ವಸ್ತ್ರೋದ್ಯೋಗದಲ್ಲಿ ಅನೇಕ ವಿಧದ ಮಶಿನ್ ಗಳನ್ನು ಬಳಸಲಾಗುತ್ತದೆ. ಈ ಮಶಿನ್ ನ ನಿರ್ಮಿತಿಯಲ್ಲಿ ಅಲಾಯ್ ಸ್ಟೀಲ್, ಸ್ಟೆನ್ ಲೆಸ್ ಸ್ಟೀಲ್, ಅಲ್ಯುಮಿನಿಯಮ್, ಫೋರ್ಜ್ಡ್ ಸ್ಟೀಲ್ ಇಂತಹ ಅನೇಕ ಪ್ರಕಾರದ ಮಟೀರಿಯಲ್ ಗಳನ್ನು ಬಳಸಲಾಗುತ್ತದೆ. ಈ ಮಶಿನ್ ನಲ್ಲಿ ಹೆಚ್ಚಾಗಿ ಎಲ್ಲ ಭಾಗಗಳು (ಪಾರ್ಟ್) ನಿರಂತರವಾಗಿ ಕಾರ್ಯನಿರತವಾಗಿರುತ್ತವೆ. ಇದರಿಂದಾಗಿ ಬಳಸಲಾಗುವ ಮಟೀರಿಯಲ್ ಸವೆತ ಪ್ರತಿರೋಧಕ, ಹಾಗೆಯೇ ಹೆಚ್ಚು ಬಾಳಿಕೆ ಬರುವುದು ಅತ್ಯಾವಶ್ಯಕವಾಗಿರುತ್ತದೆ. ಮಶಿನ್ ನ ಇನ್ನಿತರ ಸ್ಥಿರವಾದ ಭಾಗಗಳು ದೃಢವಾಗಿರುವುದೂ ಅಗತ್ಯದ್ದಾಗಿರುವುದರಿಂದ ಇದು ಫೋರ್ಜ್ಡ್ ಸ್ಟೀಲ್ ಅಥವಾ ಕಾಸ್ಟಿಂಗ್ ನಿಂದ ತಯಾರಿಸಲಾಗುತ್ತದೆ.
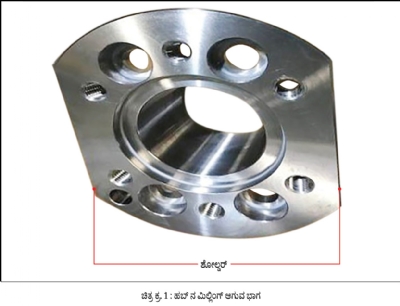
ನಮ್ಮ ಗ್ರಾಹಕರೊಬ್ಬರು ವಸ್ತ್ರೋದ್ಯೋಗಕ್ಕೋಸ್ಕರ ಬೇಕಾಗುವ ಯಂತ್ರಭಾಗಗಳ ಉತ್ಪಾದನೆಯನ್ನು ಮಾಡುತ್ತಾರೆ. ಸದ್ಯಕ್ಕೆ ವಾಹನ ಉದ್ಯಮಕ್ಕೆ ಬೇಕಾಗುವ ಭಾಗಗಳ ಉತ್ಪಾದನೆಯನ್ನು ಕಡಿಮೆ ಪ್ರಮಾಣದಲ್ಲಿ ಮಾಡಲಾಗುತ್ತದೆ. ಆದರೆ ಮಾರಾಟಗಾರರು ಅಥವಾ ಪೂರೈಕೆಗಾರರಿಗೆ ಅವರಲ್ಲಿರುವ ಮಶಿನ್ ಕೆಲಸ ನಿರ್ವಹಿಸುವಂತೆ ಇಡಬೇಕಾಗಿರುವುದರಿಂದ ಅವರು ವಾಹನ ಉದ್ಯಮಕ್ಕೆ ಹೊರತಾಗಿ ಇನ್ನಿತರ ಉದ್ಯಮಗಳ ಕಡೆಗೆ ಗಮನ ಹರಿಸುವುದಿಲ್ಲ. ವಸ್ತ್ರೋದ್ಯೋಗದಲ್ಲಿ ಬಳಸಲಾಗುತ್ತಿರುವ ಮಶಿನ್ ಗಳ ಸಂಖ್ಯೆಯೂ ಗಮನಾರ್ಹವಾಗಿ ಹೆಚ್ಚುತ್ತಿದೆ. ಪೂರೈಕೆದಾರರು ಉದ್ಯಮಗಳಿಗೆ ಬೇಕಾಗುವ ಒಂದೇ ರೀತಿಯ ಯಂತ್ರಭಾಗಗಳಲ್ಲಿ ಅವಲಂಬಿಸಿ ಇರಬಾರದು. ಈ ಭಾಗಗಳನ್ನು ಒಂದೇ ರೀತಿಯಲ್ಲಿ ನಿರಂತರವಾಗಿ ತಯಾರಿಸದೇ ವಿವಿಧ ಬ್ಯಾಚ್ ಗಳಲ್ಲಿ ತಯಾರಿಸಲಾಗುತ್ತದೆ.
