ಡ್ರಿಲ್ಲಿಂಗ್ ಪ್ರಕ್ರಿಯೆಯಲ್ಲಿ ಕಾರ್ಯವಸ್ತುಗಳಲ್ಲಿರುವ ರಂಧ್ರಗಳನ್ನು ಯಂತ್ರಣೆಯನ್ನು ಮಾಡಿ ತಯಾರಿಸಲಾಗುತ್ತದೆ. ಆದರೆ ರಂಧ್ರಗಳ ಆಳವು ಜಾಸ್ತಿ ಇದ್ದಲ್ಲಿ, ಚಿಪ್ ನಿಯಂತ್ರಣೆ ಮತ್ತು ಅವುಗಳನ್ನು ದೂರ ಒಯ್ಯುವ ನಿಟ್ಟಿನಲ್ಲಿ ಅದರಲ್ಲಿ ಬೇರೆಯೇ ರೀತಿಯ ಆವಶ್ಯಕತೆ ಇರುತ್ತದೆ. ಡ್ರಿಲ್ಲಿಂಗ್ ನಲ್ಲಿ ಶಾರ್ಟ್ ಹೋಲ್ ಡ್ರಿಲ್ಲಿಂಗ್ ಮತ್ತು ಡೀಪ್ ಹೋಲ್ ಡ್ರಿಲ್ಲಿಂಗ್ ಎಂಬುದನ್ನು ಅವುಗಳ ಕೆಲಸಕ್ಕೆ ಅನುಗುಣವಾಗಿ ವರ್ಗೀಕರಿಸಲಾಗಿದೆ.
ಉದ್ದ ಮತ್ತು ವ್ಯಾಸದ ಗುಣಾಕಾರವು (L/D) 5 ಕ್ಕಿಂತ ಕಡಿಮೆ ಇರುವಾಗ ಅದಕ್ಕೆ ಶಾರ್ಟ್ ಹೋಲ್ ಡ್ರಿಲ್ಲಿಂಗ್ ಎಂಬುದಾಗಿ ಹೇಳುತ್ತಾರೆ. ಈ ಗುಣಾಕಾರವು 5 ಕ್ಕಿಂತ ಹೆಚ್ಚು ಇರುವಾಗ ಅದನ್ನು ಲಾಂಗ್ ಹೋಲ್ ಡ್ರಿಲ್ಲಿಂಗ್ ಎಂದು ಹೇಳುತ್ತಾರೆ. L ಅಂದರೆ ರಂಧ್ರದ ಆಳ ಮತ್ತು D ಅಂದರೆ ರಂಧ್ರದ ವ್ಯಾಸವಾಗಿದೆ.
ಡ್ರಿಲ್ಲಿಂಗ್ ನಲ್ಲಿ ಎರಡು ಪದ್ಧತಿಗಳಿವೆ. ಸಾಲಿಡ್ ಡ್ರಿಲ್ಲಿಂಗ್ ಅಂದರೆ ಘನ ಪದಾರ್ಥಗಳಿಗೆ ಮಾಡಲಾಗುವ ಡ್ರಿಲ್ಲಿಂಗ್ ಮತ್ತು ಟ್ರಿಪ್ಯಾನಿಂಗ್ ಅಂದರೆ ಕೋರ್ ರಂಧ್ರ ಅಥವಾ ಕಾಸ್ಟ್ ಮಾಡಿರುವ ರಂಧ್ರದ ಆಕಾರವನ್ನು ಹೆಚ್ಚಿಸಲು ಮಾಡಲಾಗಿರುವ ಕೆಲಸ. ಇನ್ನೊಂದು ರೀತಿಯನ್ನು ಸಾಮಾನ್ಯವಾಗಿ ದೊಡ್ಡ ರಂಧ್ರಗಳಿಗೆ ಬಳಸಲಾಗುತ್ತದೆ.
• ಟೇಪರ್ ಮತ್ತು ಸ್ಟ್ರೇಟ್ ಶ್ಯಾಂಕ್ ಡ್ರಿಲ್
• 2 ಫ್ಲ್ಯೂಟ್, 3 ಫ್ಲ್ಯೂಟ್ ಮತ್ತು 4 ಫ್ಲ್ಯೂಟ್ ಗಳಿರುವ ಡ್ರಿಲ್
ಸಾಮಾನ್ಯವಾಗಿ ಸಾಲಿಡ್ ಡ್ರಿಲ್ಲಿಂಗ್ ನಲ್ಲಿ ಮೊದಲಾಗಿ ರಂಧ್ರಗಳನ್ನು ತಯಾರಿಸಲು 2 ಫ್ಲ್ಯೂಟ್ ಇರುವ ಡ್ರಿಲ್ ಬಳಸಲಾಗುತ್ತದೆ. ಆದರೆ ಮುಂಚೆ ಮಾಡಿರುವ ರಂಧ್ರಗಳನ್ನು ಡ್ರಿಲ್ ಮಾಡಲು ಅಥವಾ ಫಿನಿಶ್ ಮಾಡಲು 3 ಫ್ಲ್ಯೂಟ್ ಮತ್ತು 4 ಫ್ಲ್ಯೂಟ್ ಇರುವ ಡ್ರಿಲ್ ಬಳಸಲಾಗುತ್ತದೆ.
