ಕೈಗಾರಿಕೋದ್ಯಮಗಳಲ್ಲಿ ಅನೇಕ ರೀತಿಯ ಯಂತ್ರಭಾಗಗಳನ್ನು ತಯಾರಿಸಲಾಗುತ್ತದೆ. ಈ ಯಂತ್ರಭಾಗಗಳನ್ನು ತಯಾರಿಸುವಾಗ ಲೋಹಗಳಿಗೆ ಮತ್ತು ಮಶಿನ್ ಗಳಿಗೆ ಬೇರೆಬೇರೆ ಕಟಿಂಗ್ ಟೂಲ್ ಗಳ ಸಹಾಯದಿಂದ ಅನೇಕ ವಿಧದ ಕಾರ್ಯಪದ್ಧತಿಯನ್ನು ಬಳಸಲಾಗುತ್ತದೆ. ಆದರೆ ತಯಾರಿಸಿರುವ ಯಂತ್ರಭಾಗಗಳ ಪರೀಕ್ಷೆಯನ್ನು ಮಾಡಿ ಅವುಗಳು ಬಳಸಲು ಯೋಗ್ಯವಾಗಿವೆ, ಎಂಬುದನ್ನು ದೃಢೀಕರಿಸುವ ತನಕ ಅದಕ್ಕೆ ಸಂಬಂಧಪಟ್ಟ ಕೆಲಸವು ಪೂರ್ತಿಯಾಗುವುದಿಲ್ಲ. ಈ ಪ್ರಕ್ರಿಯೆಯಲ್ಲಿ ಅನೇಕ ರೀತಿಯ ಅಂಶಗಳು ಗಮನಕ್ಕೆ ಬಂದವು. ಅಪೇಕ್ಷಿಸಿರುವ ಪ್ಯಾರಾಮೀಟರ್ ನ ಮಾಪನವನ್ನು ಮಾಡಲು ಯೋಗ್ಯ ರೀತಿಯ ಸಾಮಗ್ರಿಗಳು ಅಥವಾ ಕಾರ್ಯಪದ್ಧತಿಯನ್ನು ಆಯ್ಕೆ ಮಾಡಲಾಗಿಲ್ಲ. ಹಾಗೆಯೇ ಒಂದು ವೇಳೆ ಈ ಪರೀಕ್ಷೆಯಲ್ಲಿ ಆಯಾ ಪ್ಯಾರಾಮೀಟರ್ ಗಳಿಗೆ ಮನ್ನಣೆ ನೀಡಲ್ಪಟ್ಟರೂ ಕೂಡಾ ಪ್ರತ್ಯಕ್ಷವಾಗಿ ಆ ಯಂತ್ರಭಾಗಗಳನ್ನು ಜೋಡಿಸುವಾಗ ಅವುಗಳು ತಿರಸ್ಕರಿಸಲ್ಪಡುತ್ತವೆ (ರಿಜೆಕ್ಟ್). ಆದುದರಿಂದ ಮಾಪನಕ್ಕೆ ಬಳಸಲಾಗುವ ಉಪಕರಣೆಗಳು ಮತ್ತು ಮಾಪನದ ರೀತಿಯನ್ನೂ ಯಂತ್ರಣೆಯ ಕೆಲಸದ ರೀತಿಯಷ್ಟೇ ಸೂಕ್ಷ್ಮವಾಗಿ ಚುನಾಯಿಸಬೇಕಾಗುತ್ತದೆ. ಹೀಗಾದಲ್ಲಿ ಮಾತ್ರ ವ್ಯವಸಾಯದ ಗುಣಮಟ್ಟ ಮತ್ತು ಅದರಿಂದ ಲಭಿಸುವ ಲಾಭದಲ್ಲಿ ಹೆಚ್ಚಳವಾಗುವುದು ಸಾಧ್ಯ ಮತ್ತು ಅದನ್ನು ನಿರಂತರವಾಗಿ ಕಾಪಾಡುವುದೂ ಸಾಧ್ಯ.
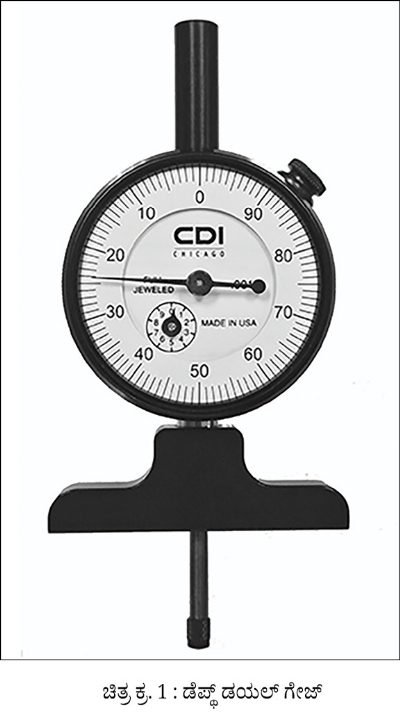
ನಮ್ಮ ‘ಎಕ್ಯುರೇಟ್’ ಕಂಪನಿಯ ವತಿಯಿಂದ ಕಳೆದ ಸುಮಾರು 5 ದಶಕಗಳ ಕಾರ್ಯನಿರ್ವಹಣೆಯಲ್ಲಿ ಮಾಪನದ ಕ್ಷೇತ್ರದಲ್ಲಿ ಭಾರತೀಯ ಉದ್ಯಮಗಳಲ್ಲಿ ಅನೇಕ ಆಧುನಿಕ ಉಪಕರಣಗಳನ್ನು ಅಭಿವೃದ್ಧಿಪಡಿಸಲಾಗಿದೆ. ಹೊಸದಾಗಿ ಮಾರುಕಟ್ಟೆಯಲ್ಲಿ ಇವುಗಳು ಕಾಲೂರಿ ಯಶಸ್ವಿಯಾಗಿ ಕೆಲಸವನ್ನು ನಿರ್ವಹಿಸುತ್ತಿವೆ. ಈ ಕಾಲಾವಧಿಯಲ್ಲಿ ನಮಗೆ ಅನೇಕ ಸವಾಲುಗಳನ್ನು ಎದುರಿಸಬೇಕಾಯಿತು. ಇಂತಹ ಸವಾಲುಗಳಿಂದಾಗಿ ನಾವು ಅನೇಕ ಉಪಕರಣಗಳನ್ನು ನಿರ್ಮಿಸಿದೆವು. ಉಪಕರಣಗಳನ್ನು ನಿರ್ಮಿಸುವಾಗ ಎದುರಾಗಿರುವ ಸವಾಲುಗಳು ಮತ್ತು ಸಾಧನೆಯ ಕುರಿತು ಈ ಲೇಖನದಲ್ಲಿ ಓದುಗರಿಗೋಸ್ಕರ ವಿವರಗಳನ್ನು ನೀಡುವ ಪ್ರಯತ್ನವನ್ನು ಮಾಡಲಾಗುತ್ತಿದೆ. ಈ ಸಂಚಿಕೆಯಲ್ಲಿ ನಾವು ಪ್ರಸ್ತುತ ಕಾಲಕ್ಕೆ ಅನುಗುಣವಾದಂತಹ ಕೊ-ಆರ್ಡಿನೇಟ್ ಮೆಶರಿಂಗ್ ಮಶಿನ್ ಗಳ ಕುರಿತು (ಸಿ.ಎಮ್.ಎಮ್.) ಮಾಹಿತಿಯನ್ನು ತಿಳಿದುಕೊಳ್ಳಲಿದ್ದೇವೆ. ಇದಕ್ಕೂ ಮುಂಚೆ ಸಿ.ಎಮ್.ಎಮ್.ನ ಉಗಮವಾಗುವ ಮುಂಚಿನ ಕಾಲದಲ್ಲಿ ಯಂತ್ರಭಾಗಗಳ ಪರೀಕ್ಷೆಯ ಹಲವಾರು ರೀತಿಯ ಕುರಿತು ಸಂಕ್ಷಿಪ್ತವಾಗಿ ತಿಳಿದುಕೊಳ್ಳೋಣ.
