ಗ್ರಾನೈಟ್ ಇದೊಂದು ಅತ್ಯಂತ ಕಠಿಣವಾದ, ಸ್ಫಟಿಕದಂತೆ ಇರುವ, ನೈಸರ್ಗಿಕವಾಗಿ ಜ್ವಾಲಾಮುಖಿಯಿಂದ ಉದ್ಭವಿಸಿರುವ ಬಂಡೆಗಳಿಂದ ತಯಾರಿಸಿರುವ ಕಲ್ಲು. ಇದು ಪ್ರಾಮುಖ್ಯವಾಗಿ ಕ್ವಾರ್ಟ್ಜ್ ಮತ್ತು ಫೆಲ್ ಸ್ಪಾರ್ ಇವುಗಳಿಂದ ತಯಾರಾಗಿರುತ್ತದೆ. ಮಾಪನ ಶಾಸ್ತ್ರಕ್ಕೆ ಸಂಬಂಧಪಟ್ಟ (ಮೆಟ್ರಾಲಾಜಿ) ಕೆಲಸಗಳಲ್ಲಿ ಈ ಕಲ್ಲಿನ ಯಾವ ರೀತಿಯನ್ನು ಬಳಸಬೇಕು ಎಂಬುದನ್ನು ನಿರ್ಧರಿಸಲಾಗಿಲ್ಲ. ಈ ಕಲ್ಲಿನಲ್ಲಿ ಅನೇಕ ರೀತಿಯ ಖನಿಜಗಳು ಸೇರಿರುವುದರಿಂದ ಅದು ವಿವಿಧ ಬಣ್ಣಗಳಲ್ಲಿ ಕಂಡುಬರುತ್ತದೆ. ಅದರ ಘನತೆಯೂ ವಿಭಿನ್ನವಾಗಿ ಇರುವುದರಿಂದ ಮಾಪನದ ಕೆಲಸದಲ್ಲಿ ಈ ಕಲ್ಲಿನ ಉಪಯುಕ್ತತೆಯು ಅದರಲ್ಲಿ ಪರಿಣಾಮವನ್ನು ಬೀರುತ್ತದೆ. ಕಪ್ಪು ಬಣ್ಣದ ಕಲ್ಲು ಎಲ್ಲಕ್ಕಿಂತಲೂ ಉಚ್ಚಮಟ್ಟದ್ದು ಎಂದು ಪರಿಗಣಿಸಲಾಗುತ್ತಿದೆ. ಆದರೂ ಬೂದು ಬಣ್ಣದ ಮತ್ತು ಹಸಿರು ಬಣ್ಣದ ಕಲ್ಲುಗಳೂ ಅಷ್ಟೇ ಉಚ್ಚಮಟ್ಟದ್ದಾಗಿರುತ್ತವೆ. ಈ ಕಲ್ಲುಗಳನ್ನು ಬಳಸುವ ಮುಂಚೆ ಕಪ್ಪು ಬಣ್ಣದ ಹೊರತಾಗಿ ಇನ್ನಿತರ ಕಲ್ಲುಗಳ ಪರೀಕ್ಷೆಯನ್ನು ಮಾಡಿ ಅವುಗಳ ಗುಣಮಟ್ಟದ ತಪಾಸಣೆಯನ್ನು ಮಾಡಬೇಕಾಗುತ್ತದೆ. ಸರ್ಫೇಸ್ ಪ್ಲೇಟ್, ಪ್ರಿಜಮ್ ಇಂತಹ ಮಾಪನದ ಕುರಿತಾದ ರೆಫರನ್ಸ್ ಉಪಕರಣಗಳಲ್ಲಿ ಮತ್ತು ಮಾಪನಕ್ಕೆ ಸಹಾಯಕವಾದ ಇನ್ನಿತರ ಸಾಮಗ್ರಿಗಳಲ್ಲಿ ಗ್ರಾನೈಟ್ ಬಳಕೆ ಒಂದು ಆದರ್ಶವಾದ ಅಂಶವಾಗಿದೆ.
ಪ್ರಿಸೈಜ್ ಸರ್ಫೇಸ್ ನ ಮಾಪನಕ್ಕೋಸ್ಕರ ರೆಫರನ್ಸ್ ಗೋಸ್ಕರ ಸ್ಟೀಲ್ ಅಥವಾ ಕಾಸ್ಟ್ ಆಯರ್ನ್ ಗಿಂತ ಗ್ರಾನೈಟ್ ಹೆಚ್ಚು ಒಳ್ಳೆಯದಾಗಿರುತ್ತದೆ. ಅದರ ಕಾರಣಗಳನ್ನು ಈ ಕೆಳಗೆ ನೀಡಲಾಗಿದೆ.
•ರಾಸಾಯನಿಕ ಪ್ರತಿಕಾರ ಶಕ್ತಿಯಿಂದಾಗಿ ಅದಕ್ಕೆ ತುಕ್ಕು ಹಿಡಿಯುವುದಿಲ್ಲ ಅಥವಾ ಅದರ ಸವೆತವೂ ಆಗುವುದಿಲ್ಲ. ಇದರಿಂದಾಗಿ ಅದರ ನಿರ್ವಹಣೆಯೂ ತುಂಬಾ ಸುಲಭ.
•ಉಷ್ಣತೆಯ ಪ್ರಸಾರದ ಗುಣಾಂಕಗಳು (ಹೀಟ್ ಎಕ್ಸ್ ಪಾನ್ಶನ್ ಕೊ-ಇಫಿಶಿಯಂಟ್) ಕಡಿಮೆ ಇರುವುದರಿಂದ ಗ್ರೆನೈಟ್ ಅಂಕುಡೊಂಕಾಗುವುದಿಲ್ಲ. (ವಾರ್ಪ್). ಗ್ರೆನೈಟ್ ಮತ್ತು ಕಾಸ್ಟ್ ಆಯರ್ನ್ ನ ರೇಖೀಯ ಉಷ್ಣತೆಯ ಪ್ರಸಾರದ ಗುಣಾಂಕ (CLTE).
ಕಪ್ಪು : 2.2 K-1
ಕಡು ಹಸಿರು : 3.3 K-1
ಕಾಸ್ಟ್ ಆಯರ್ನ್ : 10-12.5 K-1
•ಬಾಳಿಕೆಯು ತುಂಬಾ ಹೆಚ್ಚಾಗಿರುತ್ತದೆ.
•ಸರ್ಫೇಸ್ ನುಣುಪಾಗಿ ಇರುವುದರಿಂದ ಕಾರ್ಯವಸ್ತುವಿನ ಚಟುವಟಿಕೆಯು ಸಹಜವಾಗಿ ಆಗುತ್ತದೆ.
•ನಾನ್-ಮೆಗ್ನೆಟಿಕ್ ಇರುತ್ತದೆ.
•ಇದರ ಪೊರೋಸಿಟಿ ಕಡಿಮೆ ಇರುತ್ತದೆ. (ಕೇವಲ ಮಾಪನದ ಶ್ರೇಣಿಯಲ್ಲಿ) ಆದ್ದರಿಂದ ಸಹಜವಾಗಿ ಅಂಕುಡೊಂಕಾಗುವುದಿಲ್ಲ, ಅಲ್ಲದೇ ಅದರಲ್ಲಿ ಯಾವುದೇ ರೀತಿಯ ಕಲೆಗಳು ಉಂಟಾಗುವುದಿಲ್ಲ.