ಡ್ರಿಲ್ ಟೂಲ್ ಜಾಮೆಟ್ರಿ (ಚಿತ್ರ ಕ್ರ. 1) ರಂಧ್ರದ ಯೋಗ್ಯ ಆಕಾರ ತಯಾರಿಸುವಲ್ಲಿ ಮತ್ತು ಒಟ್ಟಾರೆ ಕಾರ್ಯಸಾಮರ್ಥ್ಯದಲ್ಲಿ ಮಹತ್ವದ ಪಾತ್ರವನ್ನು ವಹಿಸುತ್ತದೆ. ಡ್ರಿಲ್ ನ ತಯಾರಿಕೆಯಲ್ಲಿರುವ ಜಾಮೆಟ್ರಿಗಳ ಪ್ಯಾರಾಮೀಟರ್ ಗಳ ಕುರಿತು ಈ ಕೆಳಗಿನಂತೆ ವಿಚಾರ ಮಾಡಲಾಗುತ್ತದೆ.
1. ಬಿಂದು ಕೋನ (ಪಾಯಿಂಟ್ ಎಂಗಲ್)
ಮಟೀರಿಯಲ್ ಗಳಿಗೆ ಅನುಸಾರವಾಗಿ ಸ್ಟ್ಯಾಂಡರ್ಡ್ ಡ್ರಿಲ್ ಟೂಲ್ ನಲ್ಲಿ ಸಾಮಾನ್ಯವಾಗಿ 90˚ ಯಿಂದ 180˚ ಯ ತನಕದ ಬಿಂದು ಕೋನವನ್ನು (ಚಿತ್ರ ಕ್ರ. 3) ಬಳಸಲಾಗುತ್ತದೆ.
2. ಹೆಲಿಕ್ಸ್ ಕೋನ
ಹೆಲಿಕ್ಸ್ ಕೋನ ಕಡಿಮೆ (10˚ ಯಿಂದ 20˚ಯ ದೂರದಲ್ಲಿ) ಇದ್ದಲ್ಲಿ ಚಿಪ್ ಹೊರಗೆ ತೆಗೆಯುವುದು ಸುಲಭವಾಗುತ್ತದೆ. ಡೀಪ್ ಹೋಲ್ ಡ್ರಿಲ್ಲಿಂಗ್ ನಲ್ಲಿ ಕಡಿಮೆ ಕೋನವನ್ನು ಬಳಸಲಾಗುತ್ತದೆ. ಉಚ್ಚಮಟ್ಟದ ಹೆಲಿಕ್ಸ್ ಕೋನ (30˚ ಯಿಂದ 40˚ ತನಕ) ಶಾರ್ಟ್ ಡ್ರಿಲ್ ಹೋಲ್ ನ ಕೆಲಸದ ನಿರ್ವಹಣೆಯನ್ನು ಬಳಸಲಾಗುತ್ತದೆ.
3. ಡ್ರಿಲ್ ನಲ್ಲಿರುವ ಟೇಪರ್
ಯೋಗ್ಯವಾದ ಮತ್ತು ಪರಿಣಾಮಕಾರಿಯಾದ ಡ್ರಿಲ್ಲಿಂಗ್ ಗೋಸ್ಕರ ಇದು ತುಂಬಾ ಮಹತ್ವದ ನಿಯತಾಂಕವಾಗಿದೆ. ಅಲ್ಲದೇ ರಿಗ್ರೈಂಡಿಗ್ ನ ಸಂಖ್ಯೆಯೂ ಇದರಲ್ಲಿ ಅವಲಂಬಿಸಿರುತ್ತದೆ.
ಡ್ರಿಲ್ಲಿಂಗ್ ಯೋಗ್ಯವಾಗಿ ಮಾಡಲು ಡ್ರಿಲ್ ನ ಆಯ್ಕೆಯನ್ನು ಮಾಡುವಾಗ ಈ ಕೆಳಗಿನ ನಿಯತಾಂಕಗಳ ಅರಿವು ಇರುವುದು ಅತ್ಯಾವಶ್ಯಕವಾಗಿದೆ.
ಎ. ರಂಧ್ರದ ವ್ಯಾಸ ಮತ್ತು ಆಳ
ಬಿ. ಯಂತ್ರಭಾಗಗಳ ಆಕಾರ
ಸಿ. ವ್ಯಾಸದಲ್ಲಿ ಅಪೇಕ್ಷಿಸಿರುವ ಟಾಲರನ್ಸ್
ಡಿ. ಕಾರ್ಯವಸ್ತುಗಳಿಗೆ ಬೇಕಾಗುವ ಮಟೀರಿಯಲ್
ಇ. ಮಶಿನ್ ನ ಬಲ ಮತ್ತು ಸ್ಥಿರತೆ.