ಸ್ಟೀಲ್ ನ ಅಳತೆ ಪಟ್ಟಿ (ಸ್ಕೇಲ್) ಅಥವಾ ಅದಕ್ಕಿಂತ ನಿರ್ದೋಷವಾಗಿ ಮಾಪನ ಮಾಡುವಂತಹ ವರ್ನಿಯರ್ ಕ್ಯಾಲಿಪರ್/ ಡೆಪ್ಥ್ ಡಯಲ್ ಇಂತಹ ಉಪಕರಣಗಳು ತಮಗೆಲ್ಲರಿಗೂ ಸಾಕಷ್ಟು ಪರಿಚಿತವಾಗಿವೆ. ಈ ಉಪಕರಣಗಳು ಒಂದೇ ಅಕ್ಷದಲ್ಲಿರುವ ನೇರವಾದ ರೇಖೆಯಲ್ಲಿರುವ ಮಾಪನಗಳನ್ನು ಮಾಡುತ್ತವೆ. (ಚಿತ್ರ ಕ್ರ. 1) ಒಂದು ವೇಳೆ X, Y ಮತ್ತು Z ಈ ಮೂರೂ ಅಕ್ಷದಲ್ಲಿರುವ ಮಾಪನಗಳನ್ನು ಮಾಡುವ ಉಪಕರಣದ ಕುರಿತು ವಿಚಾರ ಮಾಡಿದಲ್ಲಿ ಸಿ.ಎಮ್.ಎಮ್. ಕೂಡಾ ಅದೇ ರೀತಿ ಇರುವುದು ಗಮನಕ್ಕೆ ಬರುತ್ತದೆ.
ಹೆಚ್ಚಿನ ಉಪಕರಣಗಳಲ್ಲಿ ಮಾಪನವನ್ನು ಮಾಡುವಾಗ ಉಪಕರಣಗಳ ವಿಶಿಷ್ಟ ಸರ್ಫೇಸ್ ಯಂತ್ರಭಾಗವನ್ನು ಸ್ಪರ್ಶಿಸುತ್ತದೆ. ಈ ರೀತಿಯನ್ನು ‘ಕಾಂಟಾಕ್ಟ್ ಟೈಪ್ ಮಾಪನದ ರೀತಿ’ ಎಂದು ಕರೆಯುತ್ತಾರೆ. ಒಮ್ಮೊಮ್ಮೆ ಈ ರೀತಿಯಲ್ಲಿ ಮಾಪನವನ್ನು ಮಾಡುವಾಗ ಲಭಿಸಿರುವ ಫಲಿತಾಂಶದಲ್ಲಿ ಸಾಕಷ್ಟು ಪ್ರಮಾಣದಲ್ಲಿ ನಿಖರತೆ ಅಥವಾ ನಿರಂತರತೆಯು ಲಭಿಸುವುದಿಲ್ಲ. ಅಲ್ಲದೇ ಅದರಲ್ಲಿ ತುಂಬಾ ಮಿತಿಗಳಿರುತ್ತವೆ. ಇನ್ನೊಂದು ಕಾರಣವೆಂದರೆ, ಇಂತಹ ಕೆಲಸದ ರೀತಿಯಲ್ಲಿ ಒಳಗೊಂಡಿರುವ ಮಾನವನ ಕೆಲಸದ ಸಹಭಾಗಿತ್ವ. ಅದು ಉಪಕರಣಗಳ ಡಯಲ್ ಗೆ ನೀಡಿರುವ ಒತ್ತಡದ ವ್ಯತ್ಯಾಸದಿಂದಲೂ ಇರಬಹುದು ಅಥವಾ ಅದು ಯಂತ್ರಭಾಗದ ಸಂದರ್ಭವನ್ನು ಪಡೆಯುವಾಗಲೂ ಇರಬಹುದು (ರೆಫರನ್ಸ್ ಪಡೆಯುವುದು ಅಥವಾ ಟ್ರೂ ಮಾಡುವುದು).
ಇದರ ಹೊರತಾಗಿ ಉಪಕರಣಗಳಲ್ಲಿ ಜೋಡಿಸಿರುವ ಭಾಗಗಳು ಒಂದಕ್ಕೊಂದರಲ್ಲಿ ಸ್ಲೈಡ್ ಆಗುತ್ತಿರುತ್ತವೆ ಅಥವಾ ಹಲ್ಲುಗಳಲ್ಲಿ ತಿರುಗುತ್ತವೆ. ಈ ಜೋಡಣೆಯಲ್ಲಿರುವ ರಿಲೆಟಿವ್ ಬ್ಯಾಕ್ ಲ್ಯಾಶ್ ಇದು ಕೂಡಾ ರೀಡಿಂಗ್ ನಲ್ಲಿ ವ್ಯತ್ಯಾಸವನ್ನುಂಟು ಮಾಡುವಲ್ಲಿ ಕಾರಣವಾಗಬಲ್ಲದು. ಈ ವ್ಯತ್ಯಾಸ ಪಾಯಿಂಟರ್ ನಿಂದ ರೀಡಿಂಗ್ ತೋರಿಸುವಂತಹ ಉಪಕರಣಗಳಲ್ಲಿ (ಎನಾಲಾಗ್ ಟೈಪ್) ಹೆಚ್ಚು ಪ್ರಮಾಣದಲ್ಲಿ ಕಂಡುಬರುತ್ತದೆ. ಈ ವ್ಯತ್ಯಾಸವನ್ನು ದೂರ ಮಾಡುವ ದೃಷ್ಟಿಯಲ್ಲಿ ಡಿಜಿಟಲ್ ವಿಧದ ಉಪಕರಣಗಳನ್ನು ಅಭಿವೃದ್ಧಿಪಡಿಸಲಾಯಿತು.
ಹಲವಾರು ಯಂತ್ರಭಾಗಗಳು ಒಂದು ವೇಳೆ ಕ್ಲಿಷ್ಟ ಅಥವಾ ಜಟಿಲವಾಗಿದ್ದಲ್ಲಿ, ಮಾಪನಗಳನ್ನು ಆ ಯಂತ್ರಭಾಗಗಳ ಮಶಿನ್ ನಿಂದಲೇ ಕೆಳಗೆ ಇರಿಸಿ ಗ್ರೆನೈಟ್ ನ ಸರ್ಫೇಸ್ ಪ್ಲೇಟ್ ನಲ್ಲಿಟ್ಟು ಇನ್ನಿತರ ಉಪಕರಣಗಳ ಸಹಾಯದಿಂದ ಮಾಪನ ಮಾಡಬೇಕಾಗುತ್ತದೆ. (ಚಿತ್ರ ಕ್ರ. 2) ಉದಾಹರಣೆ, ಅಕ್ಷಗಳ ಕಾಂನ್ಸೆಟ್ರಿಸಿಟಿ, ಅಕ್ಷಗಳ ಅಂಗ್ಯುಲರ್ ಪೊಸಿಶನ್, ಸರ್ಫೇಸ್ ನ ರೌಂಡ್ ನೆಸ್, ಅಥವಾ ಫ್ಲ್ಯಾಟ್ ನೆಸ್ ಇತ್ಯಾದಿ. ಈ ರೀತಿಯಲ್ಲಿ ಪರೀಕ್ಷೆ ಮಾಡುವ ರೀತಿಗೆ ‘ಫಸ್ಟ್ ಪ್ರಿನ್ಸಿಪಲ್’ನಿಂದ ತಪಾಸಣೆ ಮಾಡುವುದು ಎಂದು ಹೇಳುತ್ತಾರೆ.