•ಕಾಸ್ಟ್ ಆಯರ್ನ್ ಗಿಂತ ಇದರ ಕಂಪನ ಪ್ರತಿಕಾರ ಶಕ್ತಿಯು ಹೆಚ್ಚಾಗಿದೆ.
•ಹೆಚ್ಚು ನಿಖರತೆಯಿಂದ ಫಿನಿಶ್ ಮಾಡಬಹುದಾಗಿದೆ.
•ಬಳಸುವಾಗ ಅದರ ಸರ್ಫೇಸ್ ನಲ್ಲಿ ಯಾವುದೇ ರೀತಿಯ ಗೀಚುಗಳು ಉಂಟಾದಲ್ಲಿ ಅದರಲ್ಲಿ ಯಾವುದೇ ರೀತಿಯ ಉಬ್ಬುಗಳು ಕಂಡುಬರುವುದಿಲ್ಲ. ಒಂದು ವೇಳೆ ಸ್ಟೀಲ್ ನಲ್ಲಿ ಗೆರೆಗಳು ಉಂಟಾದಲ್ಲಿ ಬದಿಯಲ್ಲಿರುವ ಮಟೀರಿಯಲ್ ಹೊರಗೆ ಎಸೆಯಲ್ಪಡುತ್ತದೆ ಮತ್ತು ಉಬ್ಬು ತಯಾರಾಗುತ್ತದೆ. ಒಂದು ವೇಳೆ ಈ ಉಬ್ಬು ತುಂಬಾ ದೊಡ್ಡದಾಗಿದ್ದರೆ ಸ್ಟೀಲ್ ಪ್ಲೇಟ್ ನ ಸರ್ಫೇಸ್ ಮತ್ತೆ ಫಿನಿಶ್ ಮಾಡಬೇಕಾಗುತ್ತದೆ.
•ಗ್ರಾನೈಟ್ ನ ನಿರ್ಮಾಣದಲ್ಲಿ ದೊಡ್ಡ ಕಣಗಳಿರುತ್ತದೆ. ಇಂತಹ ಕಣಗಳು ತುಂಡಾಗುತ್ತವೆ ಮತ್ತು ಹೊರಗೆ ಎಸೆಯಲ್ಪಡುತ್ತವೆ. ಸಮತಟ್ಟುತನದಲ್ಲಿ (ಫ್ಲ್ಯಾಟ್ ನೆಸ್) ಇದರಿಂದಾಗಿ ಪರಿಣಾಮವು ಉಂಟಾಗುವುದಿಲ್ಲ. (ಕಾರ್ಯವಸ್ತುವಿನ ಹೋಲಿಕೆಯಲ್ಲಿ ಗೀಚುಗಳ ಆಕಾರ ಚಿಕ್ಕದಾಗಿದ್ದಲ್ಲಿ)
•ಕಾಸ್ಟ್ ಆಯರ್ನ್ ನ ಅರ್ಧ ಬೆಲೆಯಲ್ಲಿ ಲಭ್ಯವಿದೆ.
•ಕಾಸ್ಟ್ ಆಯರ್ನ್ ಬಳಸುವಾಗ ಆಕಾರವನ್ನು ಸೀಮಿತಗೊಳಿಸಬಲ್ಲದು. ಕಾರಣ ಯಾವುದೇ ಕೆಲಸಕ್ಕೋಸ್ಕರ ಕಾಸ್ಟ್ ಆಯರ್ನ್, ಎರಕ ಹಾಕುವಾಗ ಆಕಾರದ ಮತ್ತು ಫಿನಿಶಿಂಗ್ ಕ್ಕೋಸ್ಕರ ಲಾಭಕಾರಿಯಾಗಿದೆ. ಅದರಲ್ಲಿ ಮಿತಿಗಳಿರುತ್ತವೆ.
ಗ್ರಾನೈಟ್ ಉತ್ಪಾದನೆಗಳ ಅಭಿವೃದ್ಧಿಯಲ್ಲಿರುವ ಸವಾಲುಗಳು
ಈ ಹಿಂದೆ ನಾವು ತಯಾರಿಸುತ್ತಿದ್ದ ಎಲ್ಲ ರೀತಿಯ ಮಾಪನದ ಉಪಕರಣೆಗಳು ಕಾಸ್ಟ್ ಆಯರ್ನ್ ನವುಗಳಾಗಿದ್ದವು. ಈ ಉದ್ಯಮವು ಅಭಿವೃದ್ಧಿಯಾದಂತೆ ಮತ್ತು ನಿಖರವಾದ ಯಂತ್ರಭಾಗಗಳ ಬೇಡಿಕೆಯು ಹೆಚ್ಚಾಯಿತು. ಕಾಸ್ಟ್ ಆಯರ್ನ್ ನಲ್ಲಿ ಉಷ್ಣತೆಯ ಪ್ರಸಾರದ ಗುಣಾಂಕಗಳು ಹೆಚ್ಚಾಗಿರುವುದರಿಂದ ಉಂಟಾಗುವ ಹಾನಿಯು ಗಮನಕ್ಕೆ ಬರಲಾರಂಭಿಸಿತು. ಗ್ರಾಹಕರಿಗೆ ಅತ್ಯಂತ ಸೂಕ್ಷ್ಮವಾದ ನಿಖರತೆಯ ಬೇಕಾಗಿತ್ತು. ಅದಕ್ಕೋಸ್ಕರವೇ ನಾವು ಗ್ರಾನೈಟ್ ಬಳಸಲು ಪ್ರಾರಂಭಿಸಿದೆವು. ಉಚ್ಚಮಟ್ಟದ ನಿಖರತೆ ಇರುವ ಗ್ರಾನೈಟ್, ಸರ್ಫೇಸ್ ಪ್ಲೇಟ್ ನಿಂದ ನಿಯಂತ್ರಿಸಲ್ಪಡುವ ಹವಾಮಾನದಲ್ಲಿ ಉಪಕರಣಗಳು ಮತ್ತು ಗೇಜ್ ಇವುಗಳ ಕ್ಯಾಲಿಬ್ರೇಶನ್ ಗೋಸ್ಕರ ಸರ್ವೋತ್ಕೃಷ್ಟ ಎಂದು ತಿಳಿಯಲಾಗಿದೆ.
