ್ಟಾರ್ಶನ್ ಆಗುತ್ತದೆ.
ಲೇಸರ್ ಬೀಮ್ ಯಾವುದೇ ಒಂದು ಜಾಗದಲ್ಲಿ ಸ್ಥಿರವಾಗಿ ಇಡುವುದು ಅಸಾಧ್ಯ. ಅದು ನಿರಂತರವಾಗಿ ತಿರುಗುತ್ತಿರಬೇಕು. ಒಂದೇ ಜಾಗದಲ್ಲಿ ಲೇಸರ್ ಸ್ಥಿರವಾಗಿ ಇಟ್ಟಲ್ಲಿ ಆ ಬಿಂದುವಿನ ಕೆಳಗಿರುವ ಕಾರ್ಯವಸ್ತುವಿನೊಂದಿಗೆ ಇನ್ನಿತರ ಮಟೀರಿಯಲ್ ಗಳೂ ಹಾಳಾಗುತ್ತವೆ.
ಲೇಸರ್ ನ ಹೆಡ್ ಮತ್ತು ಮಟೀರಿಯಲ್ ನ ದೂರ ಇದೂ ತುಂಬಾ ಮಹತ್ವದ್ದಾಗಿದೆ. ಕಟಿಂಗ್ ಮಾಡಲಾಗುತ್ತದೆ ಅಥವಾ ಇಲ್ಲವೇ, ಮಾಡಲಾಗುತ್ತಿದ್ದಲ್ಲಿ ಅದರ ಗುಣಮಟ್ಟವು ಯಾವ ಹಂತದಲ್ಲಿರಬಲ್ಲದು, ಮುಂತಾದ ಅಂಶಗಳು ಅದರ ದೂರದಲ್ಲಿ ಅವಲಂಬಿಸಿರುತ್ತವೆ. ಇದರಿಂದಾಗಿ ಅದರಲ್ಲಿ ದೂರವನ್ನು ಶಾಶ್ವತವಾಗಿ ಕಾಪಾಡಲು ಮಶಿನ್ ನಲ್ಲಿ ಉಚ್ಚಮಟ್ಟದ ಇಲೆಕ್ಟ್ರಾನಿಕ್ ಸೆನ್ಸರ್ ತಂತ್ರವು ಒಳಗೊಂಡಿರುತ್ತದೆ. ಉದಾಹರಣೆ, 2 ಮಿ.ಮೀ. ದೂರ ಇಡುವುದಾದಲ್ಲಿ ಸಂಪೂರ್ಣ ಪ್ರಕ್ರಿಯೆಯಲ್ಲಿ ಅಷ್ಟೇ ದೂರವನ್ನು ಅಳವಡಿಸಬೇಕಾಗುತ್ತದೆ.
ದೊಡ್ಡ ಶೀಟ್ ನಿಂದ ಅನೇಕ ಆಕಾರದ ಭಾಗಗಳನ್ನು ಕತ್ತರಿಸುವುದಾದಲ್ಲಿ ನೆಸ್ಟಿಂಗ್ ತಂತ್ರ (ಚಿತ್ರ ಕ್ರ. 9) ಬಳಸಲಾಗುತ್ತದೆ. ವಿವಿಧ ಆಕಾರದ ಭಾಗಗಳನ್ನು ಒಂದೇ ಪ್ಲೇಟ್ ನಿಂದ ಕತ್ತರಿಸಲು ಅದರ ವಿಶಿಷ್ಟ ರಚನೆಯನ್ನು ಮಾಡಿ ಯೋಜನೆಯನ್ನು ತಯಾರಿಸಬೇಕು. ಇದರಿಂದಾಗಿ ಕನಿಷ್ಠ ಪ್ರಮಾಣದಲ್ಲಿ ಮಟೀರಿಯಲ್ ವ್ಯರ್ಥವಾಗುತ್ತದೆ. ಇದಕ್ಕೋಸ್ಕರ ಹಲವಾರು ವಿಶಿಷ್ಟ ರೀತಿಯ ಟೆಸ್ಟರ್ ಗಳಿರುತ್ತವೆ. ಎರಡು ಅಕ್ಕಪಕ್ಕದ ಭಾಗಗಳಲ್ಲಿ ತುಂಡುಗಳನ್ನು ಕಾಪಾಡಲು ಅದನ್ನು ಬಳಸಲಾಗುತ್ತದೆ. ಎರಡು ತುಂಡುಗಳ ನಡುವೆ ವಿಶಿಷ್ಟ ಪ್ರಮಾಣದಲ್ಲಿ ಅಂತರವನ್ನು ಬಿಡಬೇಕಾಗುತ್ತದೆ. ಅದು ಕೂಡಾ ಮಟೀರಿಯಲ್ ನ ದಪ್ಪಕ್ಕೆ ಅವಲಂಬಿಸಿರುತ್ತದೆ. ಎಲ್ಲ ಅಳತೆಗಳನ್ನು ಮಾಡಿ ಒಂದು ಸೀಮೆಯ ರೇಖೆಯನ್ನು ರೇಖಿಸಲಾಗುತ್ತದೆ. ಅದರ ಹೊರಗಿರುವ ಮಟೀರಿಯಲ್ ವ್ಯರ್ಥವಾಗುತ್ತದೆ.