ಸರ್ಫೇಸ್ ಪ್ಲೇಟ್ ನಲ್ಲಿರುವ ಮಾಪನದ ರೀತಿಯಲ್ಲಿ ಎರಡು ವಿಧದ ಮಿತಿಗಳು ಪ್ರಮುಖವಾಗಿ ಕಂಡುಬರುತ್ತಿದ್ದವು. ಒಂದು ಅಂದರೆ ತಪಾಸಣೆ ಮಾಡುವ ಯಂತ್ರಭಾಗಗಳ ರೆಫರನ್ಸ್ ಪಡೆಯಲು ಅಥವಾ ಆ ಯಂತ್ರಭಾಗವನ್ನು ಟ್ರೂ ಮಾಡಲು ತುಂಬಾ ಸಮಯವೂ ಬೇಕಾಗುತ್ತದೆ. ಇದರಿಂದಾಗಿ ಯಾವುದೇ ಸೆಟಿಂಗ್ ಬದಲಿಸಿದ ನಂತರ ಯಂತ್ರಭಾಗಗಳ ತಪಾಸಣೆ ಮಾಡಿ, ಅದನ್ನು ಡ್ರಾಯಿಂಗ್ ನಂತೆ ಇದೆಯೇ ಎಂಬುದು ಮನವರಿಕೆಯಾಗಲು ತುಂಬಾ ಸಮಯವು ಬೇಕಾಗುತ್ತದೆ. ಸಿ.ಎನ್.ಸಿ.ಯಂತಹ ದುಬಾರಿಯಾದ ಮಶಿನ್, ಯಂತ್ರಣೆಯಾದ ನಂತರ ಕೇವಲ ಯಂತ್ರಭಾಗಗಳ ತಪಾಸಣೆ ಮಾಡಿ ಸರಿಯಾಗಿದೆ ಖಾತರಿಯಾದ ನಂತರ ಆಫ್ ಮಾಡಿಡುವುದು, ಖಂಡಿತವಾಗಿಯೂ ಪೂರೈಸುವಂತಹದ್ದಾಗಿರಲಿಲ್ಲ. ಅಲ್ಲದೇ ಮಾನವನಿಂದ ಆಗಿರುವ ತಪ್ಪುಗಳಿಂದಾಗಿ ತಪಾಸಣೆಯಲ್ಲಿರುವ ನಿರಂತರತೆಯೂ ಲಭಿಸುತ್ತಿರಲಿಲ್ಲ.
ಸಿ.ಎನ್.ಸಿ. ಮಶಿನ್ ನಲ್ಲಿ ಯಾವುದೇ ಯಂತ್ರಭಾಗಗಳ ಯಂತ್ರಣೆಯನ್ನು ಪೂರ್ತಿ ಮಾಡಿದ ನಂತರ ಅದೇ ಮಶಿನ್ ನಲ್ಲಿ ಅದರ ತಪಾಸಣೆಯನ್ನು ಮಾಡಲಾಗುತ್ತದೆ, ಎಂಬಂತಹ ಪರಿಹಾರವನ್ನು ಪ್ರಾರಂಭದಲ್ಲಿಯೇ ಮಾಡಲಾಯಿತು. ಈ ರೀತಿಯಲ್ಲಿ ಹಲವಾರು ನಿರ್ಧಾರಿತ ವಿಧಗಳ ಸಂಜ್ಞೆಗಳನ್ನೂ ತಯಾರಿಸಲಾಯಿತು. ಆದರೆ ಆ ಪರಿಹಾರವು ಕೂಡಾ ಸಿ.ಎನ್.ಸಿ. ಮಶಿನ್ ನಲ್ಲಿ ಯಂತ್ರಣೆಯನ್ನು ನಿಲ್ಲಿಸಿ ತಪಾಸಣೆ ಮಾಡುವ ವ್ಯವಸ್ಥೆಯನ್ನು ಮಾಡಿದ್ದರಿಂದ ಅಪೇಕ್ಷಿಸಿರುವ ಉತ್ಪಾದಕತೆಯು ಲಭಿಸುವುದಿಲ್ಲ. ಅಲ್ಲದೇ ಹಲವಾರು ವರ್ಷಗಳು ಮಶಿನ್ ಬಳಸಿದ ನಂತರ ತಪಾಸಣೆಯಲ್ಲಿರುವ ನಿಖರತೆಯ ಗುಣಮಟ್ಟವೂ ಕಡಿಮೆಯಾಗುತ್ತಿತ್ತು.
ಸಿ.ಎಮ್.ಎಮ್.ನ ಆವಶ್ಯಕತೆ ಯಾವುದಕ್ಕೋಸ್ಕರ ನಿರ್ಮಾಣವಾಯಿತು, ಎಂಬುದನ್ನು ತಿಳಿದುಕೊಳ್ಳಲು ನಾವು ಒಂದು ಯಂತ್ರಭಾಗದ ಉದಾಹರಣೆಯನ್ನು ಸ್ಪಲ್ಪ ವಿಸ್ತಾರವಾಗಿ ತಿಳಿದುಕೊಳ್ಳೋಣ. ನಮ್ಮ ಗ್ರಾಹಕರೊಬ್ಬರಿಂದ ತರಲಾದ ಇಂಜಿನ್ ನ ಸಿಲಿಂಡರ್ ಹೆಡ್. ಈ ಯಂತ್ರಭಾಗದ ಡ್ರಾಯಿಂಗ್ ಕೆಲವು ಭಾಗಗಳನ್ನು ಚಿತ್ರ ಕ್ರ. 3 ರಲ್ಲಿ ತೋರಿಸಲಾಗಿದೆ. ಈ ಚಿತ್ರದಲ್ಲಿ ತೋರಿಸಿದಂತೆ ಹಲವಾರು ಮಹತ್ವದ ಮಾನದಂಡಗಳನ್ನು ತಪಾಸಣೆ ಮಾಡಲು, ನಮ್ಮಿಂದ ಯೋಗ್ಯವಾದ ಉಪಕರಣವು ಅವರಿಗೆ ಬೇಕಾಗಿತ್ತು. ಚಿತ್ರದಲ್ಲಿ ತೋರಿಸಿದಂತೆ ವಾಲ್ವ್ ಗೈಡ್ ಬೋರ್ ಮತ್ತು ವಾಲ್ವ್ ಸೀಟ್ ನ ಯಂತ್ರಣೆ ಇದೇ ಈ ಯಂತ್ರಭಾಗಗಳ ಮೂಲವಾಗಿದೆ. ಈ ಎರಡೂ ಇನ್ನಿತರ ಸರ್ಫೇಸ್ ಗಳೊಂದಿಗಿನ ಸಂಬಂಧವು ಕೂಡಾ (ರಿಲೇಶನ್) ಅಷ್ಟೇ ನಿಖರವಾಗಿ ಮತ್ತು ನಿರ್ದಿಷ್ಟವಾಗಿ ಇರುವುದು ಇಂಜಿನ್ ನ ಚಟುವಟಿಕೆಯ ದೃಷ್ಟಿಯಲ್ಲಿ ಮಹತ್ವದ್ದಾಗಿರುತ್ತದೆ. ಆ ನಿಟ್ಟಿನಲ್ಲಿ ಹಲವಾರು ಮಹತ್ವದ ಪ್ಯಾರಾಮೀಟರ್ ಗಳನ್ನು ಈ ಮುಂದೆ ನೀಡಲಾಗಿದೆ. ಅಲ್ಲದೇ ಚಿತ್ರ ಕ್ರ. 3 ರಲ್ಲಿ ಅವುಗಳನ್ನು ಬೇರೆಯೇ ಬಣ್ಣದಿಂದ ತೋರಿಸಲಾಗಿದೆ.
ಸಿಲಿಂಡರ್ ಹೆಡ್ ನಲ್ಲಿ ಅಳತೆ ಮಾಡಬೇಕಾದ ಹಲವಾರು ಮಹತ್ವದ ಪ್ಯಾರಾಮೀಟರ್ ಗಳು
1. ರೆಸ್ಟಿಂಗ್ ಸರ್ಫೇಸ್ ನ ಸಮತಟ್ಟುತನ-C
2. ವಾಲ್ವ್ ಗೈಡ್ ಬೋರ್ ಮತ್ತು ವಾಲ್ವ್ ಸೀಟ್ ಬೋರ್ ನ ಸ್ವತಂತ್ರವಾದ ಸಿಲಿಂಡ್ರಿಸಿಟಿ, ಓವ್ಯಾಲಿಟಿ.
3. ವಾಲ್ವ್ ಗೈಡ್ ಬೋರ್ ಮತ್ತು ವಾಲ್ವ್ ಸೀಟ್ ಬೋರ್ ನ ಅಕ್ಷಗಳ ರೆಸ್ಟಿಂಗ್ ಸರ್ಫೇಸ್ ನೊಂದಿಗೆ ಇರುವ ಅಂಗ್ಯುಲರ್ ಪೊಸಿಶನ್.
4. ವಾಲ್ವ್ ಗೈಡ್ ಬೋರ್ ಮತ್ತು ವಾಲ್ವ್ ಸೀಟ್ ಬೋರ್ ಗೆ ಒಂದಕ್ಕೊಂದರೊಂದಿಗೆ ಇರುವ ಕಾನ್ಸೆಂಟ್ರಿಸಿಟಿ ಇದು ಪ್ಯಾರಾ ಮೀಟರ್ ನಷ್ಟು ಮಹತ್ವದ್ದಾಗಿದೆ. ಸಿಲಿಂಡರ್ ನಲ್ಲಿ ವಾಲ್ವ್ ಜೋಡಿಸಿದ ನಂತರ ಕೆಲವೇ ಸೆಕಂಡುಗಳ ನಂತರ ಡಿಸೇಲ್ ಬಳಸಿ ಲೀಕೇಜ್ ಟೆಸ್ಟಿಂಗ್ ಮಾಡಲಾಗುತ್ತದೆ.
ಈ ಪ್ಯಾರಾಮೀಟರ್ ಗಳು ಸರ್ಫೇಸ್ ಪ್ಲೇಟ್ ನಲ್ಲಿ ಫಸ್ಟ್ ಪ್ರಿನ್ಸಿಪಲ್ ನ ತಪಾಸಣೆಯು ತುಂಬಾ ಸಮಯವನ್ನು ವ್ಯರ್ಥ ಮಾಡುತ್ತದೆ. ಅಲ್ಲದೇ ಆ ತಪಾಸಣೆಯಲ್ಲಿ ಉಂಟಾಗುವ ಸಂಭಾವ್ಯ ಮಾನವ ತಪ್ಪುಗಳಿಂದಾಗಿ ನಿಖರವಾದ ವರದಿಯು ಸಿಗುವ ಸಾಧ್ಯತೆ ತುಂಬಾ ಕಡಿಮೆ ಇರುತ್ತದೆ. ಈ ಮಿತಿಗಳಿಂದಾಗಿ ಸಿ.ಎಮ್.ಎಮ್.ನಂತಹ ತಪಾಸಣೆಯ ಮಶಿನ್ ನಲ್ಲಿ ಹಂತ ಹಂತವಾಗಿ ಅಭಿವೃದ್ಧಿಯಾಯಿತು.
ಸಿ.ಎಮ್.ಎಮ್.ನ ಪ್ರಸ್ತುತ ರಚನೆಯಲ್ಲಿರುವ ವೈಶಿಷ್ಟ್ಯಗಳು
ಚಿತ್ರ ಕ್ರ. 4 ರಲ್ಲಿ ಸಾಮಾನ್ಯವಾಗಿ 500 ರಿಂದ 800 ಮಿ.ಮೀ. ಉದ್ದ, ಅಗಲ, ಎತ್ತರ ಈ ಆಕಾರದ ಯಂತ್ರಭಾಗಗಳ ತಪಾಸಣೆಗೋಸ್ಕರ ಬಳಸಲಾಗುವ ಸಿ.ಎಮ್.ಎಮ್.ನ ರಚನೆಯನ್ನು ತೋರಿಸಲಾಗಿದೆ. ಇದರಲ್ಲಿ ತಪಾಸಣೆಗೋಸ್ಕರ ಬಂದಿರುವ ಯಂತ್ರಭಾಗಗಳನ್ನು ಸಮತೋಲಿತವಾಗಿ ಮತ್ತು ಸ್ಥಿರವಾಗಿ ಇಡಲು ಗ್ರೆನೈಟ್ ನ ಸರ್ಫೇಸ್ ಪ್ಲೇಟ್ ದೃಢವಾದ ಬೇಸ್ ನಲ್ಲಿ ಅಳವಡಿಸಲಾಗಿರುತ್ತದೆ.