ನಮ್ಮ ಗ್ರಾಹಕರು ಹಬ್, ಪಿನ್, ಶಾಫ್ಟ್ ಮತ್ತು ಹೌಸಿಂಗ್ ವಸ್ತ್ರೋದ್ಯೋಗಕ್ಕೋಸ್ಕರ ಬೇಕಾಗುವ ಯಂತ್ರಭಾಗಗಳ ಉತ್ಪಾದಕರಾಗಿದ್ದು, ಯಂತ್ರಭಾಗಗಳಲ್ಲಿ ಒಂದಾದ ಹಬ್, ಫೋರ್ಜ್ಡ್ ಸ್ಟೀಲ್ ನಿಂದ ತಯಾರಿಸಲಾಗಿರುತ್ತದೆ. ಈ ಯಂತ್ರಭಾಗಗಳು ವಿವಿಧ ಆಕಾರಗಳಲ್ಲಿ ಮತ್ತು ಸ್ಪರೂಪದಲ್ಲಿ ತಯಾರಿಸಲ್ಪಡುತ್ತಿರುವುದರಿಂದ ಹೆಚ್ಚುವರಿ ಮಟೀರಿಯಲ್ ತೆಗೆಯುವ ಪ್ರಮಾಣವೂ (ಸ್ಟಾಕ್ ರಿಮೂವಲ್) ಹೆಚ್ಚು ಇರುತ್ತದೆ. ಕಾರಣ ಅಂತಿಮ ಯಂತ್ರಭಾಗಗಳು ಸಿಲಿಂಡ್ರಿಕಲ್ ಆಕಾರದಲ್ಲಿರುವ ಕಚ್ಚಾ ವಸ್ತುಗಳ ಯಂತ್ರಣೆಯನ್ನು ಮಾಡಿ ತಯಾರಿಸಬೇಕಾಗುತ್ತದೆ.
ಬೇಡಿಕೆಯಲ್ಲಿ ಮತ್ತು ಪ್ರಮಾಣದಲ್ಲಿ ಅಕಸ್ಮಾತ್ತಾಗಿ ಹೆಚ್ಚಳವಾಗಿದ್ದರಿಂದ ಗ್ರಾಹಕರಿಗೆ ಉತ್ಪಾದನೆಯ ಸಾಮರ್ಥ್ಯವನ್ನು ಹೆಚ್ಚಿಸುವುದು ಕಠಿಣವಾಗುತ್ತದೆ. ಹಾಗೆಯೇ ಈ ಯಂತ್ರಭಾಗಗಳ ಯಂತ್ರಣೆಯನ್ನು ಸದ್ಯದ ಸೆಟಪ್ ನಲ್ಲಿಯೇ ಮಾಡುವುದು ಅನಿವಾರ್ಯವಾಗುತ್ತದೆ. ಇದಕ್ಕೋಸ್ಕರ ಟರ್ನಿಂಗ್, ಡ್ರಿಲ್ಲಿಂಗ್, ಮಿಲ್ಲಿಂಗ್, ಹೀಟ್ ಟ್ರೀಟ್ ಮೆಂಟ್, ಗ್ರೈಂಡಿಂಗ್ ಇಂತಹ ಪ್ರಕ್ರಿಯೆಗಳನ್ನು ಮಾಡಲಾಗುತ್ತಿತ್ತು. ಇದಕ್ಕೋಸ್ಕರ ನಾವು ಎಲ್ಲ ಪ್ರಕ್ರಿಯೆಗಳ ಅಭ್ಯಾಸವನ್ನು ಮಾಡಿದೆವು. ಫ್ಲಂಜ್ ನ ಬದಿಯ ಯಂತ್ರಣೆಯನ್ನು ಹೆಚ್ಚು ಪ್ರಮಾಣದಲ್ಲಿ ಮಾಡಬೇಕಾಗುತ್ತದೆ, ಆಗ ಯಂತ್ರಣೆಯಲ್ಲಿ ಗರಿಷ್ಠ ಸಮಯವು ಮಿಲ್ಲಿಂಗ್ ಮಶಿನ್ ಗೆ ಬೇಕಾಗುತ್ತದೆ, ಎಂಬುದು ನಮ್ಮ ಗಮನಕ್ಕೆ ಬಂತು. ಚಿತ್ರ ಕ್ರ. 1 ರಲ್ಲಿ ತೋರಿಸಿದಂತೆ ಎರಡೂ ಬದಿಗಳಲ್ಲಿ ಯಂತ್ರಣೆಯು ಹೆಚ್ಚು ಇದೆ. ಇದರ ಹೊರತಾಗಿ ಇತ್ತೀಚಿನ ಪ್ರಕ್ರಿಯೆಯಲ್ಲಿ ಅತ್ಯಾವಶ್ಯಕವಾಗಿರುವ ಪಾಸ್ ಗಳ ಸಂಖ್ಯೆಯೂ ಹೆಚ್ಚಾಗಿತ್ತು. ಇದಕ್ಕೋಸ್ಕರ ನಾವು ಮಿಲ್ಲಿಂಗ್ ಗೆ ಬಳಸಲಾಗುವ ಪ್ರಕೃತ ಟೂಲಿಂಗ್ ಕೂಡಾ ಪರಿಶೀಲಿಸಿದೆವು.
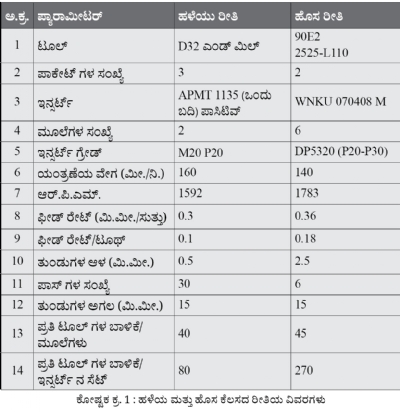
ಸದ್ಯದ ರೀತಿಯಲ್ಲಿ ಬಳಸಲಾಗುವ ಇನ್ಸರ್ಟ್ ಎರಡು ಮೂಲೆಗಳ 90˚ ಕೋನದಲ್ಲಿ ಪ್ರವೇಶಿಸಿತ್ತು. ಆದರೆ ಕಟರ್ ನ ವ್ಯಾಸವು 32 ಮಿ.ಮೀ. ಮತ್ತು ಅದಕ್ಕೆ 3 ಪಾಕೇಟ್ ಇತ್ತು. ತುಂಡುಗಳ ಅಗಲ 15 ಮಿ.ಮೀ. ಇತ್ತು. ಪ್ಯಾರಾಮೀಟರ್ ಮತ್ತು ಟೂಲಿಂಗ್ ನ ವಿವರಗಳನ್ನು ಕೋಷ್ಟಕ ಕ್ರ. 1 ರಲ್ಲಿ ನೀಡಲಾಗಿದೆ. ಇದರಲ್ಲಿ ಇನ್ಸರ್ಟ್ ನ ಸವೆತವೂ ಬೇಗನೇ ಆಗುತ್ತಿತ್ತು ಮತ್ತು ಯಂತ್ರಣೆಯಲ್ಲಿ ಅದರ ತುಂಡುಗಳು ಉಂಟಾಗುವ ಸಮಸ್ಯೆಯೂ ಇತ್ತು. ಯಂತ್ರಣೆಯ ಸಮಯವೂ ಜಾಸ್ತಿ ಇತ್ತು. ಆವಶ್ಯಕವಿರುವ ಉತ್ಪಾದನೆಯ ಪ್ರಮಾಣವು ಹೆಚ್ಚಿದ್ದರಿಂದ ಸದ್ಯದ ಟೂಲಿಂಗ್ ಮತ್ತು ಪ್ರಕ್ರಿಯೆಯ ಪ್ಯಾರಾಮೀಟರ್ ಬಳಸಿ ಆವಶ್ಯಕವಿರುವ ಪ್ರಮಾಣದಲ್ಲಿ ಉತ್ಪಾದನೆಯನ್ನು ಪೂರೈಸುವುದು ಗ್ರಾಹಕರಿಗೆ ಸಾಧ್ಯವಿರಲಿಲ್ಲ.