ಪರಿಮಾಣಗಳನ್ನು ಸೂಕ್ತ ರೀತಿಯಲ್ಲಿ ಆಯ್ಕೆ ಮಾಡಲು ಮೇಲಿನ ನಿಯತಾಂಕಗಳ ವಿವರಗಳು ಈ ಕೆಳಗಿನಂತಿವೆ.
ಅ. ರಂಧ್ರದ ವ್ಯಾಸವು 12.5 ಕ್ಕಿಂತ ಕಡಿಮೆ ಇದ್ದಲ್ಲಿ ಸಾಲಿಡ್ ಕಾರ್ಬೈಡ್ ಡ್ರಿಲ್ ನ ಆಯ್ಕೆಯನ್ನು ಮಾಡಬಲ್ಲೆವು. ಈ ಆಯ್ಕೆಯು ಮಶಿನ್ ನ ಸಾಮರ್ಥ್ಯದಲ್ಲಿಯೂ ಅವಲಂಬಿಸಿರುತ್ತದೆ. ಮಶಿನ್ ನ ಸಾಮರ್ಥ್ಯ ನಿಗದಿತ ಮಿತಿಯಲ್ಲಿದ್ದಲ್ಲಿ ಎಚ್.ಎಸ್.ಎಸ್. ಡ್ರಿಲ್ ಆಯ್ಕೆ ಮಾಡಬೇಕು. ಚಿಪ್ ಸಿಲುಕುವುದನ್ನು ತಡೆಯಲು ಯಾವಾಗಲೂ ಆರುಪಾರಾಗಿ ಕೂಲಂಟ್ ಹೋಗುವ ಡ್ರಿಲ್ ಆಯ್ಕೆ ಮಾಡಬೇಕು. ಅತಿ ಚಿಕ್ಕದಾದ ರಂಧ್ರವಿದ್ದಲ್ಲಿ ಆರುಪಾರು ಕೂಲಂಟ್ ನ ಪ್ರಣಾಳಿಕೆಯು ಇಲ್ಲದಿರುವ ಡ್ರಿಲ್ ಹೊರತಾಗಿ ಇನ್ನಿತರ ಯಾವುದೇ ಪರ್ಯಾಯ ಲಭ್ಯವಿಲ್ಲ. 12.5 ರಿಂದ 40 ಮಿ.ಮೀ. ವ್ಯಾಸದ ದೂರಕ್ಕೋಸ್ಕರ ಇಂಡೆಕ್ಸೆಬಲ್ ಈ ವಿಧದ ಡ್ರಿಲ್ ನ್ನು ಆಯ್ಕೆ ಮಾಡಬಹುದು. ಇಂತಹ ಪರಿಸ್ಥಿತಿಯಲ್ಲಿ ರಂಧ್ರದ ನಿಖರತೆಯ ಕುರಿತು ವಿಚಾರ ಮಾಡುವುದೂ ಅತ್ಯಾವಶ್ಯಕವಾಗಿದೆ. ಯಂತ್ರಣೆಯ ವೇಗ ಮತ್ತು ಫೀಡ್ ರೇಟ್ ಹೆಚ್ಚು ಪ್ರಮಾಣದಲ್ಲಿ ಬಳಸುವ ಸಾಧ್ಯತೆ ಇರುವಾಗ ನಿಖರವಾದ ಟಾಲರನ್ಸ್ ನ ಆವಶ್ಯಕತೆ ಇರುತ್ತದೆ. ರಂಧ್ರಗಳ ಆಳ ಹೆಚ್ಚು (L/D>4) ಪ್ರಮಾಣದಲ್ಲಿ ಇರುವಾಗ ಇಂಡೆಕ್ಸೆಬಲ್ ಡ್ರಿಲ್ ಯೋಗ್ಯವಾಗಿರಲಾರದು.