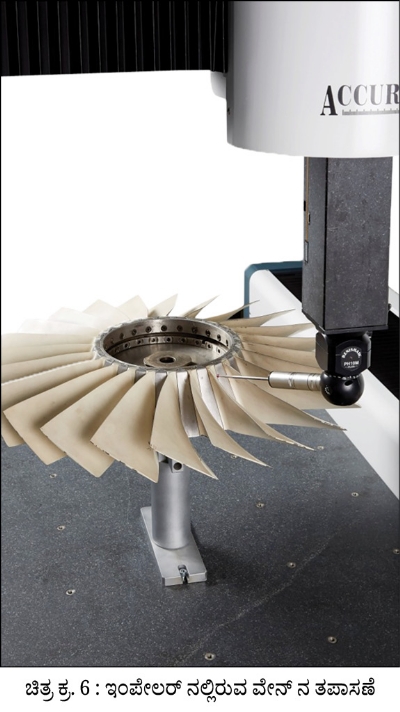
ಇದರಲ್ಲಿ ತುಂಬಾ ಸುಲಭವಾದ ಮತ್ತು ಕಂಪನಗಳಿಲ್ಲದ X ಅಕ್ಷದ ಚಟುವಟಿಕೆಗಳಿಗೆ ಏರ್ ಬೇರಿಂಗ್ ನಲ್ಲಿ ಒಂದು ಬ್ರಿಜ್ ಅಳವಡಿಸಲಾಗಿರುತ್ತದೆ. ಮಶಿನ್ ನಲ್ಲಿ ಅಲುಗಾಡುತ್ತಿರುವ ಭಾಗಗಳ ಸವೆತವಾಗಿ ಅದರ ನಿಖರತೆಯಲ್ಲಿ ಪರಿಣಾಮ ಆಗಬಾರದು ಎಂಬುದಕ್ಕೋಸ್ಕರ ಮಶಿನ್ ನ ಅಲುಗಾಡುವ ಭಾಗಗಳು ಮತ್ತು ಗ್ರೆನೈಟ್ ನ ಗೈಡ್ ವೆ ಇದರಲ್ಲಿ ವಿಶಿಷ್ಟವಾದ ಒತ್ತಡದ ಗಾಳಿಯನ್ನು ನಿರಂತರವಾಗಿ ಬಿಡಲಾಗುತ್ತದೆ. ಇದರಿಂದಾಗಿ ಮಶಿನ್ ನ ಬಾಳಿಕೆಯು ವೃದ್ಧಿಸುತ್ತದೆ. ಬ್ರಿಜ್ ನಲ್ಲಿ Y ಅಕ್ಷದ ಚಟುವಟಿಕೆಗಳಿಗೆ ಒಂದು ಕ್ಯಾರೇಜ್ ಅಳವಡಿಸಲಾಗಿರುತ್ತದೆ. ವರ್ಟಿಕಲ್ ಅಕ್ಷದಲ್ಲಿ ಮೇಲೆ- ಕೆಳಗೆ ಆಗುವಂತಹ ಚಟುವಟಿಕೆಗಳನ್ನು ಈ ಒಂದೇ ಕಾಲಮ್ ನಲ್ಲಿ ನೀಡಲಾಗಿರುತ್ತದೆ. ಕಾಂಟ್ಯಾಕ್ಟ್ ಟೈಪ್ ಮಾಪನಗಳ ದೃಷ್ಟಿಯಲ್ಲಿ ಒಂದು ಪ್ರೊಬ್ ಕಾಲಮ್ ನ ರಾಮ್ ನಲ್ಲಿ ಅಳವಡಿಸಲಾಗಿರುತ್ತದೆ. ಈ ಪ್ರೋಬ್ X, Y ಮತ್ತು Z ಈ ಮೂರೂ ಅಕ್ಷಗಳಲ್ಲಿ ಬೇಕಾದಂತೆ ಹಿಂದೆ-ಮುಂದೆ ಚಟುವಟಿಕೆಯನ್ನು ಮಾಡುತ್ತದೆ. ಈ ಚಟುವಟಿಕೆ ಜಾಯ್ ಸ್ಟಿಕ್ ನ ಸಹಾಯದಿಂದ ಕೈಯಿಂದಲೇ ಮಾಡಬಹುದಾಗಿದೆ ಅಥವಾ ಸ್ವಯಂಚಾಲಿತವಾಗಿಯೂ ಮಾಡಬಹುದಾಗಿದೆ. ಆಗಾಗ ಒಂದೇ ರೀತಿಯ ಭಾಗದ ಪರೀಕ್ಷೆಯನ್ನು ಮಾಡುವುದಾದಲ್ಲಿ ಯಾವುದೇ ಸಂಜ್ಞೆಯನ್ನು (ಕಮಾಂಡ್) ಮಶಿನ್ ನಲ್ಲಿ ಮೊದಲೇ ತಯಾರಿಸಿ, ಈ ಕೆಲಸವನ್ನು ಸ್ವಯಂಚಾಲಿತವಾಗಿ ಮಾಡಲಾಗುತ್ತದೆ.
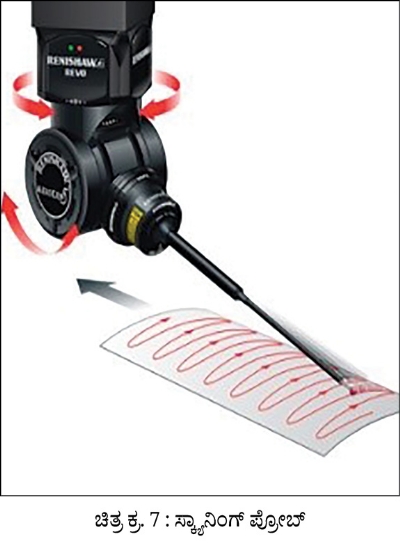
ಹೆಚ್ಚಿನ ಪ್ರೊಬ್ ಗಳು ಟಚ್ ಟ್ರಿಗರ್ ವಿಧದಲ್ಲಿರುತ್ತವೆ. ಈ ಪ್ರೋಬ್ (ಚಿತ್ರ ಕ್ರ. 5) ಯಂತ್ರಭಾಗದ ಅಪೇಕ್ಷಿಸಿರುವ ಸರ್ಫೇಸ್ ನ್ನು ಸ್ಪರ್ಶ ಮಾಡುವಾಗ, ನಿರ್ಧರಿಸಿರುವ ಒತ್ತಡಕ್ಕೆ ಅನುಸಾರವಾಗಿ ಸೆನ್ಸರ್ ನ ಮೂಲಕ ಆ ಮಾಪನವನ್ನು ಪ್ರೊಸೆಸರ್ ನಲ್ಲಿ ನೊಂದಾಯಿಸಲಾಗುತ್ತದೆ. ಆದರೆ ಯಂತ್ರಭಾಗಗಳ ಆಕಾರವನ್ನು ಅಳತೆ ಮಾಡುವಾಗ (ಉದಾಹರಣೆ, ಇಂಪೇಲರ್ ನ ವೇನ್ ನ ಪ್ರೊಫೈಲ್) ಸ್ಕ್ಯಾನಿಂಗ್ ಪ್ರೋಬ್ ಬಳಸಲಾಗುತ್ತವೆ. (ಚಿತ್ರ ಕ್ರ. 6 ಮತ್ತು 7) ಈ ಪ್ರೋಬ್ ನೀಡಿರುವ ಕಮಾಂಡ್ ನಂತೆ ಆ ದಿಕ್ಕಿನಿಂದ ಯಂತ್ರಭಾಗಗಳ ಸಂಪರ್ಕದಲ್ಲಿದ್ದು ಅನೇಕ ನಿರೀಕ್ಷಣೆಗಳನ್ನು ನೊಂದಾಯಿಸುತ್ತವೆ ಮತ್ತು ಆ ಪ್ರೊಫೈಲ್ ನ ನಿಗದಿತ ಆಕಾರವು ಹೇಗಿದೆ, ಎಂಬುದನ್ನು ನಿರ್ದೋಷವಾಗಿ ನೀಡುತ್ತದೆ.