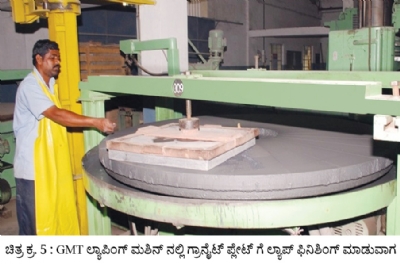
80 ರ ದಶಕದ ಪ್ರಾರಂಭದಲ್ಲಿ ಪ್ರಗತಿಪರ ದೇಶಗಳಲ್ಲಿ ಗ್ರಾನೈಟ್ ಬಳಸಲಾಗುತ್ತಿತ್ತು. ಕಾರಣ ಗ್ರಾನೈಟ್ ನ ಉಷ್ಣತೆಯ ಪ್ರಸಾರದ ಗುಣಾಂಕಗಳು ಕಾಸ್ಟ್ ಆಯರ್ನ್ ಗಿಂತ ಕಡಿಮೆ ಇರುವುದರಿಂದ ಅದು ಒಂದು ಸ್ಟೇಬಲ್ ಮಟೀರಿಯಲ್ ಎಂಬುದಾಗಿ ತಿಳಿಯಲಾಗಿತ್ತು ಮತ್ತು ಅದಕ್ಕೆ ತಗಲುವ ಖರ್ಚು ಕೂಡಾ ತುಂಬಾ ಕಡಿಮೆ ಇತ್ತು. ದಕ್ಷಿಣ ಭಾರತದ ಐತಿಹಾಸಿಕ ಪರಿಸರವು (ಡೆಕ್ಕನ್) ಜಗತ್ತಿನಲ್ಲಿ ಅತ್ಯಂತ ಉಟ್ಟಮಟ್ಟದ ಗ್ರಾನೈಟ್ ವಿಪುಲವಾಗಿ ಸಿಗುವಂತಹ ಪ್ರಸಿದ್ಧ ಮೂಲವಾಗಿದೆ. ಗಿಂಡಿ ಮಶಿನ್ ಟೂಲ್ಸ್ ಇವರು (GMT) ಒಂದು ಗಣಿಯನ್ನು ಖರೀದಿಸುವ ವ್ಯವಸ್ಥೆಯನ್ನು ಮಾಡಿದರು. ಬೆಂಗಳೂರಿನ ಸಮೀಪದ ಹೊಸೂರಿನಲ್ಲಿರುವ SIPCOT ಔದ್ಯೋಗಿಕ ಪರಿಸರದಲ್ಲಿ ಕಾರ್ಖಾನೆಯನ್ನು ನಿರ್ಮಿಸಲು ಬಾಡಿಗೆಯಲ್ಲಿ ಜಮೀನನ್ನು ಖರೀದಿಸಿದರು. ಗಣಿಯಿಂದ ಕಲ್ಲುಗಳನ್ನು ತೆಗೆಯುವುದು ಮಾತ್ರ ಒಂದು ಮಹತ್ಕಾರ್ಯವಾಗಿದೆ. ಈ ಗಣಿಗಳು ದುರ್ಗಮ, ಗುಡ್ಡಬೆಟ್ಟಗಳ ಪರಿಸರದಲ್ಲಿ ಇದ್ದವು. ಅಲ್ಲದೇ ಅಲ್ಲಿ ಕಾಡು ಪ್ರಾಣಿಗಳು ಮತ್ತು ಕಳ್ಳರ ಕಾಟವೂ ಇತ್ತು. ಉತ್ಖನನ ಮಾಡಲಾಗುವ ಕಲ್ಲು ಮೆಟ್ರಾಲಾಜಿ ಗ್ರೇಡ್ ನಲ್ಲಿ ಇದೆಯೇ ಇಲ್ಲವೇ ಎಂಬುದನ್ನು ದೃಢೀಕರಿಸಲು ಮತ್ತು ನಮ್ಮ ಸಿಬ್ಬಂಧಿಗಳು ಕಚ್ಚಾ ಕಲ್ಲುಗಳನ್ನು ಪರಿಶೀಲಿಸಲು ಗಣಿಯೆಡೆಗೆ ಆಗಾಗ ಹೋಗಬೇಕಾಗುತ್ತಿತ್ತು. ಸಾರ್ವಜನಿಕ ಸಾರಿಗೆ ವ್ಯವಸ್ಥೆಯ ಅಭಾವದಿಂದಾಗಿ ಅವರಿಗೆ ಅನೇಕ ರೀತಿಯ ಅಡಚಣೆಗಳನ್ನು ಎದುರಿಸಬೇಕಾಗುತ್ತಿತ್ತು. ಒಮ್ಮೊಮ್ಮೆ ಹತ್ತಿರದಲ್ಲಿರುವ ಬಸ್ ಸ್ಟಾಪ್ ನಿಂದ ಗಣಿಯ ತನಕ ತಲುಪಲು ಹಲವಾರು ಕಿಲೋಮೀಟರ್ ನಡೆದುಕೊಂಡು ಹೋಗಬೇಕಾಗುತ್ತಿತ್ತು. ಅದರ ನಂತರ ಇನ್ನಷ್ಟು ತೊಂದರೆಗಳನ್ನು ಎದುರಿಸಬೇಕಾಯಿತು. ಕಟ್ಟಡಗಳ ನಿರ್ಮಾಣದಲ್ಲಿ ಗ್ರಾನೈಟ್ ನ ಮೌಲ್ಯವನ್ನು ಗಮನಿಸಿ ರಾಜ್ಯ ಸರ್ಕಾರವು ಎಲ್ಲ ಗಣಿಗಳನ್ನು ವಶಪಡಿಸಿಕೊಂಡಿತು. ಇದರಿಂದಾಗಿ ಗ್ರಾನೈಟ್ ನ ಲಭ್ಯತೆಯು ಇನ್ನಷ್ಟು ಬಿಕ್ಕಟ್ಟಿನಲ್ಲಿ ಸಿಲುಕಿತು.
80 ರ ದಶಕದ ಪ್ರಾರಂಭದಲ್ಲಿ ಗ್ರಾನೈಟ್ ಕತ್ತರಿಸಲು ಮಾಡಲು ಕೆಲಸಗಾರರು ಸುತ್ತಿಗೆ ಮತ್ತು ಕಬ್ಬಿಣದ ಉಳಿಯನ್ನು ಬಳಸುತ್ತಿದ್ದರು. ಗ್ರಾನೈಟ್ ನಲ್ಲಿ ಕುಳಿಗಳನ್ನು ಮಾಡುತ್ತಾ ಅದರಲ್ಲಿ ಮರದ ಬೆಣೆಯನ್ನು ಹಾಕಿ ನೀರು ಸುರಿಯುತ್ತಿದ್ದರು. ಸ್ವಲ್ಪ ಸಮಯದ ನಂತರ ಆ ಮರದ ಬೆಣೆಯು ಉಬ್ಬುತ್ತಿತ್ತು. ಇದರಿಂದಾಗಿ ಗ್ರಾನೈಟ್ ಒಡೆಯುತ್ತಿತ್ತು. ಹಲವಾರು ರೀತಿಯ ಸ್ಫೋಟಕಗಳನ್ನು ಉಪಯೋಗಿಸಿ ಸಾಲಾಗಿ ಕುಳಿಗಳನ್ನು ಮಾಡುವ ರೀತಿ ಕೂಡಾ, ಬಂಡೆಗಳಿಂದ ಕಲ್ಲುಗಳನ್ನು ಕತ್ತರಿಸುವ ಒಂದು ಉಪಾಯವಾಗಿತ್ತು. ಆದರೆ ಈ ರೀತಿಯಿಂದಾಗಿ ಕಲ್ಲುಗಳ ಒಳಭಾಗದಲ್ಲಿ ಸೀಳುಗಳು ಉಂಟಾಗುತ್ತಿದ್ದವು. ಈ ಸೀಳುಗಳು ಪ್ರಾರಂಭದಲ್ಲಿ ಕಂಡುಬರದಿದ್ದರೂ ಫಿನಿಶಿಂಗ್ ಮಾಡುವಾಗ ಕಂಡುಬರುತ್ತಿದ್ದವು. ಇದರಿಂದಾಗಿ ತಯಾರಿಸಿರುವ ಪ್ಲೇಟ್ ನ್ನು ತಿರಸ್ಕರಿಸಲಾಗುತ್ತಿತ್ತು. ಇದು ಮಾತ್ರ ಒಂದು ಬಹು ದೊಡ್ಡ ಸಮಸ್ಯೆಯೇ ಆಗಿತ್ತು. ಇದರಿಂದ ಅಂತಿಮವಾಗಿ ಮಾರಾಟದ ಬೆಲೆಯೂ ಹೆಚ್ಚುತ್ತಿತ್ತು.