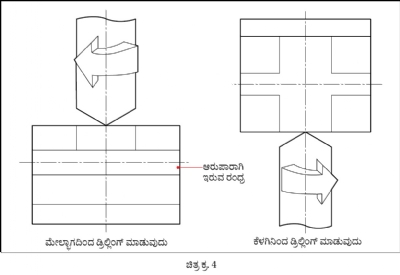
ಆ. ವಾಲುವ (ಟಿಲ್ಟಿಂಗ್) ಸರ್ಫೇಸ್ ಅಥವಾ ಕ್ರಾಸ್ ಹೋಲ್ ಡ್ರಿಲ್ಲಿಂಗ್ ಇರುವ ಹೊರ ಭಾಗ ವರ್ತುಲಾಕಾರ ಅಥವಾ ಒಳ ಭಾಗದಲ್ಲಿರುವ ವರ್ತುಲಾಕಾರ ಸರ್ಫೇಸ್ ನ ಕೆಲಸದ ನಿರ್ವಹಣೆಯಲ್ಲಿ ಇಂಡೆಕ್ಸೆಬಲ್ ಡ್ರಿಲ್ ಗೆ ಮೊದಲ ಆದ್ಯತೆ ನೀಡಲಾಗುತ್ತದೆ. ಸರ್ಫೇಸ್ ಗಳ ಮಾದರಿಯನ್ನು ಚಿತ್ರ ಕ್ರ. 2 ರಲ್ಲಿ ನೀಡಲಾಗಿದೆ. ಇಂತಹ ಕೆಲಸಗಳಲ್ಲಿ ಯಾವಾಗಲೂ ಫೀಡ್ ರೇಟ್ 30% ಕ್ಕಿಂತ ಕಡಿಮೆ ಇಡಬೇಕು. ಎರಡನೇ ರಂಧ್ರದ ಅಕ್ಷಗಳನ್ನು ಕತ್ತರಿಸುವ ರಂಧ್ರಗಳ ಡ್ರಿಲ್ಲಿಂಗ್ ಮಾಡುವುದಾದಲ್ಲಿ ಡ್ರಿಲ್ ಒಂದೇ ಒಳ ಭಾಗದಲ್ಲಿರುವ ವರ್ತುಲಾಕಾರದ ಸರ್ಫೇಸ್ ನಿಂದ ಹೊರಗೆ ಬರುತ್ತದ. ಎರಡನೇ ಒಳ ಭಾಗದ ವರ್ತುಲಾಕಾರದಲ್ಲಿ ಪ್ರವೇಶಿಸುತ್ತದೆ. ಇಂತಹ ಕೆಲಸಗಳಲ್ಲಿ ಯಾವಾಗಲೂ ಚಿಪ್ ಹೊರಗೆ ತೆಗೆಯುವ ಸಮಸ್ಯೆಯು ಕಂಡುಬರುತ್ತದೆ. ಚಿತ್ರ ಕ್ರ. 4 ರಲ್ಲಿ ತೋರಿಸಿದಂತೆ ಎರಡೂ ಬದಿಗಳಲ್ಲಿ ಡ್ರಿಲ್ಲಿಂಗ್ ಆಪರೇಶನ್ ಮಾಡಿಯೇ ಈ ಸಮಸ್ಯೆಯನ್ನು ನೀಗಿಸಬಹುದು. ಮೊದಲ ಸೆಟಪ್ ನಲ್ಲಿ ಕ್ರಾಸ್ ಹೋಲ್ ನಲ್ಲಿ ರಂಧ್ರಗಳು ತೆರೆಯುವ ತನಕ ಡ್ರಿಲ್ಲಿಂಗ್ ಮಾಡಲಾಗುತ್ತದೆ. ಡ್ರಿಲ್ ಒಳ ಭಾಗದಲ್ಲಿರುವ ವರ್ತುಲಾಕಾರದ ಸರ್ಫೇಸ್ ನಲ್ಲಿ ಪ್ರವೇಶಿಸುವಾಗ ಫೀಡ್ ರೇಟ್ ಶೇಕಡಾ 20 ರಿಂದ 30 ರಷ್ಟು ಕಡಿಮೆ ಮಾಡಬೇಕು. ಚಿತ್ರ ಕ್ರ. 2 ರಲ್ಲಿರುವ ಎರಡನೇ ಸೆಟಪ್ ನಲ್ಲಿ ತೋರಿಸಿದಂತೆ ಕೆಳ ಭಾಗದಲ್ಲಿ ಡ್ರಿಲ್ ಮಾಡಬೇಕಾಗಬಹುದು. ಒಂದು ವೇಳೆ ಒಂದೇ ಕೆಲಸದಲ್ಲಿ ಅನೇಕ ಆಕಾರದ ರಂಧ್ರಗಳನ್ನು ತಯಾರಿಸುವುದಾದಲ್ಲಿ ಅದಕ್ಕೋಸ್ಕರ ಡ್ರಿಲ್ಲಿಂಗ್ ಪ್ರಕ್ರಿಯೆಯನ್ನು ಹೇಗೆ ನಿರ್ವಹಿಸಬೇಕು ಎಂಬುದನ್ನು ಚಿತ್ರ ಕ್ರ. 5 ರಲ್ಲಿ ತೋರಿಸಲಾಗಿದೆ. ಮೊದಲಾಗಿ ಒಂದು ದೊಡ್ಡ ರಂಧ್ರವನ್ನು ಮಾಡಬೇಕು ಮತ್ತು ನಂತರ ಕಡಿಮೆ ಫೀಡ್ ರೇಟ್ ಅಳವಡಿಸಿ ಚಿಕ್ಕ ರಂಧ್ರಗಳನ್ನು ಮಾಡಬೇಕಾಗಬಹುದು. ಇನ್ನೊಂದು ಬದಿಯಿಂದ ಬೇಕಾಗಿರುವ ಆಳದಷ್ಟು ಮೂರನೇ ಡ್ರಿಲ್ ಮಾಡಬೇಕು. ಈ ಡ್ರಿಲ್ಲಿಂಗ್ ನಲ್ಲಿಯೂ ತುಂಡಾಗಬಲ್ಲ, ಒವ್ಯಾಲಿಟಿ ಮತ್ತು ರಂಧ್ರಗಳ ತಪ್ಪಾದ ಆಕಾರವನ್ನು ತಡೆಯಲು ಫೀಡ್ ರೇಟ್ ಕಡಿಮೆ ಇಡುವುದು ಅಗತ್ಯವಾಗಿದೆ.