ತಪಾಸಣೆಯನ್ನು ಮಾಡುವಾಗ ಪ್ರೋಬ್ ನ ಸ್ಪರ್ಶ ಬಿಂದು ಯಂತ್ರಭಾಗದ ನಿಗದಿತವಾಗಿ ಯಾವ ಜಾಗದಲ್ಲಿ ಒರಗುವುದು ಅಗತ್ಯವಾಗಿದೆ, ಎಂಬುದು ಆ ಯಂತ್ರಭಾಗಗಳ ರಚನೆಯಲ್ಲಿ ಅವಲಂಬಿಸಿರುತ್ತದೆ. ಆದ್ದರಿಂದ ಬೇರೆಬೇರೆ ಆಕಾರದ ಮತ್ತು ವಿವಿಧ ಉದ್ದದ ಪ್ರೋಬ್ ಮಶಿನ್ ನೊಂದಿಗೆ ಉಪಲಬ್ಧವಿರಿಸಿ ನೀಡಲಾಗಿರುತ್ತದೆ. (ಚಿತ್ರ ಕ್ರ. 8) ಪ್ರೋಬ್ ಹೆಡ್ ನಲ್ಲಿ ಪ್ರೋಬ್ ಬದಲಾಯಿಸುವ ಕ್ರಿಯೆಯನ್ನು ಕೈಯಿಂದ ಅಥವಾ ಸ್ವಯಂಚಾಲನೆಯಿಂದ ಮಾಡಲಾಗುತ್ತದೆ. ಪ್ರೋಬ್ ತುಂಬಾ ಸೂಕ್ಷ್ಮವಾಗಿದ್ದರಿಂದ ಅದನ್ನು ಮುತುವರ್ಜಿ ವಹಿಸಿ ನಿರ್ವಹಿಸಬೇಕಾಗುತ್ತದೆ. ಆದ್ದರಿಂದ ಗ್ರೆನೈಟ್ ಪ್ಲೇಟ್ ನಲ್ಲಿ ಆವಶ್ಯಕತೆಗೆ ತಕ್ಕಂತೆ ಪ್ರೋಬ್ ಪಾರ್ಕಿಂಗ್ ನ ವ್ಯವಸ್ಥೆಯನ್ನೂ ಮಾಡಲಾಗಿರುತ್ತದೆ. ಸ್ವಯಂಚಾಲನೆಯಿಂದ ಪ್ರೋಬ್ ಬದಲಾಯಿಸುವಾಗ ಈ ವ್ಯವಸ್ಥೆಯು ಉಪಯೋಗಕ್ಕೆ ಬರುತ್ತದೆ. (ಚಿತ್ರ ಕ್ರ. 9)
ಸಿ.ಎಮ್.ಎಮ್.ನಲ್ಲಿ ಮೊದಲಾಗಿ ತಪಾಸಣೆ ಮಾಡುವಂತಹ ಯಂತ್ರಭಾಗಗಳನ್ನು ಗ್ರೆನೈಟ್ ಪ್ಲೇಟ್ ನಲ್ಲಿ X ಅಥವಾ Y ಅಕ್ಷಕ್ಕೆ ಸಮಾನಾಂತರವಾಗಿ ಮಾಡಿ ಅಳವಡಿಸಲಾಗುತ್ತದೆ. ಇದು ಯೋಗ್ಯವಾಗಿ ಸ್ಥಿರವಾಗಿದೆ, ಎಂಬುದನ್ನು ಖಾತರಿ ಪಡಿಸಲಾಗುತ್ತದೆ. ಸಿ.ಎಮ್.ಎಮ್. ನಲ್ಲಿ ವಿವಿಧ ಪ್ಯಾರಾಮೀಟರ್ ಗಳ ಮಾಪನವನ್ನು ಮಾಡಲು ವಿವಿಧ ಪರ್ಯಾಯಗಳು (ಪ್ರೊಗ್ರಾಮ್) ಉಪಲಬ್ಧವಿರುತ್ತವೆ. ಯಾವ ಪ್ಯಾರಾಮೀಟರ್ ನ ಮಾಪನವನ್ನು ಮಾಡಬೇಕೋ, ಅದರ ಕಮಾಂಡ್ ಗಳನ್ನು ಆಯ್ಕೆ ಮಾಡಿ ಅದಕ್ಕೆ ಸೂಕ್ತವಾದ ಪ್ರೋಬ್ ಚುನಾಯಿಸಬೇಕಾಗುತ್ತದೆ. ಪ್ರಾರಂಭದಲ್ಲಿ ಕೈಯಿಂದ ನಿಯಂತ್ರಿಸಿ ಪ್ರೋಬ್ ಯಂತ್ರಭಾಗಗಳ ಸರ್ಫೇಸ್ ನ ಹತ್ತಿರ ತಂದು ಕಮಾಂಡ್ ಗೆ ಅನುಗುಣವಾಗಿ ಮುತುವರ್ಜಿಪೂರ್ವಕವಾಗಿ ಸ್ಪರ್ಷ ಮಾಡಿ ಸ್ವಲ್ಪ ಒತ್ತಡವನ್ನು (ಪ್ರೆಶರ್) ನೀಡಲಾಗುತ್ತದೆ. ನಿರ್ಧಾರಿತ ಒತ್ತಡದ ನಂತರ ಆ ನಿರೀಕ್ಷಣೆಯನ್ನು ಸೆನ್ಸ್ ಮಾಡಿ ಪ್ರೊಸೆಸರ್ ಗೆ ಕಳುಹಿಸಲಾಗುತ್ತದೆ. ಈ ರೀತಿಯ ಅನೇಕ ಅಪೇಕ್ಷಿತ ನಿರೀಕ್ಷಣೆಗಳ ಸೆಟ್ ತಯಾರಾದ ನಂತರ ಆದಕ್ಕೆ ಆಧರಿಸಿ ಆ ಪ್ಯಾರಾಮೀಟರ್ ನ ನಿಖರವಾದ ಮಾಪನಗಳು (ವ್ಯಾಲ್ಯೂ) ಸಿಗುತ್ತದೆ. ಅಲ್ಲದೇ ಆದನ್ನು ಡ್ರಾಯಿಂಗ್ ನಲ್ಲಿ ನೀಡಿರುವ ಟಾಲರನ್ಸ್ ನ ಹೋಲಿಕೆಯಂತೆ ಹೇಗಿದೆ, (ಎಕ್ಸೆಪ್ಟೆಡ್ ಅಥವಾ ರಿಜೆಕ್ಟೆಡ್) ಎಂಬುದನ್ನು ಹೇಳಲಾಗುತ್ತದೆ. ಈ ವರದಿಯ ಮುದ್ರಿತ ಪ್ರತಿ (ಪ್ರಿಂಟ್ ಔಟ್) ಪಡೆದು ಅದರ ವರದಿಯನ್ನು ಸಂಗ್ರಹಿಸಿಲಾಗುತ್ತದೆ. ಮಾದರಿಗೋಸ್ಕರ ಸಿಲಿಂಡರ್ ಹೆಡ್ ನ ವರದಿಯನ್ನು ಚಿತ್ರ ಕ್ರ. 10 ರಲ್ಲಿ ನೀಡಲಾಗಿದೆ.