ಅನೇಕ ರೀತಿಯ ಪರೀಕ್ಷೆಗಳನ್ನು ಮಾಡಿದ ನಂತರ ಡೈಮಂಡ್ ಸಾ (ವಜ್ರದ ಕರಗಸ) ಬಳಸುವುದನ್ನು ನಿರ್ಧರಿಸಿದೆವು. ಇದರಲ್ಲಿ ಕಲ್ಲು ಒಡೆಯುವುದಿಲ್ಲ ಮತ್ತು ಅದರಿಂದಾಗಿ ನಷ್ಟದ ಪ್ರಮಾಣವು ಕಡಿಮೆಯಾಗುತ್ತದೆ. ತುಂಬಾ ಆಳದ ತನಕ ಕೆಲಸ ಮಾಡುವುದಾದಲ್ಲಿ ವಾಯರ್ ಕಟಿಂಗ್ ಗೆ ಪ್ರಾಧಾನ್ಯತೆಯನ್ನು ನೀಡಲಾಗುತ್ತದೆ.
ಗ್ರಾನೈಟ್ ಖರೀದಿಸಿದ ನಂತರ ಅದಕ್ಕೆ ಲ್ಯಾಪ್ ಮಾಡಲು ಕೈಯಿಂದ ಲ್ಯಾಪಿಂಗ್ ಮಾಡಲು ನುರಿತ ಕೆಲಸಗಾರರ ಒಂದು ತಂಡವನ್ನು ಸಿದ್ಧಪಡಿಸಬೇಕಾಗುತ್ತದೆ. ಇದು ತುಂಬಾ ಕಠಿಣವಾದ ಮತ್ತು ಕಠೋರ ಶ್ರಮದ ಕೆಲಸವಾಗಿದೆ. ಪ್ಲೇಟ್ ನ ಸರ್ಫೇಸ್ ಗೆ ಲ್ಯಾಪಿಂಗ್ ಮಾಡಲು ದಿನವಿಡಿ ಕೆಲಸ ಮಾಡಬೇಕಾಗುತ್ತಿತ್ತು. ಪ್ಲೇಟ್ ಒಣಗುವ ತನಕ ಕಾಯಬೇಕಾಗುತ್ತಿತ್ತು. ಪ್ರತಿಯೊಂದು ಹಂತದಲ್ಲಿ ತಪಾಸಣೆಯನ್ನು ಮಾಡುವ ಮುಂಚೆ ಸರ್ಫೇಸ್ ಹವಾಮಾನದ ಉಷ್ಣಾಂಶಕ್ಕೆ ಸರಿಹೊಂದಿಸಬೇಕಾಗುತ್ತದೆ. ಕೆಲಸವನ್ನು ನಿರ್ವಹಿಸುವಾಗ ಅನೇಕ ರೀತಿಯ ಅಡಚಣೆಗಳನ್ನು ಎದುರಿಸಬೇಕಾಗುತ್ತಿತ್ತು. ಇಂದಿನ ದಿನಗಳಲ್ಲಿ ಲ್ಯಾಪಿಂಗ್ ಮಶಿನ್ ಬಳಸಿ 5 ಮೈಕ್ರೋಮೀಟರ್ ತನಕದ ಸಮತಟ್ಟನ್ನು ಪಡೆಯಲಾಗುತ್ತದೆ. ಆದರೆ ಅದಕ್ಕಿಂತ ಹೆಚ್ಚು ನಿಖರತೆಯು ಮಾತ್ರ ಕೇವಲ ಕೈಯಿಂದ ಕೆಲಸ ಮಾಡಿಯೇ ಲಭಿಸಬಲ್ಲದು.
ಈ ರೀತಿಯಲ್ಲಿ ಹೈಟೆಕ್ ಅಪ್ಲಿಕೇಶನ್ ಗೋಸ್ಕರ ಬೇಕಾಗುವ ಅತ್ಯಂತ ಉಚ್ಚಮಟ್ಟದ ನಿಖರತೆ ಇರುವ ಉತ್ಪಾದನೆಗಳನ್ನು ಮಾನವನ ಕೈಯಿಂದ ‘ನೋ ಟೆಕ್’ ನೈಸರ್ಗಿಕವಾದ ಶಕ್ತಿ ಮತ್ತು ಸೂಕ್ಷ್ಮತೆಯನ್ನು ಬಳಸಿ ಅಭಿವೃದ್ಧಿ ಪಡಿಸಲಾಯಿತು.
ವಿಶ್ವಾಸಾರ್ಹವಾದ ತಪಾಸಣೆಯ ಪ್ರಯೋಗ ಶಾಲೆಯನ್ನು ನಿರ್ಮಿಸುವುದೇ ಮುಂದಿನ ಗುರಿಯಾಗಿತ್ತು. 80 ರ ದಶಕದಲ್ಲಿ ಈ ಪ್ರಕ್ರಿಯೆಯು ನಡೆಯುತ್ತಿತ್ತು, ಎಂಬುದನ್ನು ಗಮನದಲ್ಲಿಡಬೇಕು. ಪ್ರಯೋಗ ಶಾಲೆಗೆ ಬೇಕಾಗುವ ಎಲ್ಲ ರೀತಿಯ ನಿರ್ದೋಷತೆಯುಳ್ಳ ಸಾಮಗ್ರಿಗಳನ್ನು ಆಮದು ಮಾಡಬೇಕಾಗುತ್ತಿತ್ತು. ಇದಕ್ಕೆ ಆಮದು ಶುಲ್ಕ 300% ಇತ್ತು. ಇದರಿಂದಾಗಿ ಹಣಕಾಸಿನ ಬಜೆಟ್ ಕುಸಿಯುತ್ತಿತ್ತು.