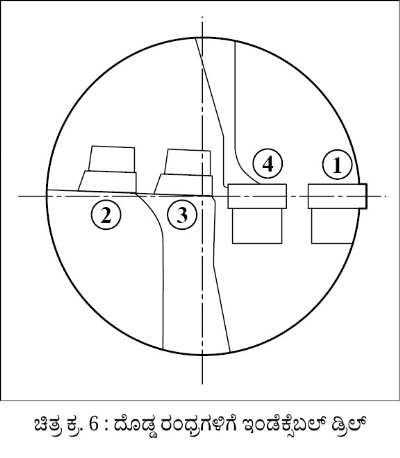
ಇ. 35 ಮಿ.ಮೀ.ಗಿಂತ ಹೆಚ್ಚು ವ್ಯಾಸದ ದೊಡ್ಡ ರಂಧ್ರಗಳನ್ನು ಮಾಡುವಾಗ ಮಶಿನ್ ನ ಸಾಮರ್ಥ್ಯವನ್ನೂ ಪರಿಶೀಲಿಸಬೇಕು. ಡ್ರಿಲ್ಲಿಂಗ್ ನಲ್ಲಿ ಗರಿಷ್ಠ ಕತ್ತರಿಸುವ ಬಲ (ಕಟಿಂಗ್ ಫೋರ್ಸ್) ಅಕ್ಷೀಯ ದಿಕ್ಕಿನಲ್ಲಿ ಇರುತ್ತದೆ. ಥ್ರಸ್ಟ್ ಲೋಡ್ ಕೂಡಾ ಹೆಚ್ಚು ಇರುತ್ತದೆ. ಇದಕ್ಕೋಸ್ಕರ ಹೆಚ್ಚು ಸ್ಪಿಂಡಲ್ ಬಲವು ಅತ್ಯಾವಶ್ಯಕವಾಗಿದೆ. ಉಚ್ಚ ಸಾಮರ್ಥ್ಯ ಇರುವ ಮಶಿನ್ ನಲ್ಲಿ ಇಂಡೆಕ್ಸೆಬಲ್ ವಿಧದ ಡ್ರಿಲ್ ಬಳಸಿ ದೊಡ್ಡ ರಂಧ್ರಗಳನ್ನು ಮಾಡುವುದೂ ಸಾಧ್ಯ. ಚಿತ್ರ ಕ್ರ. 6 ರಲ್ಲಿ ಟೂಲ್ ನ ಫ್ರಂಟ್ ವ್ಯೂ ತೋರಿಸಲಾಗಿದೆ. ಇದರಲ್ಲಿ ಅನೇಕ ರೀತಿಯ ಪ್ಲೇನ್ ಗಳಲ್ಲಿ 4 ಇನ್ಸರ್ಟ್ ಗಳನ್ನು ಅಳವಡಿಸಲಾಗಿದೆ. ಈ ಇನ್ಸರ್ಟ್ ನ ಡ್ರಿಲ್ ನಲ್ಲಿರುವ ಸ್ಥಾನವನ್ನು ಮಟೀರಿಯಲ್ ನಿಧಾನವಾಗಿ ಪ್ರವೇಶಿಸುವಂತೆ ಮತ್ತು ಕಟಿಂಗ್ ಫೋರ್ಸ್ ಕಡಿಮೆಯಾಗುವಂತೆ ಅಳವಡಿಸಲಾಗಿರುತ್ತದೆ. ಡ್ರಿಲ್ಲಿಂಗ್ ಗೋಸ್ಕರ ಆವಶ್ಯಕವಿರುವ ಬಲದ ಕುರಿತಾದ ವಿಶ್ಲೇಷಣೆಯನ್ನು ಮಾಡುವುದು ಯಾವಾಗಲೂ ಆವಶ್ಯಕವಾಗಿದೆ.