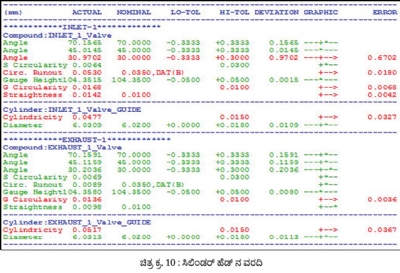
ತಪಾಸಣೆ ಮಾಡಲಾಗುವ ಯಂತ್ರಭಾಗಗಳ ಆಕಾರ, ಅದರ ಮಾಪನ ಮತ್ತು ಅದರಲ್ಲಿ ತಪಾಸಣೆ ಮಾಡಬೇಕಾಗಿರುವ ಪ್ಯಾರಾಮೀಟರ್ ಮತ್ತು ಅದರ ಕ್ಲಿಷ್ಟತೆ ಇದರಿಂದ ನಾವು ನಮ್ಮ ಸಿ.ಎಮ್.ಎಮ್.ನ ಉತ್ಪಾದನೆಗಳನ್ನು ಆಗಾಗ ಅಭಿವೃದ್ಧಿ ಮಾಡುತ್ತಾ ಮುಂದುವರಿದೆವು. ಈ ಕೆಲಸದ ಪ್ರೋಬ್ ನ ಅಭಿವೃದ್ಧಿಯಲ್ಲಿ ‘ರೆನಿಶಾ’ ಕಂಪನಿಯವರು ನಮ್ಮೊಂದಿಗೆ ಅಮೂಲ್ಯವಾದ ಯೋಗದಾನವನ್ನು ನೀಡಿದ್ದಾರೆ. ಕ್ಲಿಷ್ಟ ಮತ್ತು ನಿಖರವಾದ ಯಂತ್ರಭಾಗಗಳ ಯಂತ್ರಣೆಯನ್ನು ಮಾಡುವಂತಹ ಲಘು ಮತ್ತು ಮಧ್ಯಮ ಆಕಾರದ ಉದ್ಯಮಿಗಳಲ್ಲಿಯೂ ಪ್ರಸ್ತುತ ಸಿ.ಎಮ್.ಎಮ್. ಇರುವುದೂ ಅತ್ಯಂತ ಮಹತ್ವದ ಅಂಶವಾಗಿದೆ. ಸಿ.ಎಮ್.ಎಮ್.ನ ಶ್ರೇಣಿಯಲ್ಲಿ ನಮ್ಮ ಅನೇಕ ಮಾಡೆಲ್ ಗಳು ಮಾರುಕಟ್ಟೆಯಲ್ಲಿ ಉಪಲಬ್ಧವಿವೆ. ಅದರಲ್ಲಿರುವ ಹಲವಾರು ಮಾಡೆಲ್ ಗಳನ್ನು ಚಿತ್ರ ಕ್ರ. 11, 12 ಮತ್ತು 13 ರಲ್ಲಿ ನೀಡಲಾಗಿದೆ.
ಸಿ.ಎಮ್.ಎಮ್.ನ ತಂತ್ರಜ್ಞಾನವು ಮೊದಲಾಗಿ 1965 ರ ಅಂದಾಜಿಗೆ ಯುರೋಪ್ ನಲ್ಲಿ ಅಭಿವೃದ್ಧಿ ಪಡಿಸಲಾಯಿತು. ಮುಂದೆ ಯುನೈಡೆಟ್ ಕಿಂಗ್ಡಮ್, ಇಟಲಿ, ಜರ್ಮನಿಯಂತಹ ದೇಶಗಳೂ ಅದರಲ್ಲಿ ನಿಪುಣರಾದವು. ನಮ್ಮಲ್ಲಿ ಈ ರೀತಿಯ ಸಿ.ಎಮ್.ಎಮ್. ತಯಾರಿಸುವ ವಿಚಾರವನ್ನು 1985 ರ ಅಂದಾಜಿಗೆ ಮಾಡಲಾಯಿತು. ಪ್ರತ್ಯಕ್ಷವಾದ ಉತ್ಪಾದನೆಯು 1991 ರ ಅಂದಾಜಿಗೆ ಪ್ರಾರಂಭಿಸಲಾಯಿತು. ಮಶಿನ್ ತಯಾರಾಗುವ ಸಮಯದಲ್ಲಿ ಇಂತಹ ಮಶಿನ್ ಗಳು ತುಂಬಾ ದುಬಾರಿಯಾಗಿದ್ದರಿಂದ ಅವುಗಳ ಸಂಖ್ಯೆಯು ತುಂಬಾ ಕಡಿಮೆಯೇ ಇತ್ತು. ಈ ಪರಿಸ್ಥಿತಿಯಲ್ಲಿ ಮಶಿನ್ ನ ಕವರ್ ತೆಗೆದು ಒಳ ಭಾಗವನ್ನು ತುಂಬಾ ಸೂಕ್ಷ್ಮವಾಗಿ ನೋಡುವುದು ತುಂಬಾ ಕಠಿಣವಾಗಿದ್ದು. ಇದರಿಂದಾಗಿ ಇಂತಹ ಸಿ.ಎಮ್.ಎಮ್. ನಮ್ಮ ಕಂಪನಿಯಲ್ಲಿ ತಯಾರಿಸಲು ಅನೇಕ ಭಾಗಗಳ ಕುರಿತು ವಿಚಾರ ಮಾಡುವುದು ಅಥವಾ ಏರ್ ಬೇರಿಂಗ್ ನಂತರ ಭಾಗಗಳಿಗೆ, ಅದರಲ್ಲಿ ಉಪಯೋಗಕ್ಕೆ ಇಲ್ಲದ ಭಾಗಗಳ ರಿವರ್ಸ್ ಇಂಜಿನಿಯರಿಂಗ್ ಮಾಡುವುದು ಇದರ ಹೊರತಾಗಿ ಇನ್ನೊಂದು ಪರ್ಯಾಯವಾಗಿತ್ತು.
ಎರಡನೇ ಸವಾಲುಗಳುಳ್ಳ ಪರಿಸ್ಥಿತಿ ಎಂದರೆ ಇಲೆಕ್ಟ್ರಾನಿಕ್ ಸೆನ್ಸರ್ ನಂತಹ ಭಾಗಗಳನ್ನು ಅಭಿವೃದ್ಧಿ ಪಡಿಸುವುದು. ಆ ಕಾಲದಲ್ಲಿ ಇಂತಹ ಭಾಗಗಳಿಗೆ ಶೇಕಡಾ 100 ರಷ್ಟು ಆಮದು ಶುಲ್ಕ (ಇಂಪೋರ್ಟ್ ಡ್ಯೂಟಿ) ಇದ್ದಿದ್ದರಿಂದ ಆ ಕಾಲದಲ್ಲಿ ನಮಗೆ ಮೊದಲ ಒಂದು ಮಶಿನ್ ತಯಾರಿಸಲು ಸುಮಾರು 10 ಲಕ್ಷ ರೂಪಾಯಿಗಳನ್ನು ಖರ್ಚು ಮಾಡಬೇಕಾಗುತ್ತಿತ್ತು. ಈ ಮಶಿನ್ ನ ನಿಖರತೆಯ ತಪಾಸಣೆಯನ್ನು ಮಾಡಲು ಆವಶ್ಯಕವಿರುವ ಲೇಸರ್ ಮಶಿನ್ ಕೂಡಾ ತುಂಬಾ ದುಬಾರಿಯಾಗಿತ್ತು. ಆದ್ದರಿಂದ ನಾವು ಹಲವಾರು ಮಶಿನ್ ಟೂಲ್ ಉತ್ಪಾದಕರಲ್ಲಿ ಇದ್ದ ಮಶಿನ್ ಗಳನ್ನು ಬಳಸಿ ನಮ್ಮ ಆವಶ್ಯಕತೆಯನ್ನು ಪೂರೈಸಿದೆವು. ಭಾರತದಲ್ಲಿ ಕಂಪ್ಯೂಟರ್ ಪ್ರಚಾರವು ಸ್ವಲ್ಪ ಪ್ರಮಾಣದಲ್ಲಿ ಪ್ರಾರಂಭಗೊಂಡಿತ್ತು. ನಾವು ಮಶಿನ್ ನಲ್ಲಿರುವ ಗಣಿತದ ಸಮೀಕರಣಗಳಿಗೆ ಆಧರಿಸಿರುವ ಮೈಕ್ರೊಪ್ರೊಸೆಸರ್ ಬಳಸಿ ಈ ಸವಾಲನ್ನು ಸಮರ್ಥವಾಗಿ ನಿಭಾಯಿಸಿದೆವು. ಕಳೆದ ಸುಮಾರು 3 ವರ್ಷಗಳ ಕಠಿಣ ಶ್ರಮದಿಂದ ಮೊದಲನೆಯ ಮಾದರಿ ಮಶಿನ್ ನನ್ನು ನಾವು ತಯಾರಿಸಿದೆವು. ಬೆಂಗಳೂರಿನ ‘ಲೋಹ ನಿರ್ಮಾಣ’ ಈ ಕಂಪನಿಯು ನಮ್ಮಲ್ಲಿ ವಿಶ್ವಾಸವನ್ನಿಟ್ಟು ಮೊದಲನೆಯ ಮಶಿನ್ ಖರೀದಿಸಿದರು. ನಮ್ಮ ಸಿ.ಎಮ್.ಎಮ್. ಮಶಿನ್ ಉತ್ಪಾದನೆಯ ಪ್ರವಾಸವು 1991-92 ರಿಂದ ಪ್ರಾರಂಭಗೊಂಡಿತು.