ಪ್ರಿಸಿಜನ್ ಗ್ರಾನೈಟ್ ಉತ್ಪಾದನೆಗಳನ್ನು ತಯಾರಿಸಲು ಗಣಿಯಲ್ಲಿ ನಿರ್ದೋಷವಾದ ಕಲ್ಲುಗಳನ್ನು ಆಯ್ಕೆ ಮಾಡಬೇಕಾಗುತ್ತಿತ್ತು. ಅಲ್ಲದೇ ಈ ಕಲ್ಲುಗಳನ್ನು ಗಣಿಯಲ್ಲಿ ಕತ್ತರಿಸಿ ಹೊರಗೆ ತೆಗೆಯುವುದು, ಅವುಗಳಿಗೆ ಲ್ಯಾಪಿಂಗ್, ಡ್ರಿಲ್ಲಿಂಗ್, ಇನ್ಸರ್ಟ್ ಬಾಂಡಿಂಗ್, ಪ್ಯಾಕಿಂಗ್ ಮತ್ತು ಡಿಸ್ಪೇಚ್ ಮಾಡುವ ತನಕ ಅನೇಕ ಸಮಸ್ಯೆಗಳನ್ನು ಎದುರಿಸಬೇಕಾಗುತ್ತಿತ್ತು. ಅನೇಕ ಬಾರಿ ನಮ್ಮ ಉತ್ಪಾದನೆಯನ್ನು ಅನುಸರಿಸಿ ಮಶಿನ್ ಗಳನ್ನೂ ನಿರ್ಮಿಸಬೇಕಾಗುತ್ತಿತ್ತು. ಉದಾಹರಣೆ, ಪ್ರಾರಂಭದಲ್ಲಿ ನಾವು ಗ್ರಾನೈಟ್ ನಲ್ಲಿ ಇನ್ಸರ್ಟ್ ಗೋಸ್ಕರ ಡ್ರಿಲ್ ಮಾಡುವಾಗ ರೇಡಿಯಲ್ ಡ್ರಿಲ್ಲಿಂಗ್ ಮಶಿನ್ ಬಳಸುತ್ತಿದ್ದೆವು. ಕಾಲಕ್ರಮೇಣ ಗ್ರಾಹಕರು ಥ್ರೆಡೆಡ್ ಇನ್ಸರ್ಟ್ ನ ನಿಖರತೆಯು ಹೆಚ್ಚು ಇರಬೇಕು, ಎಂಬ ಬೇಡಿಕೆಯನ್ನು ನೀಡಲಾರಂಭಿಸಿದರು. ನಾವು ಡ್ರಿಲ್ಲಿಂಗ್ ಗೋಸ್ಕರ ಕೂಲಂಟ್ ನ ಬದಲಾಗಿ ನೀರನ್ನು ಬಳಸುತ್ತಿದ್ದೆವು. ಕೂಲಂಟ್ ಬಳಸಬಲ್ಲ ಮಶಿನ್ ಗಳು ಮಾರುಕಟ್ಟೆಯಲ್ಲಿ ಲಭ್ಯವಿರಲಿಲ್ಲ. ಆದ್ದರಿಂದ ನಾವು ಒಂದು ಗ್ರಾನೈಟ್ ಗ್ಯಾಂಟ್ರಿಯನ್ನು ತಯಾರಿಸಿದೆವು (ಚಿತ್ರ ಕ್ರ. 7). ಅದರಲ್ಲಿ ಎಚ್.ಎಮ್.ಟಿ. ಡ್ರಿಲ್ಲಿಂಗ್ ಹೆಡ್ ಅಳವಡಿಸಿದೆವು. ಈಗ ಇನ್ಸರ್ಟ್ ನಲ್ಲಿ 50 ಮೈಕ್ರೊಮೀಟರ್ ಪಿಚ್ ನಷ್ಟು ನಿಖರತೆಯನ್ನು ಪಡೆಯಬಲ್ಲೆವು. ಹಾಗೆಯೇ ಬೇಡಿಕೆಗಳಿಗೆ ಅನುಸಾರವಾಗಿ ಇದಕ್ಕಿಂತಲೂ ಹೆಚ್ಚು ನಿಖರತೆಯನ್ನು ಪಡೆಯಬಲ್ಲೆವು.
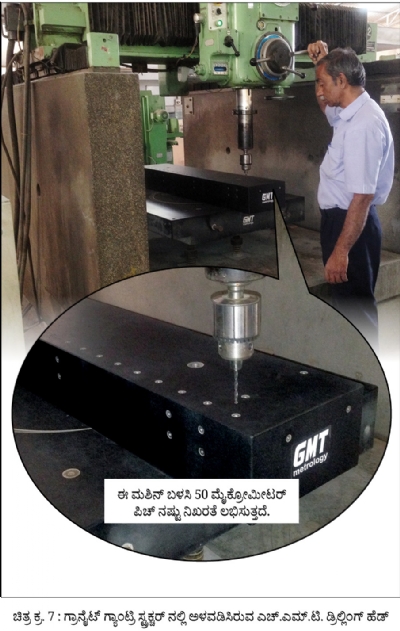
ಹೊಳಪು ಮತ್ತು ಇದರಿಂದಾಗಿ ಮಾಪನದಲ್ಲಿ ಉಂಟಾಗುವ ಸಮಸ್ಯೆಗಳನ್ನು ತಡೆಯಲು ಪ್ರಿಸಿಜನ್ ಗ್ರಾನೈಟ್ ಸರ್ಫೇಸ್ ಎಂದಿಗೂ ಪಾಲಿಶ್ ಮಾಡಲಾಗುವುದಿಲ್ಲ. ನಮ್ಮಲ್ಲಿ ಗ್ರಾನೈಟ್ ಗೋಸ್ಕರ ಈ ಅನೇಕ ಮೂಲಗಳಿವೆ. ಪ್ರತಿಯೊಂದು ಬಾರಿ ನಾವು ಹೊಸ ಹೊಸ ಗಣಿಗಳಲ್ಲಿರುವ ಗ್ರಾನೈಟ್ ಬಳಸುವ ಮುಂಚೆ NABL ಮನ್ನಣೆಯನ್ನು ಪಡೆದಿರುವ ಪ್ರಯೋಗ ಶಾಲೆಯಲ್ಲಿ ಅದರ ಪರೀಕ್ಷೆಯನ್ನು ಮಾಡಿಕೊಳ್ಳುತ್ತೇವೆ. ಇದರ ಪ್ರಾತಿನಿಧಿಕವಾದ ಫಲಿತಾಂಶಗಳನ್ನು ಕೋಷ್ಟಕ ಕ್ರ. 2 ರಲ್ಲಿ ನೀಡಲಾಗಿದೆ.
ಮಾಪನದ ಉಪಕರಣಗಳ ಪರೀಕ್ಷೆ
ಡೈಮೆನ್ಶನಲ್ ಮೆಟ್ರಾಲಾಜಿ ಉಪಕರಣಗಳನ್ನು ಪ್ರಮಾಣೀಕರಿಸಲು ಅನೇಕ ಯಾಂತ್ರಿಕ ಮತ್ತು ಇಲೆಕ್ಟ್ರಾನಿಕ್ ಗೇಜ್ ಗಳಿವೆ. ಪ್ರಾರಂಭದಲ್ಲಿ ನಾವು ಆಪ್ಟಿಕಲ್ ಗೇಜ್ ಕೂಡಾ ಬಳಸುತ್ತಿದ್ದೆವು. ಸ್ಟ್ರೇಟ್ ನೆಸ್ ದೃಢೀಕರಿಸಲು ಆಟೊಕೋಲಿಮೀಟರ್. ಇದಕ್ಕೋಸ್ಕರ ತಪಾಸಣೆಯನ್ನು ಮಾಡುವ ವ್ಯಕ್ತಿಯಲ್ಲಿ ಉಚ್ಚ ಗುಣಮಟ್ಟದ ನಿಪುಣತೆ ಇರುವುದೂ ಅತ್ಯಾವಶ್ಯಕವಾಗಿದೆ. 80 ರ ದಶಕದ ಉತ್ತರಾರ್ಧದಲ್ಲಿ ಸಮತಟ್ಟುತನದ ಮಾಪನಕ್ಕೋಸ್ಕರ ಇಲೆಕ್ಟ್ರಾನಿಕ್ ಲೆವಲ್ ಉಪಕರಣಗಳನ್ನು ಬಳಸಲು ಪ್ರಾರಂಭಿಸಲಾಯಿತು. ಅವುಗಳನ್ನು ಅಳವಡಿಸುವುದು ಮತ್ತು ಅವುಗಳನ್ನು ನಿರ್ವಹಿಸುವುದು ಮಾತ್ರ ನಮಗೋಸ್ಕರ ಬಹು ದೊಡ್ಡ ಸಮಸ್ಯೆ ಮತ್ತು ಸವಾಲೂ ಆಗಿತ್ತು. ಕಾರಣ ಅದೇ ಕಾಲಾವಧಿಯಲ್ಲಿ ಭಾರತದಲ್ಲಿ ಯಾರಿಗೂ ಈ ರೀತಿಯ ಇಲೆಕ್ಟ್ರಾನಿಕ್ ಉಪಕರಣಗಳ ಕುರಿತು ಮಾಹಿತಿ ಇರಲಿಲ್ಲ. ಮ್ಯಾನ್ಯುವಲ್ ತಪಾಸಣೆಯಲ್ಲಿ ಪ್ಲೇಟ್ ನ ಸರ್ಫೇಸ್ ನಲ್ಲಿ ಪೆನ್ಸಿಲ್ ನಿಂದ ಚೌಕಟ್ಟುಗಳನ್ನು (ಗ್ರೀಡ್) ಬರೆಯಬೇಕಾಗುತ್ತಿತ್ತು. ನಂತರ ಅವುಗಳ ಪ್ರತಿಯೊಂದು ಭಾಗದಿಂದ ಸ್ಪಿರಿಟ್ ಲೆವರ್ ಜಾಗ್ರತೆಯಿಂದ ಸರಿಸಿ ಲೆವಲ್ ನ ಕೋಷ್ಟಕವನ್ನು (ಕೋಷ್ಟಕ ಕ್ರ. 1) ಕೈಯಿಂದಲೇ ತಯಾರಿಸಬೇಕಾಗುತ್ತಿತ್ತು.