ಯಂತ್ರಭಾಗಗಳು : ಹಬ್
ಮಟೀರಿಯಲ್ : ಫೋರ್ಜ್ಡ್ ಸ್ಟೀಲ್
ಪ್ರಕ್ರಿಯೆ : ಫೇಸ್ ಮತ್ತು ಶೋಲ್ಡರ್ ಮಿಲ್ಲಿಂಗ್
ಮಶಿನ್ : ವಿ.ಎಮ್.ಸಿ. BT40 ಟೇಪರ್
ಸ್ಪಿಂಡಲ್ ನ ಶಕ್ತಿ : 12 kW
ಮಶಿನ್ ನ ಗರಿಷ್ಠ ಆರ್.ಪಿ.ಎಮ್. : 4000
ಪ್ರಕೃತ ಪ್ರಕ್ರಿಯೆಯಲ್ಲಿರುವ ಸಮಸ್ಯೆಗಳು
1. ಟೂಲ್ ನ ಬಾಳಿಕೆಯು ಕಡಿಮೆ : ಟೂಲ್ ನ ಸವೆತವು ಹೆಚ್ಚು
2. ಟೂಲ್ ನಿಂದ ಚಿಪ್ ಹೊರಬರುವುದು.
3. ಕಡಿಮೆ ಉತ್ಪಾದನೆಯ ಸಾಮರ್ಥ್ಯ
4. ಪ್ರತಿಯೊಂದು ಯಂತ್ರಭಾಗಗಳ ಖರ್ಚು
ನಾವು ಪ್ರಕ್ರಿಯೆ ಮತ್ತು ಭಾಗಗಳ ಯಂತ್ರಣೆಯನ್ನು ಮಾಡುವ ರೀತಿಯನ್ನು ಪರಿಶೀಲಿಸಿದೆವು. ತುಂಡುಗಳ ಅಗಲ 15 ಮಿ.ಮೀ. ಇರುವುದರಿಂದ ದೊಡ್ಡ ಆಕಾರದ ಕಟರ್ ಬಳಸುವ ಆವಶ್ಯಕತೆ ಇರಲಿಲ್ಲ. ಇದರಿಂದಾಗಿ ಯಂತ್ರಭಾಗಗಳಲ್ಲಿ ಯಂತ್ರಣೆಯ ಭಾರವು ಉಂಟಾಗುವ ಸಮಸ್ಯೆ ಉಂಟಾಗುತ್ತಿತ್ತು. ಅದಕ್ಕೋಸ್ಕರ ನಾವು D32 ಕಟರ್ ನ ಬದಲಿಗೆ D25 ಕಟರ್ ಬಳಸುವುದನ್ನು ಸೂಚಿಸಿದೆವು. ಹಾಗೆಯೇ ಈ ಹಿಂದೆ ಬಳಸಿರುವ 2 ಮೂಲೆಗಳ ಇನ್ಸರ್ಟ್ ಗಳ ಬದಲಾಗಿ 6 ಮೂಲೆಗಳಿರುವ ಮತ್ತು ಹೆಚ್ಚು ಹೆಲಿಕ್ಸ್ ಇರುವ ಇನ್ಸರ್ಟ್ ಗಳನ್ನು ಬಳಸುವುದನ್ನೂ ಸೂಚಿಸಿದೆವು. ಇದರಿಂದಾಗಿ ಕಂಪನಗಳು ಮತ್ತು ಯಂತ್ರಣೆಯ ಬಲವು ಕಡಿಮೆ ಮಾಡುವುದು ಸಾಧ್ಯವಾಯಿತು. ಹಾಗೆಯೇ 6 ಮೂಲೆಗಳಿರುವ ಇನ್ಸರ್ಟ್ ನ ವೈಶಿಷ್ಟ್ಯಪೂರ್ಣವಾದ ಜಾಮೆಟ್ರಿಯಿಂದಾಗಿ ಫೀಡ್ ರೇಟ್ ಹೆಚ್ಚಿಸುವುದು ಸಾಧ್ಯವಾಯಿತು. ಸದ್ಯದ ಪಾಸ್ ಗಳ ಸಂಖ್ಯೆಯು ಹೆಚ್ಚು ಇತ್ತು ಮತ್ತು ತುಂಡುಗಳ ಆಳವೂ ಕಡಿಮೆ ಇತ್ತು. ಆದರೆ ಮಶಿನ್ ನ ಹೆಚ್ಚುವರಿ ತುಂಡುಗಳಿಗೆ ಆಳ ಮತ್ತು ಹೆಚ್ಚುವರಿ ಫೀಡ್ ರೇಟ್ ಪಡೆಯುವ ಸಾಮರ್ಥ್ಯ ಇರುವುದೂ ಕಂಡುಬಂತು. ಇದರಿಂದಾಗಿ ತುಂಡುಗಳ ಆಳವನ್ನು ಹೆಚ್ಚಿಸಿ ಪಾಸ್ ಗಳ ಸಂಖ್ಯೆ ಕಡಿಮೆ ಮಾಡಲಾಯಿತು. ಇದರಿಂದಾಗಿ ಸೈಕಲ್ ಟೈಮ್ ಕಡಿಮೆ ಮಾಡುವುದು ಸುಲಭವಾಯಿತು ಮತ್ತು ಉತ್ಪಾದನೆಯ ಸಾಮರ್ಥ್ಯವನ್ನು ಹೆಚ್ಚಿಸುವುದೂ ಸಾಧ್ಯವಾಯಿತು.
ತಿಳಿದುಕೊಂಡಿರುವ ಅಂಶಗಳು
ಎ. ಮಶಿನ್ ನ ಸಾಮರ್ಥ್ಯವನ್ನು ಪರಿಶೀಲಿಸುವುದು, ಹಾಗೆಯೇ ಮಶಿನ್ ಬಳಕೆಯನ್ನು ಗರಿಷ್ಠ ಪ್ರಮಾಣದಲ್ಲಿ ಮಾಡುವುದು.
ಬಿ. ರಫ್ ಮಿಲ್ಲಿಂಗ್ ನಲ್ಲಿ ಕಡಿಮೆ ವೇಗವನ್ನು ಅಳವಡಿಸಿ ಹೆಚ್ಚು ಫೀಡ್ ರೇಟ್ ತನಕ ತಲುಪುವ ಪ್ರಯತ್ನ ಮಾಡುವುದು, ಇದರಿಂದಾಗಿ ಸೈಕಲ್ ಟೈಮ್ ಕಡಿಮೆಯಾಗಲು ಸಹಾಯವಾಗಬಹುದು. ಟೂಲ್ ನ ಬಾಳಿಕೆ ಹೆಚ್ಚಬಲ್ಲದು ಮತ್ತು ಉತ್ಪಾದಕತೆಯೂ ಸುಧಾರಿಸಬಲ್ಲದು.
ಸಿ. ಇನ್ಸರ್ಟ್ ನ ಶ್ರೇಣಿಯ ಆಯ್ಕೆ (ರಫ್ ಮಿಲ್ಲಿಂಗ್ ಗೋಸ್ಕರ ಹೆಚ್ಚು ಟಫ್)
ಡಿ. ಟೂಲ್ ನ ದಾರಿ ಯಾವಾಗಲೂ ಫಿಕ್ಸ್ಚರ್ ಕ್ಲಾಂಪಿಂಗ್ ನ ಶಕ್ತಿಯ ದಿಕ್ಕಿನಲ್ಲಿರಬೇಕು (ಡೌನ್ ಮಿಲ್ಲಿಂಗ್).
ಇ. ಚಿಪ್ ಸಿಲುಕುವುದನ್ನು ತಡೆಯಲು ಮತ್ತು ಅಡಚಣೆ ರಹಿತವಾದ ಯಂತ್ರಣೆಗೋಸ್ಕರ ಸೂಕ್ತವಾದ ಕೂಲಂಟ್ ನ ಬಳಕೆ.