ಸಿ.ಎಮ್.ಎಮ್.ನಂತಹ ಅತ್ಯಾಧುನಿಕವಾದ ಮತ್ತು ದುಬಾರಿಯಾಗಿರುವ ಮಶಿನ್ ನ ನಿರ್ವಹಣೆಯ ಖರ್ಚು ಪೂರೈಸುವಂತೆ ಇರಬಲ್ಲದೇ? ಎಂಬ ಹೆದರಿಕೆಯು ಹಲವಾರು ಉದ್ಯಮಿಗಳ ಮನಸ್ಸಿನಲ್ಲಿರುತ್ತದೆ. ಮಶಿನ್ ನ ಬೆಲೆಯು ಇಷ್ಟು ಹೆಚ್ಚು ಇರುವುದರಿಂದ ಅದಕ್ಕೆ ಆಗಾಗ ಬೇಕಾಗುವ ಬಿಡಿ ಭಾಗಗಳೂ ತುಂಬಾ ದುಬಾರಿಯಾಗಿರಬಹುದು. ಮತ್ತು ಇದರಿಂದಾಗಿ ಕಾರ್ಖಾನೆಯಲ್ಲಿ ತಯಾರಿಸಿ ಬಳಸುವುದು ತಮ್ಮ ಕೈಗೆಟಕುವಂತಹದ್ದಲ್ಲ, ಎಂಬ ಅನುಮಾನವನ್ನು ಅನೇಕರು ವ್ಯಕ್ತಪಡಿಸಿದರು. ಆದರೆ ಇದೊಂದು ತಪ್ಪು ಕಲ್ಪನೆಯಾಗಿದೆ. ಈ ಮಶಿನ್ ಗಳು ಪ್ರಮುಖವಾಗಿ ಏರ್ ಬೇರಿಂಗ್ ನಲ್ಲಿ ಕೆಲಸ ನಿರ್ವಹಿಸುವುದರಿಂದ ಇದರಲ್ಲಿ ಒಂದಕ್ಕೊಂದು ತಿಕ್ಕಲ್ಪಟ್ಟು ಸವೆತವಾಗುವಂತಹ ಯಾವುದೇ ಭಾಗಗಳಿಲ್ಲ. ಇದರಿಂದಾಗಿ ಭಾಗಗಳನ್ನು ಸಾಮಾನ್ಯವಾಗಿ ಬದಲಾಯಿಸುವ ಅಗತ್ಯ ಇರುವುದಿಲ್ಲ. ಆದರೆ ನಿರ್ಧಾರಿತ ಸಮಯದ ನಂತರ ಮಶಿನ್ ನ ಕ್ಯಾಲಿಬ್ರೇಶನ್ ಮಾಡಿ ನಿರ್ದೋಷದ ಖಾತರಿಯನ್ನು ವಹಿಸುವುದು ಅತ್ಯಾವಶ್ಯವಾಗಿರುತ್ತದೆ. ಒಂದು ವೇಳೆ ಗ್ರಾಹಕನು ನಮ್ಮೊಂದಿಗೆ ಎ.ಎಮ್.ಸಿ. (ವಾರ್ಷಿಕ ನಿರ್ವಹಣೆಯ ಕರಾರು) ಮಾಡಿದ್ದಲ್ಲಿ ನಾವು ಈ ಕ್ಯಾಲಿಬ್ರೇಶನ್ ನ ಸಂಪೂರ್ಣವಾದ ಜವಾಬ್ದಾರಿಯನ್ನು ವಹಿಸುತ್ತೇವೆ.
ಈ ಪರಿಸ್ಥಿತಿಯಲ್ಲಿ ಬದಲಾಯಿಸಬೇಕಾಗಿರುವ ಇಲೆಕ್ಟ್ರಾನಿಕ್ ಭಾಗಗಳ (ಪಾರ್ಟ್) ಖರ್ಚು ಮಾತ್ರ ತುಂಬಾ ಹೆಚ್ಚು ಇರುತ್ತದೆ. ಆದರೆ ಈ ಖರ್ಚು ಕಾಲಕ್ಕೆ ತಕ್ಕಂತೆ ಬದಲಾಗುತ್ತದೆ. ಹಾಗೆಯೇ ಇಲೆಕ್ಟ್ರಾನಿಕ್ಸ್ ಪ್ರೋಬ್ ನಲ್ಲಿ ಅಳವಡಿಸಲಾಗಿರುವ ಸ್ಟೈಲಸ್ ತುಂಬಾ ಸಲ ಬದಲಾಯಿಸಬೇಕಾಗುತ್ತದೆ. ಆದರೆ ಅದರ ಖರ್ಚು ಎರಡರಿಂದ ಐದು ಸಾವಿರ ರೂಪಾಯಿಗಳಷ್ಟು ಇರುತ್ತದೆ.
ಅನೇಕ ಸವಾಲುಗಳನ್ನು ಎದುರಿಸುತ್ತಾ ವಿದೇಶದ ಉತ್ಪಾದನೆಗಳಿಗೆ ಸರಿಸಾಟಿಯಾದ ಉಪಕರಣಗಳನ್ನು ನಾವು ಉಪಲಬ್ಧ ಮಾಡಿಕೊಡುತ್ತಿದ್ದೇವೆ. ಹಾಗೆಯೇ ನಮ್ಮ ಉತ್ಪಾದನೆಗಳು ವಿದೇಶದ ಉತ್ಪಾದನೆಗಳ ಬೆಲೆಯ ಹೋಲಿಕೆಯಲ್ಲಿ ಸುಮಾರು ಶೇಕಡಾ 25 ರಿಂದ 40 ರಷ್ಟು ಅಗ್ಗವಾಗಿರುತ್ತವೆ. ಈ ಎರಡೂ ಅಂಶಗಳು ನಮ್ಮ ದೃಷ್ಟಿಯಲ್ಲಿ ಅಭಿಮಾನಾಸ್ಪದವಾಗಿವೆ.