ಗ್ರಾಹಕರ ಬೇಡಿಕೆಗಳನ್ನು ವಿಶ್ಲೇಷಿಸಲು ಟೆಕ್ನೋ-ಕಮರ್ಶಿಯಲ್ ಸವಾಲುಗಳು
ಉದಾಹರಣೆ 1
ಒಬ್ಬ ಗ್ರಾಹಕರಿಗೆ ನಾವು 12 ಮೀಟರ್ ಉದ್ದದ T ಕಚ್ಚು (ಸ್ಲಾಟ್) ಇರುವ 12 ಮೀಟರ್ X 1.5 ಮೀಟರ್ ಆಕಾರದ ಒಂದು ಪ್ಲೇಟ್ ತಯಾರಿಸಿದೆವು. T ಕಚ್ಚಿನ ನೇರತನವು 150 ಮೈಕ್ರೊಮೀಟರ್/ 12 ಮೀಟರ್ ಉದ್ದಕ್ಕೋಸ್ಕರ ನೀಡುವುದನ್ನು ಒಪ್ಪಿದ್ದೆವು. ಅದನ್ನು 80 ಮೈಕ್ರೋಮೀಟರ್ ನಷ್ಟು ನೀಡುವುದು ನಮಗೆ ಸಾಧ್ಯವಾಯಿತು. T ಕಚ್ಚು ಇನ್ಸರ್ಟ್ ನ ಚಿತ್ರವನ್ನು ತಯಾರಿಸಲು ಸಂದರ್ಭಕ್ಕೋಸ್ಕರ ಪ್ಲೇಟ್ ನ ಮೇಲ್ಭಾಗದ ಸರ್ಫೇಸ್ ನಿಂದ 100 ಮಿ.ಮೀ. ದೂರದಲ್ಲಿ ಪ್ಲೇಟ್ ನ ಒಂದು ಬದಿಯಲ್ಲಿ (ಸೈಡ್) ಇನ್ನೊಂದು ತೋಡನ್ನು (ಗ್ರೂವ್) (ಚಿತ್ರ ಕ್ರ. 9) ಕೊರೆದೆವು. ಪ್ಲೇಟ್ ನ ಉದ್ದದಲ್ಲಿ ಈ 100 ಮಿ.ಮೀ. ಸರ್ಫೇಸ್ ನ ನೇರತನದ ನಿಖರತೆಯು 30 ಮೈಕ್ರೋಮೀಟರ್/ 12 ಮೀಟರ್ ಇತ್ತು. T ಕಚ್ಚಿನ ನಿಖರತೆಯು 12 ಮೀಟರ್ ಉದ್ದದಲ್ಲಿ 80 ಮೈಕ್ರೋಮೀಟರ್ (ಚಿತ್ರ ಕ್ರ. 10) ಇತ್ತು.
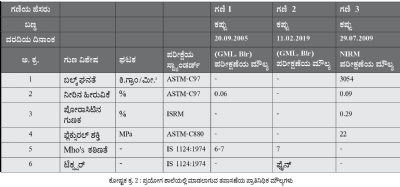
ಇಷ್ಟು ದೊಡ್ಡ ಗಾತ್ರದ ಒಂದು ಕಲ್ಲನ್ನು ಗಣಿಯಿಂದ ಬಂಡೆಯಲ್ಲಿರುವ ಒಳ್ಳೆಯ ಭಾಗದಿಂದ ಕತ್ತರಿಸಿ ಹೊರ ತೆಗೆಯಲು ಮೂರು ಬಾರಿ ಪ್ರಯತ್ನಿಸಿದ ನಂತರ ಯಶಸ್ಸನ್ನು ಪಡೆದೆವು. 30 ಟನ್ ತೂಕವಿರುವ ಪ್ಲೇಟ್ ಗಣಿಯಿಂದ ಕಾರ್ಖಾನೆಗೆ ತರುವುದು, ಅನ್ ಲೋಡ್ ಮಾಡುವುದು, ಯೋಗ್ಯವಾದ ಜಾಗದಲ್ಲಿ ಅದನ್ನು ಇಡುವುದು ಮತ್ತು ಸ್ಪೆಸಿಫಿಕೇಶನ್ ಗೆ ಅನುಸಾರವಾಗಿ ಫಿನಿಶ್ ಮಾಡುವುದು, ಈ ಎಲ್ಲ ಕೆಲಸಗಳು ನಿಜವಾಗಿಯೂ ಸವಾಲುಗಳನ್ನು ಒಡ್ಡುತ್ತಿದ್ದವು. ಇದರಲ್ಲಿ ತಪಾಸಣೆಯ ಪ್ರಕ್ರಿಯೆಗೋಸ್ಕರ ಪ್ಲೇಟ್ ನ ಅಕ್ಕಪಕ್ಕದಲ್ಲಿರುವ ಹವಾಮಾನವನ್ನು ನಿಯಂತ್ರಿಸಬೇಕಾಯಿತು. ಅದರ ನಂತರ ಆ ಪ್ಲೇಟ್ ಪ್ಯಾಕ್ ಮಾಡುವುದು, ಲೋಡ್ ಮಾಡುವುದು ಮತ್ತು ಘಾಟಿ ರಸ್ತೆಗಳ ಮುಖಾಂತರ ಸಾರಿಗೆ ಮಾಡುವುದು, ನಂತರ ಗ್ರಾಹಕರಲ್ಲಿ ಅದನ್ನು ಅನ್ ಲೋಡ್ ಮಾಡುವುದು, ಪ್ಯಾಕಿಂಗ್ ಬಿಡಿಸುವುದು, ಅದರ ಕಾರ್ಯಸಾಮರ್ಥ್ಯವನ್ನು ಸಾಬೀತು ಇಂತಹ ಕೆಲಸಗಳೂ ಅತ್ಯಂತ ಕಠಿಣವಾಗಿದ್ದವು.