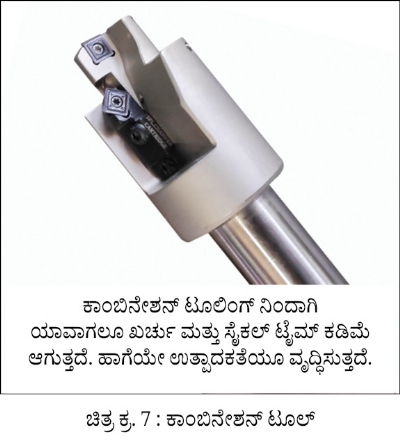
ಈ. ಕೋಷ್ಟಕ ಕ್ರ. 1 ರಲ್ಲಿ ಕೆಲಸದ ಆವಶ್ಯಕತೆಗೆ ಅನುಸಾರವಾಗಿ ಡ್ರಿಲ್ ನ ಆಯ್ಕೆ ಹೇಗೆ ಮಾಡಬೇಕು ಎಂಬುದನ್ನುನೀಡಲಾಗಿದೆ. ಒಂದು ವಿಶಿಷ್ಟವಾದ ಡ್ರಿಲ್ ನ ಆಳಕ್ಕೋಸ್ಕರ ರಂಧ್ರಗಳ ವ್ಯಾಸದ ಟಾಲರನ್ಸ್ ಕಡಿಮೆ ಪ್ರಮಾಣದಲ್ಲಿ ಲಭಿಸಬಲ್ಲದು, ಈ ಕುರಿತಾದ ಮಾಹಿತಿಯನ್ನು ಈ ಕೋಷ್ಟಕದಿಂದ ತಿಳಿದುಕೊಳ್ಳಬಹುದು. ಮಿತಿಯಲ್ಲಿರುವ ಡ್ರಿಲ್ ನ ಆಳ ಮತ್ತು ರಂಧ್ರಗಳ ಟಾಲರನ್ಸ್ ಗೋಸ್ಕರ ಇಂಡೆಕ್ಸೆಬಲ್ ಅಥವಾ ಇನ್ಸರ್ಟ್ ರೀತಿಯ ಡ್ರಿಲ್ ಬಳಸಲಾಗುತ್ತದೆ. ಡ್ರಿಲ್ ನ ಆಳ 5D ಗಿಂತ ಹೆಚ್ಚು, 8D ಯಷ್ಟು ಇರುವಲ್ಲಿ ಕಟಿಂಗ್ ಫೋರ್ಸ್ ಸಹಿಸಲು ಟೂಲ್ ಮಟೀರಿಯಲ್ ಸಾಕಷ್ಟು ಪ್ರಮಾಣದಲ್ಲಿ ಕಠಿಣವಾಗಿ ಇರಬೇಕಾಗುತ್ತದೆ. ಡೀಪ್ ಹೋಲ್ ಡ್ರಿಲ್ಲಿಂಗ್, ಆಯಿಲ್ ಹೋಲ್ ಇಂತಹ ಕೆಲಸಗಳಲ್ಲಿ ಆವಶ್ಯಕವಿರುವ ಆಳದಲ್ಲಿ ರಂಧ್ರಗಳನ್ನು ಮಾಡುವುದಾದಲ್ಲಿ, ಅದಕ್ಕೆ ಬಳಸಲಾಗುವ ಟೂಲ್ ಗೆ ಗನ್ ಡ್ರಿಲ್ ಎಂದು ಕರೆಯುತ್ತಾರೆ. ಈ ರೀತಿಯ ಕೆಲಸಗಳಲ್ಲಿ ಡ್ರಿಲ್ ನ ಮುಂಭಾಗದಲ್ಲಿ ಘನ ಕಾರ್ಬೈಡ್ ನ ಟೂಲ್ ಬ್ರೇಝಿಂಗ್ ಮಾಡಲಾಗುತ್ತದೆ. ಅದರಲ್ಲಿ ಸಿಂಗಲ್ ಫ್ಲ್ಯೂಟ್ ಇರುವುದೂ ಅತ್ಯಾವಶ್ಯಕವಾಗಿದೆ. ಡೀಪ್ ಹೋಲ್ ಡ್ರಿಲ್ಲಿಂಗ್ ನ ಕೆಲಸಕ್ಕೋಸ್ಕರ ವಿಶೇಷವಾದ ಮಶಿನ್ ಗಳ ಅಗತ್ಯವೂ ಇರುತ್ತದೆ.
ಪ್ರಸ್ತುತ ಪ್ರಕ್ರಿಯೆಯನ್ನು ಹೋಲಿಸಿದಲ್ಲಿ ಇಂಡೆಕ್ಸೆಬಲ್ ಡ್ರಿಲ್ ಎಷ್ಟು ಲಾಭಕಾರಿಯಾಗಿದೆ ಎಂಬುದನ್ನು ಈ ಕೆಳಗಿನ ಉಪಕರಣಗಳಿಂದ ತಿಳಿದುಕೊಳ್ಳೋಣ.