ಫೀಡ್ ರೇಟ್ ಮತ್ತು ತುಂಡುಗಳ ಆಳ ಹೆಚ್ಚಿಸಿದ್ದರಿಂದ ನಮಗೆ ಉತ್ಪಾದಕತೆಯನ್ನು ಹೆಚ್ಚಿಸುವುದು ಸಾಧ್ಯವಾಯಿತು. ಸೈಕಲ್ ಟೈಮ್ ಸುಮಾರು ಶೇಕಡಾ 50 ರಷ್ಟು ಕಡಿಮೆ ಆಯಿತು. ಇದರ ಹೊರತಾಗಿ ಮೊದಲು ಬಳಸಲಾಗುತ್ತಿದ್ದ 2 ಮೂಲೆಗಳ ಇನ್ಸರ್ಟ್ ಗಳ ಬದಲಾಗಿ ಹೊಸದಾಗಿ ಬಳಸಲಾಗುವ ಇನ್ಸರ್ಟ್ ಗೆ 4 ಮೂಲೆಗಳಿರುವುದರಿಂದ 4 ಹೆಚ್ಚು ಮೂಲೆಗಳ ಲಾಭವೂ ಆಯಿತು. ಇದರಿಂದಾಗಿ ಪ್ರತಿಯೊಂದು ಶಿಪ್ಟ್ ನಲ್ಲಿ ಬಳಸಲಾಗುವ ಇನ್ಸರ್ಟ್ ಗಳ ಸಂಖ್ಯೆಯನ್ನು ಕಡಿಮೆ ಮಾಡುವುದು ಸಾಧ್ಯವಾಯಿತು.
ಪ್ಯಾರಾಮೀಟರ್ ಮತ್ತು ಟೂಲಿಂಗ್ ಬದಲಾವಣೆಯಿಂದಾಗಿ ಆಗಿರುವ ಲಾಭಗಳು
1. ಟೂಲ್ ಗಳ ಬಾಳಿಕೆ ಶೇಕಡಾ 13 ರಷ್ಟು ಹೆಚ್ಚಾಯಿತು. (ಪ್ರತಿಯೊಂದು ಟೂಲ್ ಗೋಸ್ಕರ ಶೇಕಡಾ 100 ಕ್ಕಿಂತ ಹೆಚ್ಚು ಹೆಚ್ಚಳ).
2. ಹೆಚ್ಚುವರಿ 4 ಮೂಲೆಗಳು.
3. ಉತ್ಪಾದಕತೆಯು ಶೇಕಡಾ 50 ರಷ್ಟು ಹೆಚ್ಚಾಯಿತು.
4. ಪ್ರತಿಯೊಂದು ಯಂತ್ರಭಾಗದ ಖರ್ಚು ಶೇಕಡಾ 56 ರಷ್ಟು ಕಡಿಮೆಯಾಯಿತು.
5. ಇನ್ಸರ್ಟ್ ನ ಬಳಕೆಯೂ ಕಡಿಮೆಯಾಯಿತು.
6. D32 ಕಟರ್ ಮತ್ತು D25 ಕಟರ್ ನ ಬೆಲೆಯಲ್ಲಿ ಸುಮಾರು ಶೇಕಡಾ 15 ರಷ್ಟು ವ್ಯತ್ಯಾಸವಾಯಿತು.
7. ಎರಡೂ ಮೂಲೆಗಳ ಇನ್ಸರ್ಟ್ ಗಿಂತ ಆರು ಮೂಲೆಗಳ ಇನ್ಸರ್ಟ್ ನ ಬೆಲೆಯು ಇಮ್ಮಡಿ ಇದೆ. ಈ ಬೆಲೆಯು ಹೆಚ್ಚು ಇದ್ದರೂ ಕೂಡಾ ನಾವು ಪ್ರತಿಯೊಂದು ಯಂತ್ರಭಾಗದ ಖರ್ಚಿನಲ್ಲಿ ರೂಪಾಯಿ 4.6 ರಷ್ಟು ಕಡಿತವನ್ನು ಮಾಡಿದೆವು. ಹಾಗೆಯೇ ಇನ್ಸರ್ಟ್ ನ ಬಳಕೆಯು ಪ್ರತಿ ತಿಂಗಳಿಗೆ 675 ರಿಂದ 260 ರಷ್ಟು ಕಡಿಮೆಯಾಯಿತು. ಇದರಿಂದಾಗಿ ಇನ್ಸರ್ಟ್ ನ ಇನ್ವೆಂಟರಿಯಲ್ಲಿ ಗಮನಾರ್ಹವಾದ ಇಳಿತವಾಯಿತು.