ಉದಾಹರಣೆ 2
5 ಅಕ್ಷೀಯ ಮಶಿನ್ ಕ್ಯಾಲಿಬ್ರೇಟ್ ಮಾಡಲು ಸರ್ಫೇಸ್ ಪ್ಲೇಟ್
ಉಚ್ಚಮಟ್ಟದ ನಿಖರತೆ ಇರುವ ಯಂತ್ರಭಾಗಗಳ ಉತ್ಪಾದನೆಯಲ್ಲಿ ಬಹು ಅಕ್ಷೀಯ ಮಶಿನ್ ಬಳಸುವ ಒಲವು ಹೆಚ್ಚಾಗುತ್ತಿದೆ. ಈ ಮಶಿನ್ ಸ್ಥಿರವಾದ ಉಷ್ಣಾಂಶ ಇರುವ ಹವಾಮಾನದಲ್ಲಿ ಇಡಲಾಗುತ್ತದೆ. ಒಂದು ಬಾರಿ ಮಶಿನ್ ಜೋಡಿಸಿ ಗೊತ್ತುಪಡಿಸಿದ ನಂತರ ಉತ್ಪಾದಕರು ಈ ಮಶಿನ್ ಝೀರೋ ಸೆಟಿಂಗ್ ಮಾಡುತ್ತಾರೆ. ಹೆಚ್ಚು ಕಾಲ ಉಪಯೋಗಿಸಿದ ನಂತರ ಬಳಕೆಗಾರರಿಗೆ ಝೀರೋ ಸೆಟಿಂಗ್ ಮತ್ತೆ ಮಾಡಲು ಮಶಿನ್ ಉತ್ಪಾದಕರಲ್ಲಿ ಅವಲಂಬಿಸಿರುವುದು ಆವಶ್ಯಕವಾಗಿರುತ್ತದೆ. ಕಾರಣ ಯಾವುದೇ ಕ್ಯಾಲಿಬ್ರೇಶನ್ ಮಾಡುವ ಪ್ರಯೋಗ ಶಾಲೆಯಲ್ಲಿ 5 ಅಕ್ಷೀಯ ಮಶಿನ್ ಗಳ ಕ್ಯಾಲಿಬ್ರೇಶನ್ ಮಾಡಲು ಇಂದಿಗೂ ಸಿದ್ಧರಾಗಿಲ್ಲ. ಇದು ತುಂಬಾ ದುಬಾರಿಯಾಗಿರುತ್ತದೆ. ಇದರ ಹೊರತಾಗಿ ಅವರಿಗೆ ಉತ್ಪಾದಕರಿಂದ ಸೇವೆ (ಸರ್ವಿಸ್) ಸಿಗುವ ತನಕ ದಾರಿ ನೋಡಬೇಕಾಗುತ್ತದೆ. ಇದರಿಂದಾಗಿ ಖರ್ಚು ಹೆಚ್ಚುತ್ತದೆ.
ಒಬ್ಬ ಗ್ರಾಹಕರು ನಮಗೆ ಕ್ಯಾಲಿಬ್ರೇಶನ್ ಮಾಸ್ಟರ್ (ಚಿತ್ರ ಕ್ರ. 12) ಅಭಿವೃದ್ಧಿ ಪಡಿಸಲು ವಿನಂತಿಸಿದರು ಮತ್ತು ನಾವು ಅದನ್ನು ಯಶಸ್ವಿಯಾಗಿ ಪೂರ್ತಿಗೊಳಿಸಿದೆವು.
ಉದಾಹರಣೆ 3
ಗ್ರಾಹಕರ ಮಾತನ್ನು ನಮ್ಮಲ್ಲಿಗೆ ತಲುಪಿಸುವ ಸರ್ವೋತ್ಕೃಷ್ಟ ರೀತಿ ಅಂದರೆ ಅವರು ನೀಡುವ ಪ್ರಶಸ್ತಿಪತ್ರಗಳು. ನಮ್ಮ ಗ್ರಾಹಕರಾದ ಮೆ. ನ್ಯಾನೋಟ್ಯಾಮ್ ಟೆಕ್ನಾಲಾಜಿಸ್ ಪ್ರೈ.ಲಿ., ಬೆಂಗಳೂರು ಇವರು ನ್ಯಾನೋ ಮಿಲ್ಲಿಂಗ್ ಮಶಿನ್ ಗೋಸ್ಕರ ಗ್ರಾನೈಟ್ ಬೇಸ್ ಮತ್ತು ಗ್ಯಾಂಟ್ರಿ ಖರೀದಿಸಿದ್ದರು. ನ್ಯಾನೋ ಟ್ಯಾಮ್ ನ ಸತೀಶ್ ಕುಮಾರ್ ಇವರು ಹೇಳುತ್ತಾರೆ, “ಗ್ರಾನೈಟ್ ಬೇಸ್ ಮತ್ತು ಕಾಲಮ್ ಇವುಗಳ ಕಠಿಣತೆ (ಸ್ಟಿಫ್ ನೆಸ್) ನಮ್ಮ ಗ್ರಾಹಕರ ಬೇಡಿಕೆಯಂತೆ ಇತ್ತು ಮತ್ತು ಅವರು ಚುನಾಯಿಸಿದ ಗ್ರಾನೈಟ್ ನ ಗುಣಧರ್ಮಗಳು ಕೂಡಾ ಸ್ಟ್ಯಾಂಡರ್ಡ್ ಗಳಿಗೆ ಅನುಸಾರವಾಗಿದ್ದವು. ಆದ್ದರಿಂದಲೇ ಅಮೇರಿಕಾದಲ್ಲಿರುವ ನಮ್ಮ ಗ್ರಾಹಕರು ಕೂಡಾ ಗ್ರಾನೈಟ್ ನ ಕಠಿಣತೆಯ ಕುರಿತು ತುಂಬಾ ಸಂತುಷ್ಟರಾಗಿದ್ದಾರೆ.’’
ಅವಶ್ಯಕವಿರುವ ಫ್ರೇಮ್ ಗೆ ಕಠಿಣತೆ ಇರುವ ಗ್ರಾನೈಟ್ ಬೇಸ್ ಮತ್ತು ಕಾಲಮ್ ಲಭಿಸಿದ್ದರಿಂದ ಗ್ರಾಹಕರು ತುಂಬಾ ಸಂತಸಪಟ್ಟಿದ್ದಾರೆ.
ಗ್ರಾನೈಟ್ ಉತ್ಪಾದನೆಗಳ ಮಾಪನದ ಬಳಕೆ ಮತ್ತು ಮುತುವರ್ಜಿ
1.ಇನ್ಸ್ಟಾಲೇಶನ್ ಮಾಡುವಾಗ ಪ್ಲೇಟ್ ಗೆ ಯೋಗ್ಯವಾದ ಆಧಾರ ನೀಡಿರಿ. ಸರ್ಫೇಸ್ ಪ್ಲೇಟ್ ನ ಕುರಿತು ಲೆವಲಿಂಗ್ ಸ್ಕ್ರೂನೊಂದಿಗೆ ಒಂದು ಸ್ಟ್ಯಾಂಡ್ ಕೂಡಾ ನೀಡಲಾಗುತ್ತದೆ. ಸರ್ಫೇಸ್ ಪ್ಲೇಟ್ ಗೆ ಪ್ಲೇಟ್ ನ ತುದಿಯಿಂದ ಇರುವ ಉದ್ದದ ಶೇಕಡಾ 20 ಕ್ಕಿಂತ ಕಡಿಮೆ, 3 ಬಿಂದುಗಳಲ್ಲಿ ಆಧಾರವನ್ನು ನೀಡುವುದು ಆದರ್ಶವಾದ ರೀತಿಯಾಗಿದೆ. ಅದರಲ್ಲಿ ಎರಡು ಆಧಾರಗಳು ಪ್ಲೇಟ್ ನ ಉದ್ದದ ಬದಿಯಿಂದ ಅಗಲದ ಶೇಕಡಾ 20 ಕ್ಕಿಂತ ಕಡಿಮೆ ಮತ್ತು ಉಳಿದಿರುವ ಆಧಾರವು ಮಧ್ಯದಲ್ಲಿ ಇರಬೇಕು. ಉತ್ಪಾದನೆಯಲ್ಲಿ ಇದೇ ಆಧಾರದ ಬಿಂದುವನ್ನು ಬಳಸಲಾಗುತ್ತದೆ.