ಹಣಕಾಸಿಗೆ ಸಂಬಂಧಪಟ್ಟ ಅಂಶಗಳು
ಖರ್ಚಿನ ಕುರಿತು ವಿಚಾರ ಮಾಡಿದರೆ, ಗ್ಯಾಸ್ ಕಟಿಂಗ್ ಮಶಿನ್ ಮತ್ತು ಲೇಸರ್ ಕಟಿಂಗ್ ಮಶಿನ್ ಇವೆರಡನ್ನು ಹೋಲಿಸಿದಲ್ಲಿ ಲೇಸರ್ ಕಟಿಂಗ್ ಮಶಿನ್ 8-10 ಪಟ್ಟು ದುಬಾರಿಯಾಗಿರುತ್ತದೆ. ಅದರ ಪ್ರಕ್ರಿಯೆಯ ಖರ್ಚು ನಾಲ್ಕು ಪಟ್ಟು ಇರುತ್ತದೆ. ಗ್ಯಾಸ್ ಕಟಿಂಗ್ ಮಾಡಿ ಕೆಲಸ ನಿರ್ವಹಿಸುವಲ್ಲಿ ಲೇಸರ್ ಖಂಡಿತವಾಗಿಯೂ ಉಪಯುಕ್ತವಾಗಿರುವುದಿಲ್ಲ. ಒಂದು ವೇಳೆ ಲೇಸರ್ ನ ಬೆಲೆಯು ಕಡಿಮೆಯಾದರೂ ಕೂಡಾ ಅದರ ಪ್ರಕ್ರಿಯೆಯ ಖರ್ಚು ಮಾತ್ರ ತುಂಬಾ ಹೆಚ್ಚು ಇರುತ್ತದೆ. ಇದು ಕೇವಲ ಮಶಿನ್ ನ ಕುರಿತಾಗಿ ಅಲ್ಲದೇ, ಅದಕ್ಕೆ ಬೇಕಾಗುವ ಎಲ್ಲ ರೀತಿಯ ಕನ್ಸುಮೇಬಲ್ ಇತ್ಯಾದಿ ಎಲ್ಲ ಸಾಮಗ್ರಿಗಳೂ ದುಬಾರಿಯಾಗಿರುತ್ತವೆ. ಆದರೆ ಉತ್ಪಾದಕತೆ ಮತ್ತು ಗುಣಮಟ್ಟದ ನಿಟ್ಟಿನಲ್ಲಿ ನೋಡಿದಾಗಿ ಆ ಖರ್ಚು ಕಡಿಮೆ ಅನಿಸುತ್ತದೆ. ಹಾಗೆಯೇ ಲೇಸರ್ ನಿಂದಾಗಿ ಕಡಿಮೆಯಾಗುವ ಉತ್ಪಾದನೆಯ ಖರ್ಚಿನ ವ್ಯತ್ಯಾಸವು ಇದನ್ನು ಸರಿಹೊಂದಿಸುತ್ತದೆ. ಹಾಗೆಯೇ ಕಟಿಂಗ್ ನಂತರ ಯಾವುದೇ ಪ್ರಕ್ರಿಯೆಯನ್ನು ಮಾಡುವ ಆವಶ್ಯಕತೆ ಇಲ್ಲದಿರುವುದರಿಂದ ಅದಕ್ಕೋಸ್ಕರ ತಗಲುವ ಖರ್ಚು ಕಡಿಮೆಯಾಗುತ್ತದೆ. ಇದರಿಂದಾಗಿಯೇ ಲೇಸರ್ ಕಡಿಮೆ ಸಮಯದಲ್ಲಿ ತುಂಬಾ ಪ್ರಸಿದ್ಧವಾಗಿದೆ. ಕೆಲಸದ ವೇಳೆ ಕಡಿಮೆ ಮಾಡಲು ಈ ಪ್ರಕ್ರಿಯೆಯು ತುಂಬಾ ಪ್ರಭಾವಶಾಲಿಯಾಗಿದೆ.
ಯಾವುದೇ ಯಂತ್ರಭಾಗದ ಡಿಸೈನ್ ಆಗುತ್ತಿರುವಾಗ ಅದನ್ನು ಲೇಸರ್ ಪ್ರಕ್ರಿಯೆಯಿಂದಲೇ ಮಾಡುವುದು, ಎಂಬುದನ್ನು ಪ್ರಾರಂಭದಲ್ಲಿಯೇ ನಿರ್ಧರಿಸಬೇಕಾಗುತ್ತದೆ. ಅದಕ್ಕೆ ಅನುಸಾರವಾಗಿ ಡಿಸೈನ್ ನಲ್ಲಿ ಆವಶ್ಯಕವಿರುವ ಎಲ್ಲ ರೀತಿಯ ವೈಶಿಷ್ಟ್ಯಗಳನ್ನು ಅಳವಡಿಸಬೇಕಾಗುತ್ತದೆ. ಶೀಘ್ರವಾದ ಮತ್ತು ನಿರ್ದೋಷವಾದ ಉತ್ಪಾದನೆಗೋಸ್ಕರ ಲೇಸರ್ ಪ್ರಕ್ರಿಯೆಯು ಪ್ರಭಾವಶಾಲಿಯಾಗುತ್ತದೆ, ಇದರಲ್ಲಿ ಯಾವುದೇ ರೀತಿಯ ಸಂಶಯವಿಲ್ಲ.