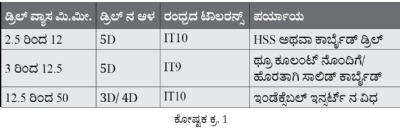
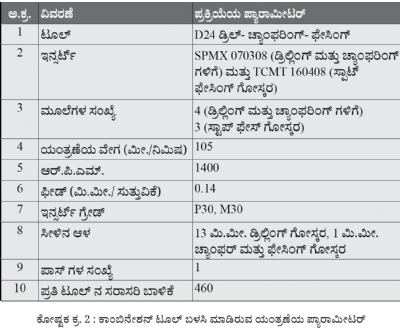
ಡ್ರಿಲ್ಲಿಂಗ್ ನಂತರ ರಂಧ್ರಗಳ ಬದಿಗಳು ಚೂಪಾಗಿವೆಯೇ ಅಥವಾ ಅಲ್ಲಿ ಬರ್ ಜಮೆಯಾಗಿದೆಯೇ ಎಂಬುದು ಕಂಡುಬರುತ್ತದೆ. ಅದನ್ನು ನೀಗಿಸಲು ಚ್ಯಾಂಫರ್ ತಯಾರಿಸಬೇಕು ಅಥವಾ ಬರ್ ತೆಗೆದು ಹಾಕಬೇಕು. ಟ್ಯಾಪಿಂಗ್ ನಂತಹ ನಂತರದ ಕ್ರಿಯೆಗಳಿಗೆ ಚ್ಯಾಂಫರ್ ಅಗತ್ಯವಾಗಿರುತ್ತದೆ ಅಥವಾ ಅಸೆಂಬ್ಲಿಗೂ ಕೂಡಾ ಉಪಯುಕ್ತವಾಗಿರುತ್ತದೆ. ಇಂತಹ ಪರಿಸ್ಥಿತಿಯಲ್ಲಿ ಗ್ರಾಹಕರು ಚಿತ್ರ ಕ್ರ. 7 ರಲ್ಲಿ ತೋರಿಸಿದಂತೆ ಕಾಂಬಿನೇಶನ್ ಟೂಲಿಂಗ್ ಬಳಸುತ್ತಾರೆ. ಚಿತ್ರದಲ್ಲಿ ತೋರಿಸಿದಂತೆ ಹಲವಾರು ಉತ್ಪಾದನೆಗಳಲ್ಲಿ ಡ್ರಿಲ್ಲಿಂಗ್ ನಂತರ ಫೇಸಿಂಗ್, ಚ್ಯಾಂಫರಿಂಗ್ ನಂತಹ ಕೆಲಸಗಳೂ ಅತ್ಯಾವಶ್ಯಕವಾಗಿವೆ. ಚಿತ್ರ ಕ್ರ. 8 ರಲ್ಲಿ ತೋರಿಸಿರುವ ಕಾರ್ಯವಸ್ತುವು ಕ್ರ್ಯಾಂಕ್ ಶಾಫ್ಟ್ ಆಗಿರುತ್ತದೆ. ಇದರಲ್ಲಿ ಡ್ರಿಲ್ಲಿಂಗ್, ಚ್ಯಾಂಫರಿಂಗ್ ಮತ್ತು ಸ್ಪಾಟ್ ಫೇಸಿಂಗ್ ನಂತಹ ಕೆಲಸಗಳನ್ನು ನಿರ್ವಹಿಸುವುದು ಸಾಧ್ಯ. ಕಾಂಬಿನೇಶನ್ ಟೂಲ್ ಮೂರೂ ಕೆಲಸಗಳನ್ನು ಒಂದೇ ಸೆಟಪ್ ನಲ್ಲಿ ಪೂರ್ತಿಗೊಳಿಸುತ್ತದೆ. ಮೊದಲಾಗಿ ಡ್ರಿಲ್ಲಿಂಗ್, ಅದರ ನಂತರ ಚ್ಯಾಂಫರ್ ಮತ್ತು ಸ್ಪಾಟ್ ಫೇಸ್ ಮಾಡಲಾಗುತ್ತದೆ. ಡ್ರಿಲ್ಲಿಂಗ್ ಮತ್ತು ಚ್ಯಾಂಫರಿಂಗ್ ಗೋಸ್ಕರ ಅದೇ ಇನ್ಸರ್ಟ್ ಬಳಸಲಾಗುತ್ತದೆ. ಸ್ಪಾಟ್ ಫೇಸಿಂಗ್ ಗೋಸ್ಕರ ಸ್ವತಂತ್ರವಾದ ಇನ್ಸರ್ಟ್ ಇರುತ್ತದೆ. ಪ್ಯಾರಾಮೀಟರ್ ಗಳ ವಿವರಗಳನ್ನು ಕೋಷ್ಟಕ ಕ್ರ. 2 ರಲ್ಲಿ ನೀಡಲಾಗಿದೆ.