2.ಪ್ಲೇಟ್ ಬಳಸುವ ಮುಂಚೆ ಅದರ ಸುತ್ತಮುತ್ತದ ಹವಾಮಾನದಲ್ಲಿರುವ ಉಷ್ಣಾಂಶಕ್ಕೆ ಸರಿಹೊಂದಿಸಲು ಕನಿಷ್ಠ ಅರ್ಧ ಗಂಟೆಯ ಕಾಲಾವಧಿಯನ್ನು ನೀಡಿರಿ. ಉದಾಹರಣೆ, ಟೂಲ್ ರೂಮ್ ನಲ್ಲಿ, ಹವಾ ನಿಯಂತ್ರಣದ ಯಂತ್ರಣೆಯನ್ನು ನಿರಂತರವಾಗಿ ನಡೆಸುವುದು ಸೂಕ್ತವಲ್ಲ. ಒಮ್ಮೊಮ್ಮೆ ಅದನ್ನು ನಿಲ್ಲಿಸಬೇಕಾಗುತ್ತದೆ. ಅದನ್ನು ಪ್ರಾರಂಭಿಸಿದ ನಂತರ ಪ್ಲೇಟ್ ನ ಸಂಪೂರ್ಣ ಕ್ರಾಸ್ ಸೆಕ್ಷನ್ ನಲ್ಲಿ ಒಂದೇ ರೀತಿಯಲ್ಲಿ ಸ್ಥಿರವಾದ ಉಷ್ಣಾಂಶವು ಇರುವುದು ಅತ್ಯಾವಶ್ಯಕವಾಗಿದೆ.
3.ತಯಾರಿಸಿದ ಪ್ರೊಡಕ್ಟ್ ಶುಚಿಯಾಗಿಡಿರಿ. ದಿನಕ್ಕೊಮ್ಮೆ ಕನಿಷ್ಠ ಎರಡು ಬಾರಿ ಸಾಬೂನು ಬಳಸಿ ನೀರಿನಿಂದ ಉಜ್ಜಿಕೊಳ್ಳಿರಿ. ಉಚ್ಚಮಟ್ಟದ ಪರಿಣಾಮ ಲಭಿಸಲು ಶುಚಿ ಮಾಡಿದ ನಂತರ ಒಣಗಲು ಮತ್ತು ಸುತ್ತಮುತ್ತದ ಉಷ್ಣಾಂಶಕ್ಕೆ ಸರಿಹೊಂದಾಣಿಸಲು ಸಾಕಷ್ಟು ಸಮಯವನ್ನು ನೀಡಿರಿ. ಮಾಪನಕ್ಕೆ ಆವಶ್ಯಕವಿರುವ ವಸ್ತುಗಳ ಹೊರತಾಗಿ ಉತ್ಪಾದನೆಯಲ್ಲಿ ಚಹಾ ಕುಡಿಯುವ ಕಪ್ ಅಥವಾ ಇನ್ನಿತರ ಯಾವುದೇ ವಸ್ತುಗಳನ್ನು ಇಡಬೇಡಿರಿ.
4.ಸರ್ಫೇಸ್ ನಲ್ಲಿ ಚೆಕ್ಕೆಗಳು ಉಂಟಾಗುವುದರಿಂದ ನಷ್ಟವುಂಟಾಗುವುದು ಸಮಸ್ಯೆಯು ಸಾಮಾನ್ಯವಾಗಿ ಕಂಡುಬರುತ್ತದೆ. ಪ್ಲೇಟ್ ಬಳಸದೇ ಇರುವಾಗ ಅದರ ಮೇಲ್ಭಾಗವನ್ನು ಮುಚ್ಚಿ ಇಡಬೇಕು. ಪ್ಲೇಟ್ ನ ಸರ್ಫೇಸ್ ನ ಸಂರಕ್ಷಣೆಗೆ GMT ತಯಾರಿಸಿರುವ ಮರದ ಕವಚವನ್ನು ನೀಡಬಲ್ಲದು. ಸಾಮಾನ್ಯವಾಗಿ ಅಬ್ರೆಸಿವ್ ಧೂಳು ಪ್ಲೇಟ್ ನ ಸವೆತಕ್ಕೆ ಎಲ್ಲಕ್ಕಿಂತಲೂ ಪ್ರಮುಖ ಕಾರಣವಾಗಿದೆ.
5.ನಮ್ಮಿಂದ ನೀಡಲಾಗಿರುವ ಪ್ಲೇಟ್ ನಿಯಮಿತವಾಗಿ ಕ್ಯಾಲಿಬ್ರೇಟ್ ಮಾಡಿರಿ. ಕ್ಯಾಲಿಬ್ರೇಶನ್ ಮಾಡುವ ಕಾಲಾವಧಿಯು ಪ್ಲೇಟ್ ನ ನಿರ್ವಹಣೆ ಮತ್ತು ಬಳಕೆಯ ಪ್ರಮಾಣದಲ್ಲಿ ಅವಲಂಬಿಸಿರುತ್ತದೆ. ಪ್ಲೇಟ್ ಸ್ಥಿರ ಉಷ್ಣಾಂಶದಲ್ಲಿ ಇಟ್ಟಲ್ಲಿ, ಧೂಳು ಮತ್ತು ಕಸದಿಂದ ರಕ್ಷಿಸಿದ್ದಲ್ಲಿ ಅದು ಗರಿಷ್ಠ ಕಾಲಾವಧಿಯ ತನಕ ಬಾಳಿಕೆ ಬರಬಲ್ಲದು.
6.ಕ್ಯಾಲಿಬ್ರೇಶನ್ ಅಪ್ಲಿಕೇಶನ್ ನಲ್ಲಿ ಅವಲಂಬಿಸಿರುತ್ತದೆ. ಸಾಮಾನ್ಯವಾಗಿ ಕನಿಷ್ಠ ವರ್ಷಕ್ಕೊಮ್ಮೆಯಾದರೂ ಸಾಮಗ್ರಿಗಳ ಕ್ಯಾಬಿಬ್ರೇಟ್ ಮಾಡಲೇಬೇಕು, ಎಂಬ ಸಲಹೆಯನ್ನು ನಾವು ನೀಡುತ್ತೇವೆ. ಕ್ಯಾಲಿಬ್ರೇಶನ್ ಗೆ ಗ್ರಾಹಕರು ಅವರ ಉತ್ಪಾದಕರೊಂದಿಗೆ ಅಥವಾ NABL ನಿಂದ ಪ್ರಮಾಣೀಕರಿಸಲಾದ ಪ್ರಯೋಗ ಶಾಲೆಗಳೊಂದಿಗೆ ಸಂಪರ್ಕ ಸಾಧಿಸಬೇಕು.
ಸಹ-ಲೇಖಕರು : ವಿ. ಸೇಕರ್ (ಜನರಲ್ ಮ್ಯಾನೆಜರ್, ಮೆಟ್ರಾಲಾಜಿ ವಿಭಾಗ,
ಗಿಂಡಿ ಮಶಿನ್ ಟೂಲ್ಸ್ ಲಿಮಿಟೆಡ್)