ಅನೇಕ ಬಾರಿ ಗ್ರಾಹಕರು ತಮ್ಮಲ್ಲಿರುವ ಪ್ರಕ್ರಿಯೆಯ ಖರ್ಚನ್ನು ಕಡಿಮೆ ಮಾಡಲು ಕಡಿಮೆ ಬೆಲೆಯ ಟೂಲಿಂಗ್ ಬಳಸುತ್ತಾರೆ. ಆದರೆ ಸಾಮಾನ್ಯವಾಗಿ ಅದರ ಪರಿಣಾವು ಉತ್ಪಾದನೆಯ ಸಾಮರ್ಥ್ಯದಲ್ಲಿ ಬೀರುತ್ತದೆ. ಕಾರಣ ಆಗಾಗ ಟೂಲ್ ಬದಲಾಯಿಸಬೇಕಾಗುತ್ತದೆ. ಉಚ್ಚಮಟ್ಟದ ಟೂಲಿಂಗ್ ಕಾರ್ಯಗತಗೊಳಿಸಿ ಕಡಿಮೆ ಖರ್ಚಿನಲ್ಲಿ ಉತ್ಪಾದನೆಯನ್ನು ಹೇಗೆ ಸುಧಾರಿಸಲು ದೀರ್ಘಕಾಲಾವಧಿಯ ಉಪಾಯಗಳನ್ನು ಹುಡುಕುವುದೂ ಅಗತ್ಯವಾಗಿದೆ. ಈ ಮುಂದೆ ನೀಡಿರುವ ಉದಾಹರಣೆಯಂತೆ ಎಚ್.ಎಸ್.ಎಸ್. ಡ್ರಿಲ್ ನ ಜಾಗದಲ್ಲಿ ಇಂಡೆಕ್ಸೆಬಲ್ ಡ್ರಿಲ್ ಬಳಸಲಾಗಿದೆ. ಪ್ರಸ್ತುತ ಪ್ರಕ್ರಿಯೆಯಲ್ಲಿ ಕಡಿಮೆ ನಿಯತಾಂಕಗಳಿರುವ ಎಚ್.ಎಸ್.ಎಸ್. ಡ್ರಿಲ್ ಬಳಸಲಾಗುತ್ತಿತ್ತು. ಇದರಿಂದಾಗಿ ಟೂಲ್ ನ ಬಾಳಿಕೆಯೂ ಕಡಿಮೆ ಸಿಗುತ್ತದೆ. ಈ ರೀತಿಯ ಡ್ರಿಲ್ಲಿಂಗ್ ಸಿ.ಎನ್.ಸಿ. ಲೇಥ್ ಮಶಿನ್ ನಲ್ಲಿ ಮಾಡಲಾಗುತ್ತದೆ. ಹೊಸ ಮತ್ತು ಹಳೆಯ ರೀತಿಗೋಸ್ಕರ ಪ್ರಕ್ರಿಯೆ ನಿಯತಾಂಕಗಳ ವಿವರಗಳನ್ನು ಕೋಷ್ಟಕ ಕ್ರ. 3 ರಲ್ಲಿ ನೀಡಲಾಗಿದೆ.
ಯಂತ್ರಭಾಗ : ಹೈಡ್ರಾಲಿಕ್ ಯಂತ್ರಭಾಗಗಳ ರಿಂಗ್
ಆಪರೇಶನ್ : ಡ್ರಿಲ್ಲಿಂಗ್
ಮಟೀರಿಯಲ್ : C45 (ಕಠಿಣತೆ 180 ರಿಂದ 220 BHN)
ಮಶಿನ್ : ಸಿ.ಎನ್.ಸಿ. ಲೇಥ್
ಇಂಡೆಕ್ಸೆಬಲ್ ಡ್ರಿಲ್ ಮೂಲಕ ಪ್ರಕ್ರಿಯೆ ಮಾಡಿದ್ದರಿಂದ ಗ್ರಾಹಕರಿಗೆ ಈ ಕೆಳಗಿನ ಲಾಭಗಳಾಗಿವೆ.
1. ಉತ್ಪಾದಕತೆ ಶೇಕಡಾ 100 ರಷ್ಟು ಹೆಚ್ಚಾಯಿತು.
2. ಟೂಲಿಂಗ್ ನ ಖರ್ಚು ಶೇಕಡಾ 87 ರಷ್ಟು ಕಡಿಮೆಯಾಯಿತು.
3. ಸೈಕಲ್ ಟೈಮ್ ಕಡಿಮೆಯಾಯಿತು. (120 ಸೆಕಂಡುಗಳಿಂದ 30 ಸೆಕಂಡುಗಳಷ್ಟು ಕಡಿಮೆಯಾಯಿತು)
4. ರಂಧ್ರಗಳ ಗುಣಮಟ್ಟವು ಸುಧಾರಿಸಿತು ಮತ್ತು ನಿರಂತರತೆಯೂ ಲಭಿಸಿತು.
ಹೊಸ ಪ್ರಕ್ರಿಯೆಯಲ್ಲಿ ಬದಲಾವಣೆಗಳನ್ನು ಮಾಡಿ ಗ್ರಾಹಕರಿಗೆ ಹೆಚ್ಚು ಪ್ರಮಾಣದಲ್ಲಿ ಲಾಭವುಂಟಾಯಿತು. ಪ್ರಕೃತ ಒಂದು ಶಿಷ್ಟ್ ನಲ್ಲಿ 200 ಯಂತ್ರಭಾಗಗಳ ಹೋಲಿಕೆಯಲ್ಲಿ 900 ಯಂತ್ರಭಾಗಗಳನ್ನು ತಯಾರಿಸಲಾಗುತ್ತದೆ.